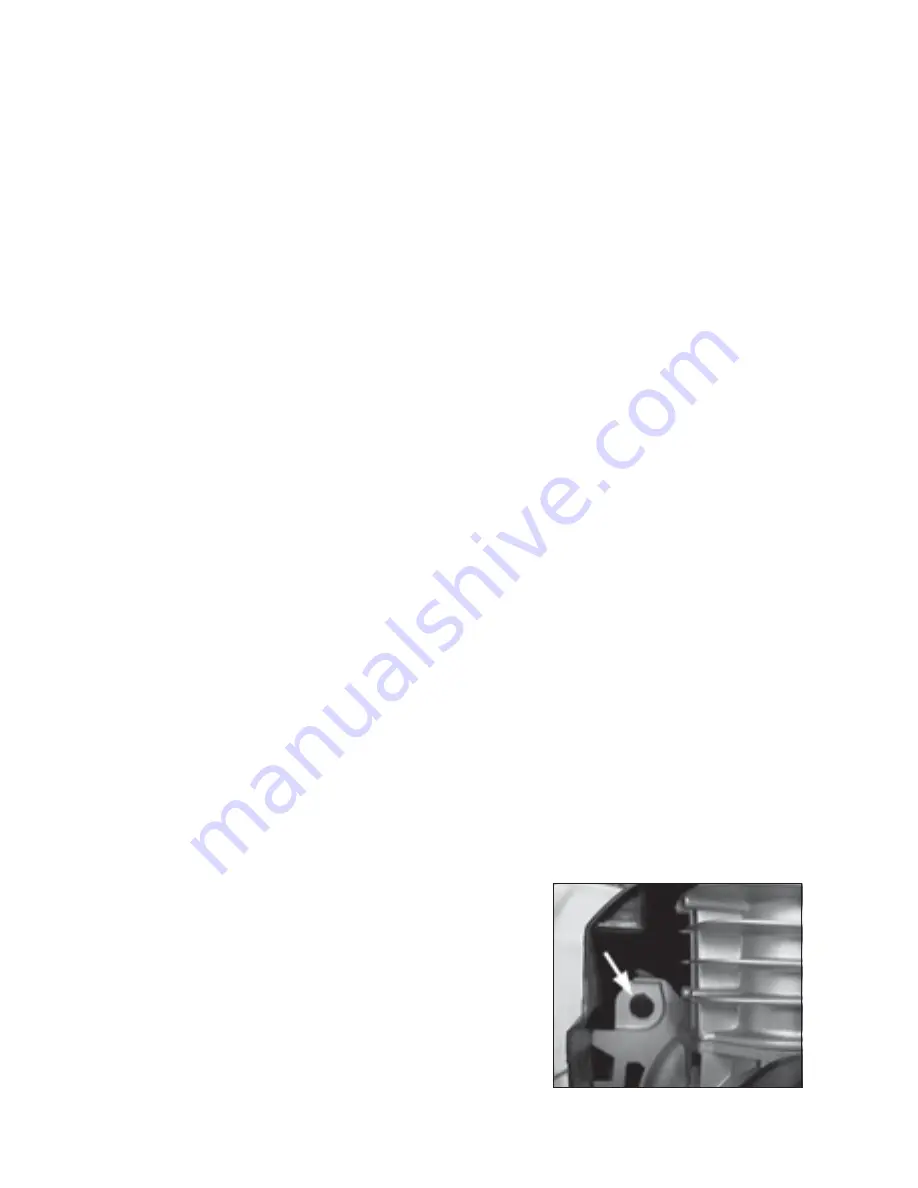
7
3.
To start the compressor pull UP the ON/OFF knob to the ‘ON’ (I) position - the
motor should start immediately.
Note: Should the motor fail to start immediately, it is probable that the air receiver
is already full of air. Check the tank pressure gauge (see fig. 2). If you release air,
by opening air outlet tap, the motor will start automatically once the cut-in pressure
is reached.
4.
Before connecting your airline to the compressor allow it to run with the air
outlet tap completely open for 10 to 15 seconds to permit a good distribution
of the lubricating oil.
5.
Close the outlet tap then connect one end of suitable air hose to the
compressor air outlet, and the other and to the equipment to be used.
Set the outlet pressure by adjusting the Output Pressure Regulator. To do this,
turn the knob clockwise to increase pressure, anti-clockwise to decrease.
Align your desired pressure setting, shown on the top of the regulator knob,
with the arrow on the casing.
Note: For most spraywork do not exceed 50 psi (unless following paint manuf-
acturer’s instructions).
For other airline equipment such as air tools, tyre gauges, staple guns, paraffin
guns etc., it may be necessary to set the operating pressure at a higher (or lower)
level.
IMPORTANT:
Always refer to the accessory manufacturers’ recommendations
for optimum operating pressures for their equipment.
6.
With operating pressure set, reopen the air outlet tap.
7.
The Pressure Switch, located within the plastic cover beneath the ON/OFF
knob, should not require adjustment. This is an automatic device and has
been preset at the factory to stop the motor when pressure in the receiver
reaches its maximum, and to start it again when the pressure falls to the
minimum preset value. This operation is completely automatic and does not
affect the spraying process in any way. However, should problems develop
with the cut-in, cut out settings, consult your local Clarke dealer.
Fig. 3
Note:
a.
If the machine pumps continuously
without cutting out then the compressor is
too small for the application/tool being used,
and damage may result. Consult your local
Clarke dealer.
b.
The motor is protected by a Thermal Overload
so that if the motor overheats for any reason
-the thermal overload will trip, stopping the
motor. To restart, allow a period for the motor
to cool down, (approx 5 mins), before
pressing the Reset Button, arrowed in fig. 3.
and shown at ‘C’, fig.6