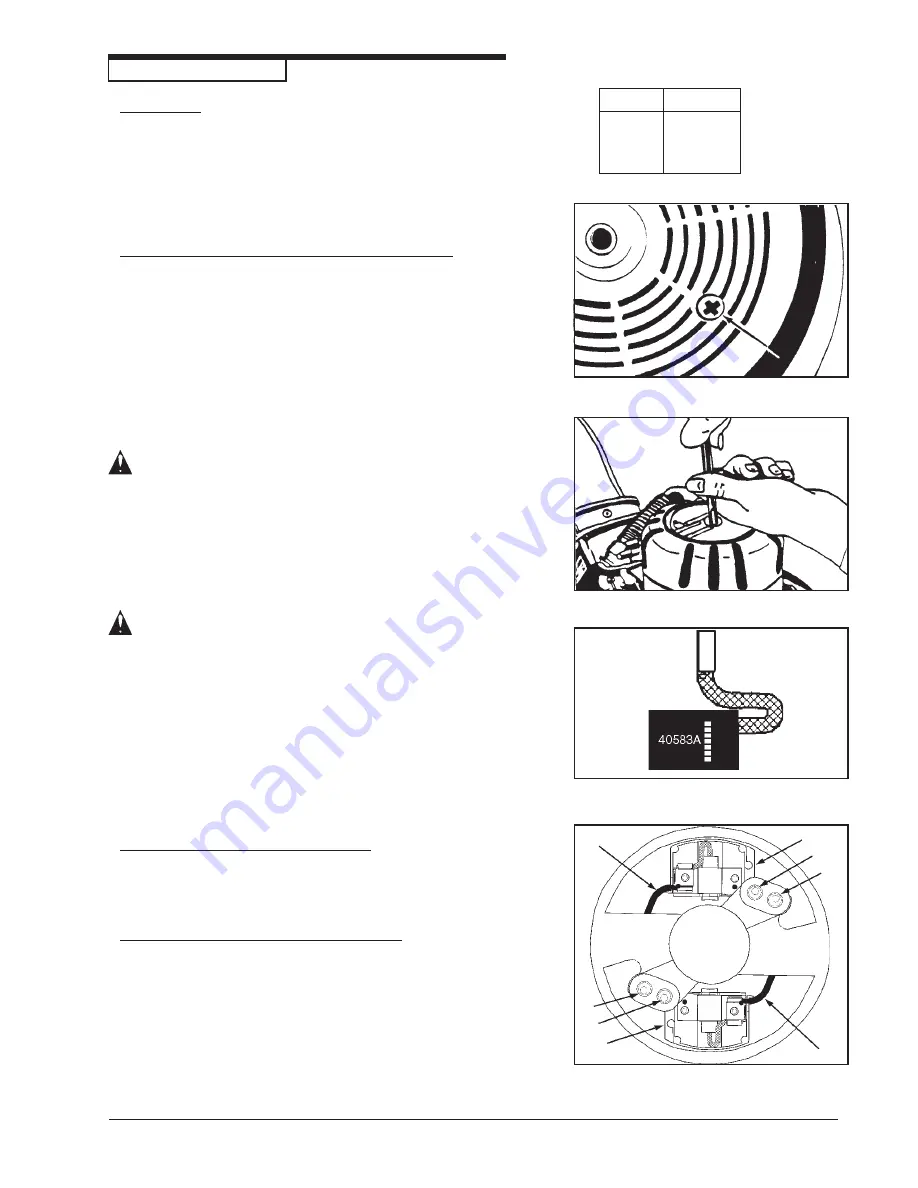
Clarke
®
American Sanders
B-2 (CE) Operator's Manual
FORM NO. 70162B - 11 -
Figure 9
Figure 10
Figure 11
MAINTENANCE
Lubrication
The machine is completely lubricated. The bearings and
gears in the gear unit have enough lubricant for approximately
six months of normal operation. All other bearings are sealed
and have enough lubricant for the life of the machine. No
lubricant is needed for the rotating disc guard.
How To Change The Lubricant In The Gearbox
To change the lubricant in the gearbox, follow this procedure:
1. Put the machine upside down on a bench.
2. Align one of the two holes in the rubber pad with one of
the three holes in the rotating disc guard.
3. Align both holes with one of the three screws in the
gear housing cover. Remove the screw from the gear
housing cover. See figure 9.
4. Align the holes with each of the other two screws, then
remove screws.
CAUTION
:
Make sure no dust enters the gear
box. Damage could occur to the gear
box.
5. Remove the cover from the gear housing.
6. Remove the old lubricant from the gearbox.
7. Add ten ounces of Clarke American Sanders lubricant
to the gearbox.
CAUTION
:
To prevent damage to the motor,
do not add more than ten ounces
of lubricant to the gearbox.
8. Using the three screws removed above, install the cover
on the gear housing.
9. Start the machine and let it run for 15 minutes. A small
amount of excess lubricant should flow out the vent
hole. If none appears it may be necessary to add
additional lubricant.
10. Wipe off excess lubricant and clear vent hole.
How To Check The Carbon Brushes
Depending on use, a set of brushes can be expected to last
250 hours and should be inspected sometime prior to that
time.
To check the brushes, follow this procedure:
1. Remove the motor cover. See figure 10.
2. Inspect the carbon brushes. Replace both brushes if
either brush has worn to 3/8" in length, or is worn to the
wear indicator. See figure 11.
3. To replace the brushes, disconnect the field wire (A)
from the brush holder (B). Then remove the two screws
and washers (C) securing the holder to the motor
housing. See figure 12.
Lubricants
Qty
Part No.
1 Qt.
16610A
1 Gal.
16611A
Figure 12
A
A
B
B
C
C
C
C
Summary of Contents for 07097A
Page 20: ......