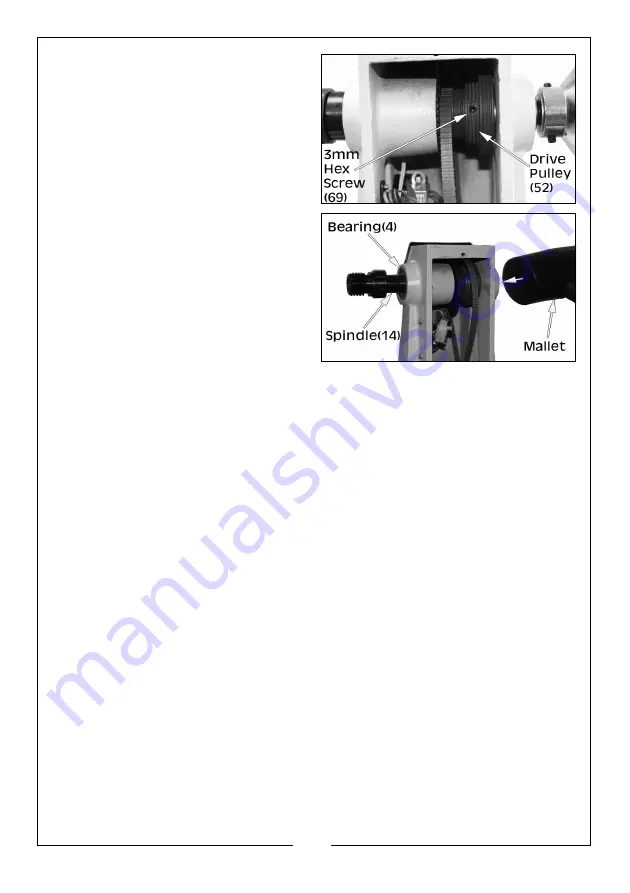
13
Parts & Service: 020 8988 7400 / E-mail: [email protected] or [email protected]
3. Loosen the 3mm hex screw (69)
on the drive pulley (52).
4. Tap out the spindle (14) using a
mallet.
NOTE:
If you don’t have a mallet,
place a block of wood
against the spindle and tap
with a hammer.
5. To get the spindle completely out,
use a flat head screwdriver to tap
it the rest of the way.
NOTE:
Be careful not to damage the bearings or the threads.
6. Replace the bearings, spindle or belt as required.
BELT:
You need only to move the spindle enough to slide a new belt on.
SPINDLE:
You must knock the spindle completely out through both bearings.
BEARINGS:
After removal of the spindle, completely knock out the bearings
from the inside of the headstock. This is best accomplished by inserting a
long rod or screwdriver through one bearing inside the headstock toward
the opposite bearing. tap firmly to remove the bearing from the casting. Do
the same for the second bearing. Please be aware not to damage the
retainer rings (13) when tapping out the bearing. Reassemble the new bear-
ings by tapping them into place from the outside and replace spindle.
NOTE:
You may have to loosen the motor plate screws (44, 45 & 46) to
reinstall the drive pulley (52), spindle collar (3) and belt (53).
7. Reinstall the hand wheel (1) and 3mm hex set screws (2).
NOTE: DO NOT
tighten the hand wheel against the bearings
8. Tighten the pulley 3mm hex screw (69) and close the rear belt door (7)
Please refer to TROUBLESHOOTING on page 17. If you are unable to rectify any
faults, please contact your local dealer or CLARKE International Service
Department on 0208 988 7400 for assistance.
Summary of Contents for 6501661
Page 20: ......