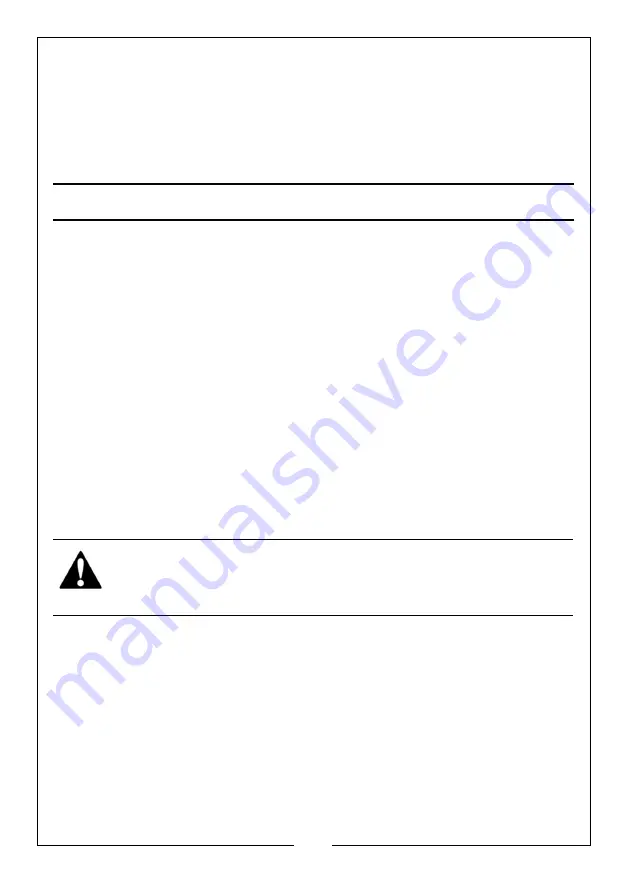
10
Parts & Service: 020 8988 7400 / E-mail: [email protected] or [email protected]
NOTE:
Never attempt to grind a piece of metal that is thinner than the
gap between the tool rest and the grinding wheel.
2. Press the tool blade evenly onto the grinding stone and move the tool
sideways across the stone. Make sure that at least half the width of the tool
cutting edge comes into contact with the grinding stone at any time to
avoid damage to the stone.
MAINTENANCE
GENERAL MAINTENANCE
Make sure that all components are tight and secure. Always have any
damaged or worn parts repaired or replaced by qualified service personnel.
Do not attempt to repair the grinder unless you are qualified to do so.
The drive motor and bearings are sealed units and require no regular
maintenance. Should you require assistance, contact your local Clarke
service agent.
The stone will wear down with use and may well go out of true. Use a dressing
wheel or stone grader to correct the trueness and to remove worn, glazed
grains from the stone.
The stone will have a finite life expectancy, dependant upon the nature of the
work being done. Periodically, make a note of the wheel diameter and
replace your 150mm dia wheel if it reduces to an little as 130mm in diameter.
INSTALLING A NEW GRINDING WHEEL
Use only correct replacement wheels of a suitable grade for your intended
use. Check that the spindle speed (no-load speed) marked on the machine
does not exceed the maximum rpm marked on the grinding wheel. Consult
your dealer if in doubt about choosing the correct replacement wheel.
Check replacement wheels thoroughly for any signs of damage before fitting.
Replacement wheels must fit easily, but not loosely, on to the machine spindle.
Do not attempt to fit a wheel that is tight on the spindle. There is a danger of a
tight fitting wheel bursting in use if the spindle expands due to becoming hot.
WARNING: NEVER RE-START THE GRINDER WITHOUT THE GUARDS
INSTALLED.
Summary of Contents for 6500112
Page 16: ......