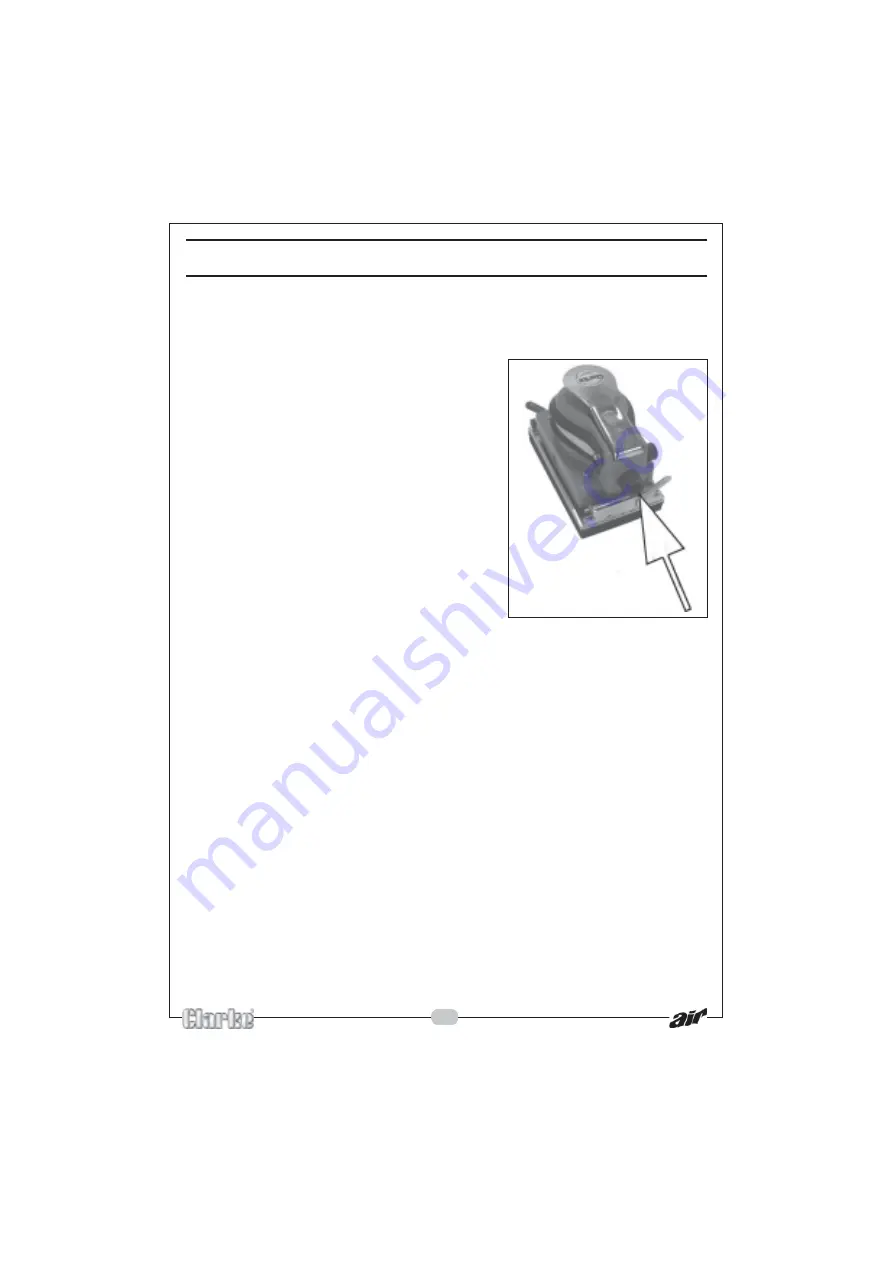
10
Parts & Service: 020 8988 7400/E-mail:[email protected] or [email protected]
MAINTENANCE
WARNING!
Make sure that the sander is disconnected from the air supply
before starting any cleaning or maintenance procedures.
DAILY
•
Drain water from the compressor air tank
and air-line.
•
Pour a few drops of CLARKE air line oil**,
into the air inlet. This should be carried out
regardless of whether or not an air line
lubricator is used. If an air-line lubricator is
not used, this procedure should be
repeated after every two to three hours of
use.
WEEKLY
•
Check the air inlet screen filter in Fig 3 and
clean if necessary.
CLEANING
•
Keep the body of the sander clean and free from debris. Grit or gum
deposits in the tool may reduce efficiency.
•
After extensive use, remove the screen filter and flush out the sander with
gum solvent oil or an equal mixture of SAE No10 oil and paraffin. Allow to
dry before use.
SERVICING AND REPAIRS
•
Major servicing and repair should be carried out by a qualified service
technician.
PERFORMANCE
Please note that factors other than the tool may effect its operation and
efficiency such as reduced compressor output, excessive drain on the airline,
moisture or restrictions in the line, or the use of connectors of improper size or
poor condition which will reduce air supply.
**Clarke Air Line Oil is available from your CLARKE dealer part no. 3050825.
ACCESSORIES
A wide range of airline accessories are available including filter/regulators,
lubricators, high pressure hoses, adaptors and connectors etc. Contact your
CLARKE dealer for further information, or call CLARKE International on 01992
565333.
Air Inlet Screen
Filter (located
here)
Fig 4