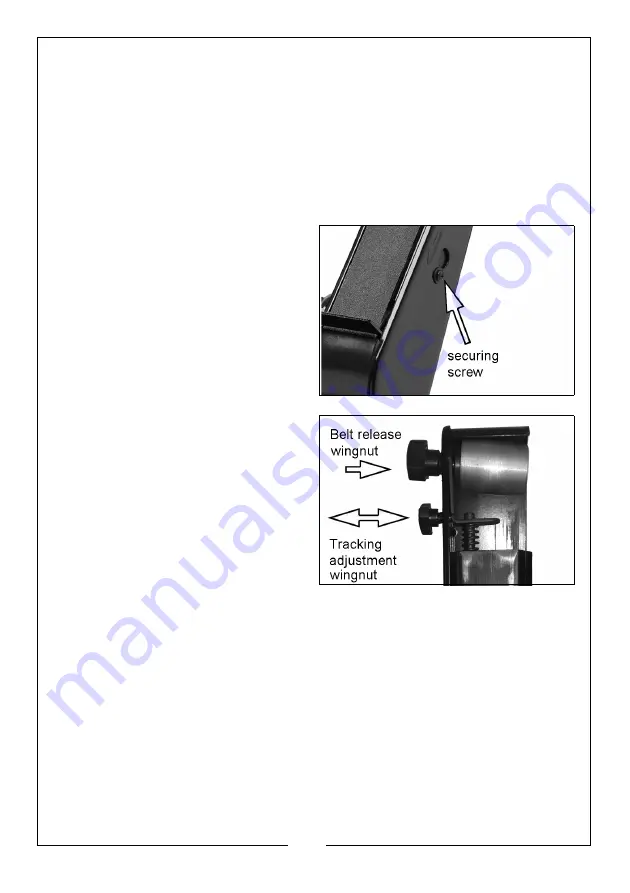
15
Parts & Service: 020 8988 7400 / E-mail: [email protected] or [email protected]
2. Stand to the side of the stone and hold the dresser handle firmly. Place the
dresser on the tool support so that its wheels can move freely (i.e, the
exposed part of the wheel should be facing up). Run the stone and apply
the dresser to the surface of the stone.
3. When the abrasive wheel starts to become clogged with debris, use the
dresser tool supplied to clean (dress) it
CHANGING THE SANDING BELT
To renew or change the sanding belt proceed as follows:
1. Unplug from the power supply.
Remove the sander side cover by
unscrewing the securing screw.
2. Slacken the top roller securing
wingnut, allowing the top roller to
move slightly off its axis as shown.
3. Slide the belt off and replace with
a new one, ensuring it lies
centrally on the top and bottom
rollers
4. Retighten the top roller securing
wingnut till it becomes firm but
NOT too tight. The belt should now
be fairly taught and positioned
centrally on the rollers.
IMPORTANT: The belt needs just
enough tension to ensure that it does
not slip on the rollers whilst under
load, however too much tension will
shorten the working life of the belt
and the machine.
5. Replace the sanding belt cover.
6. Rotate the belt by hand whilst screwing the Tracking Adjustment screw in or
out to ensure the belt runs centrally on the rollers. Turn the screw
anticlockwise to move the belt outwards (towards the outer cover), or
clockwise to move inwards.
7. When satisfied, plug the machine into the power supply and switch on.
Make fine adjustments with the Tracking Adjustment screw if necessary.
CLEANING & STORAGE
Clean the exterior of the machine if required using a mild detergent or mild
solvent. NEVER immerse the machine in water. To reduce any fire hazard, keep
Summary of Contents for 6502130
Page 24: ......