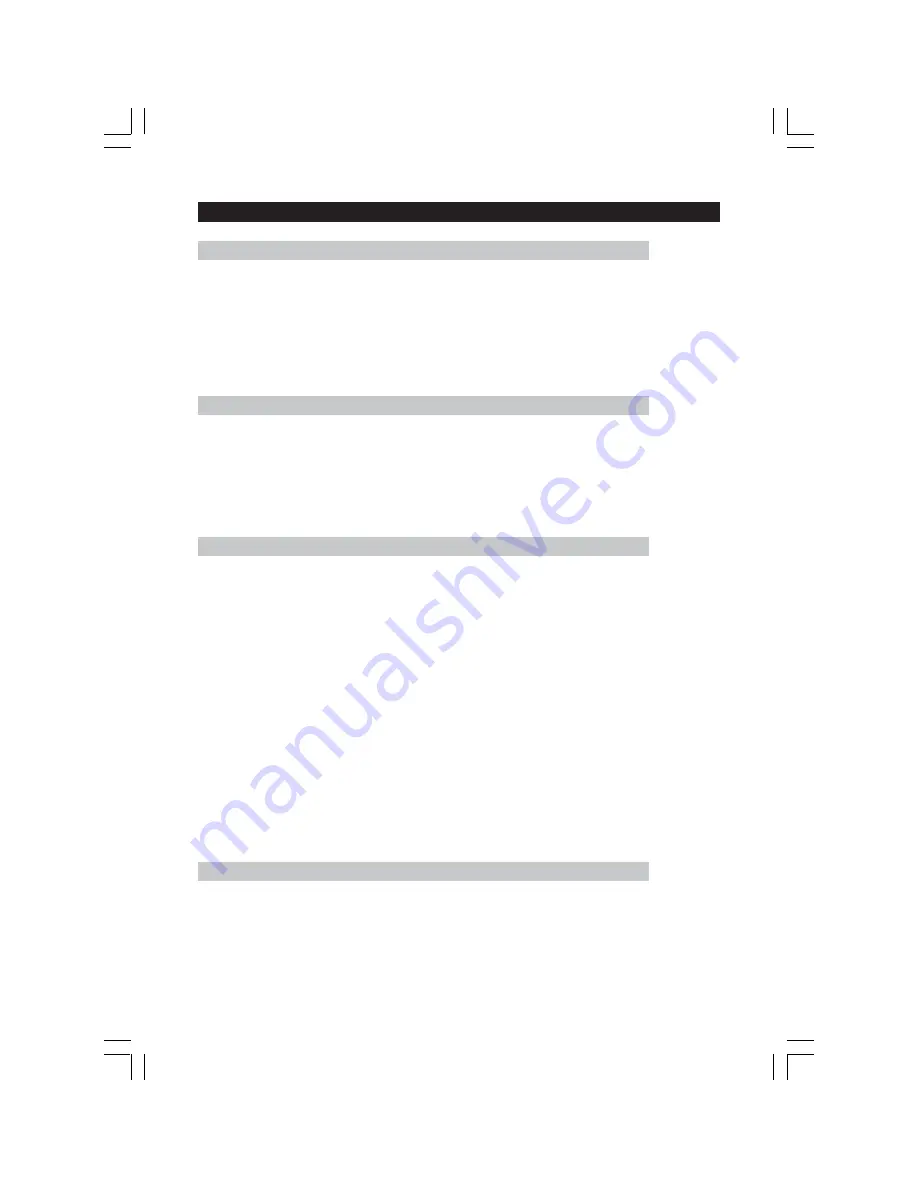
MAINTENANCE
(A) EYESHIELD and SPARK ARRESTER BRACKET ADJUSTMENT
The see-through eye shields allow the user to see the operation clearly and to work
precisely. The eye shields can be adjusted up and down to suit operator.
The Spark Arrester brackets should be adjusted so that they are as close as possible
to the wheel without impairing the wheels rotation.
IMPORTANT: Even though the Eye Shields are fitted, you should nevertheless
ALWAYS wear safety goggles when operating a grinding machine.
(B) TOOLREST ADJUSTMENT
The appropriate adjustment of the Tool Rests provides the operator with a correct
working angle and a firm and efficient base for working. Adjustments can be
made by loosening the mounting screws and moving the Tool Rest to within 1/16”
(1.6mm) from the wheel. Due to the wear on the grinding wheel, it will be
necessary to adjust the Tool Rests from time to time. Always re-tighten the
mounting screws once adjustment is complete.
(C) CHANGING THE GRINDING WHEEL
To renew or change the grinding wheels, follow the steps given below.
1. Switch off and un-plug from mains power supply. Disassemble outer covers,
left or right, by removing the three cover retaining nuts, bolts and washers.
2. Slacken the Spark Arrester bracket and Tool Rest mounting screws, and pull
the bracket and Tool Rest away from the wheel.
3. Hold the grinding wheel firmly and remove the nut and flange from the shaft,
noting that the
left hand wheel nut has a left hand thread.
4. Take off the used wheel and replace with the new one, ensuring:
a. the paper blotters are in place either side of the wheel.
b. that there is a good balanced rotation of the grinding wheel, and
c. you do not overtighten the wheel nut.
5. Readjust the Tool Rest and Spark Arrester Brackets as described above.
6. Switch ON the machine and allow it to rotate freely for at least one minute.
(D) DRESSING THE WHEEL
It will be necessary from time to time to dress the wheel to obtain a true working
surface.This should be done ONLY with an approved dressing tool, which can be
obtained from your CLARKE dealer, quoting Model No. GWD-1. Part No. 6501120.
7
Summary of Contents for CBG6RP
Page 1: ...BENCH GRINDER MODEL CBG6RP OPERATING MAINTENANCE INSTRUCTIONS 0101...
Page 2: ......
Page 11: ...9 PARTS DIAGRAM...
Page 12: ......