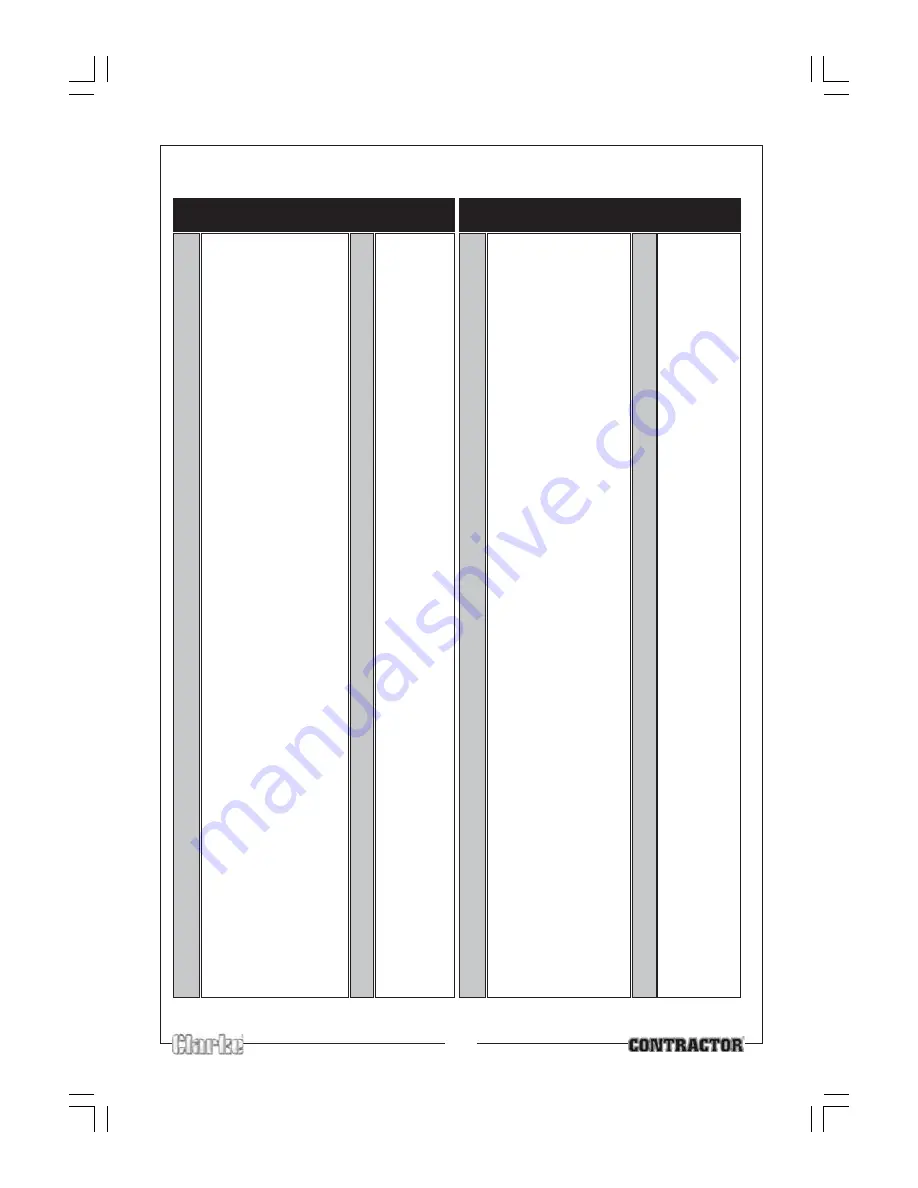
28
No. Description
Qty Part No
No. Description
Qty Part No
81
Slide bar clamp
4
DDCTS12081
82
Left guard
1
DDCTS12082
83
Screw
1
DDCTS12083
84
Handle 2
1
DDCTS12084
85
Handle 1
1
DDCTS12085
86
Handle cover
1
DDCTS12086
87
Hand wheel B
1
DDCTS12087
88
Hand wheel A
1
DDCTS12088
89
Screw
1
DDCTS12089
90
Indicator
1
DDCTS12090
91
Front table
1
DDCTS12091
92
Rock
1
DDCTS12092
93
Nut
3
DDCTS12093
94
Protection plate
1
DDCTS12094
95
Torque spring
1
DDCTS12095
96
Small plate
1
DDCTS12096
97
Big washer
1
DDCTS12097
98
Riving knife bracket
1
DDCTS12098
99
Retaining ring
1
DDCTS12099
100
Lower Blade Guard A
1
DDCTS12100
101
Shaft assy
1
DDCTS12101
102
Blade
1
DDCTS12102
103
Nut
1
DDCTS12103
103
Lower Blade Guard B
1
DDCTS12104
105
Blade flange
1
DDCTS12105
106
Bolt
1
DDCTS12106
107
Big washer
1
DDCTS12107
108
Riving knife clamp
1
DDCTS12108
109
Screw
4
DDCTS12109
110
Spring washer
4
DDCTS12110
111
Flat washer
4
DDCTS12111
112
Riving knife bracket
1
DDCTS12112
113
Nut
5
DDCTS12113
114
Screw
4
DDCTS12114
115
Bearing
2
DDCTS12115
116
Retain ring
1
DDCTS12116
117
Screw
4
DDCTS12117
118
Spring washer
4
DDCTS12118
119
Support bar
1
DDCTS12119
120
Screw
2
DDCTS12120
121
Threaded spindle
2
DDCTS12121
122
Bolt
2
DDCTS12122
123
Spring
2
DDCTS12123
124
Gear
1
DDCTS12124
125
Belt
1
DDCTS12125
126
Drive wheel
1
DDCTS12126
127
Clamp 2
1
DDCTS12127
128
Spring
4
DDCTS12128
129
Motor assy
1
DDCTS12129
130
Bolt
2
DDCTS12130
131
Screw
1
DDCTS12131
132
Big washer
7
DDCTS12132
133
Screw
1
DDCTS12133
134
Drive wheel
1
DDCTS12134
135
Motor Bracket
1
DDCTS12135
136
Guide Bracket
1
DDCTS12136
137
Threaded bar
1
DDCTS12137
138
Pin
1
DDCTS12138
139
Clamping bracket
1
DDCTS12139
140
Drive shaft assy
1
DDCTS12140
141
Bolt
1
DDCTS12141
142
Washer
1
DDCTS12142
143
Locking handle
1
DDCTS12143
144
Pin
1
DDCTS12144
145
Sleeve
1
DDCTS12145
146
Slide block
3
DDCTS12146
147
Spring
8
DDCTS12147
148
Rip fence Slide
1
DDCTS12148
149
Spring
1
DDCTS12149
150
Scale
1
DDCTS12150
151
Flat washer
7
DDCTS12151
152
Bracket assy
1
DDCTS12152
153
Spring
4
DDCTS12153
154
Washer
1
DDCTS12154
154
Spindle retaining ring
1
DDCTS12155
156
Blade fixing knob
2
DDCTS12156
157
Motor switch
1
DDCTS12157