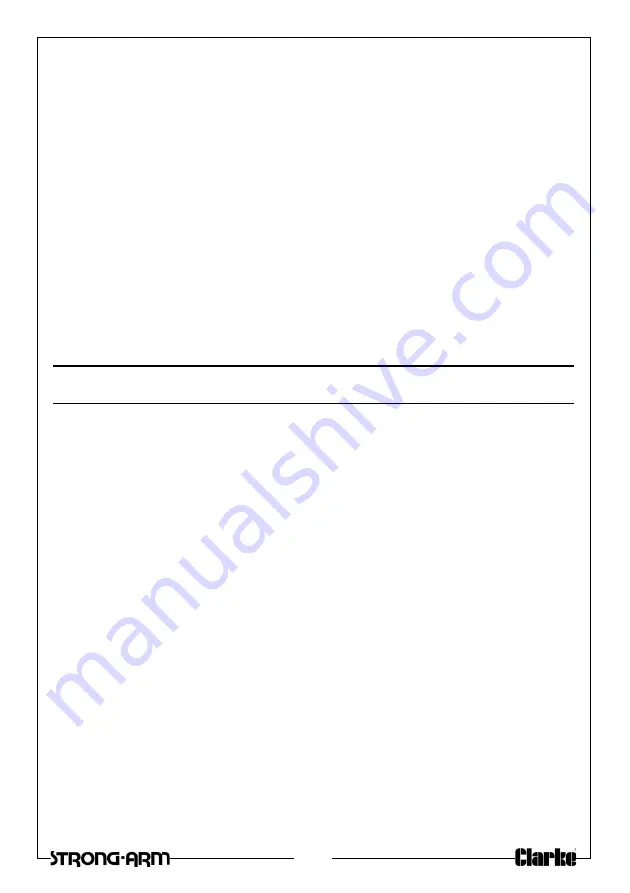
7
7. Ensure that the axle stands cannot move when supporting the load and
are on firm, level ground. Use suitable wheel chocks to stop the vehicle
from moving.
NOTE:
The jack may move slightly during operation. It is important
therefore, that the floor is clean and completely free from debris.
8. To stop it lowering at any point, turn the handle clockwise again. Always
avoid a rapid descent by turning the handle slowly.
9. Carefully lower the vehicle onto the axle stand, checking constantly,
preferably with an assistant, that the vehicles jacking point rests snugly and
cleanly on the axle stand, and that the stand is stable before the weight is
taken.
NOTE:
Ensure this operation is carried out under complete control. DO
NOT allow the load to drop suddenly as this could damage
internal parts.
Completely remove the jack from the vehicle.
MAINTENANCE
GENERAL CARE
1. When the jack is not in use, keep the ram fully lowered and the release
valve closed.
2. Keep the jack clean and occasionally apply lubricating oil to all pivot
points, front wheels & rear castors.
3. Periodically check the oil level as follows.
4. Check the pump piston and piston rod periodically for signs of corrosion.
Clean exposed areas with a clean oiled cloth.
5. In the event of damage or broken components, replacements are
available from Clarke Parts & Service.
CHECKING /MAINTAINING THE OIL LEVEL
If the jack has been stored for long periods, check for oil leaks before use. If
necessary, check the oil level as follows:
1. Ensure the jack is fully lowered by turning the control valve fully anti-
clockwise.
Summary of Contents for 7623032
Page 2: ...2...
Page 10: ...10 DECLARATION OF CONFORMITY...
Page 11: ...11 COMPONENT PARTS RAM ASSEMBLY...
Page 13: ...13 COMPONENT PARTS GENERAL ASSEMBLY...
Page 15: ...15...
Page 16: ......