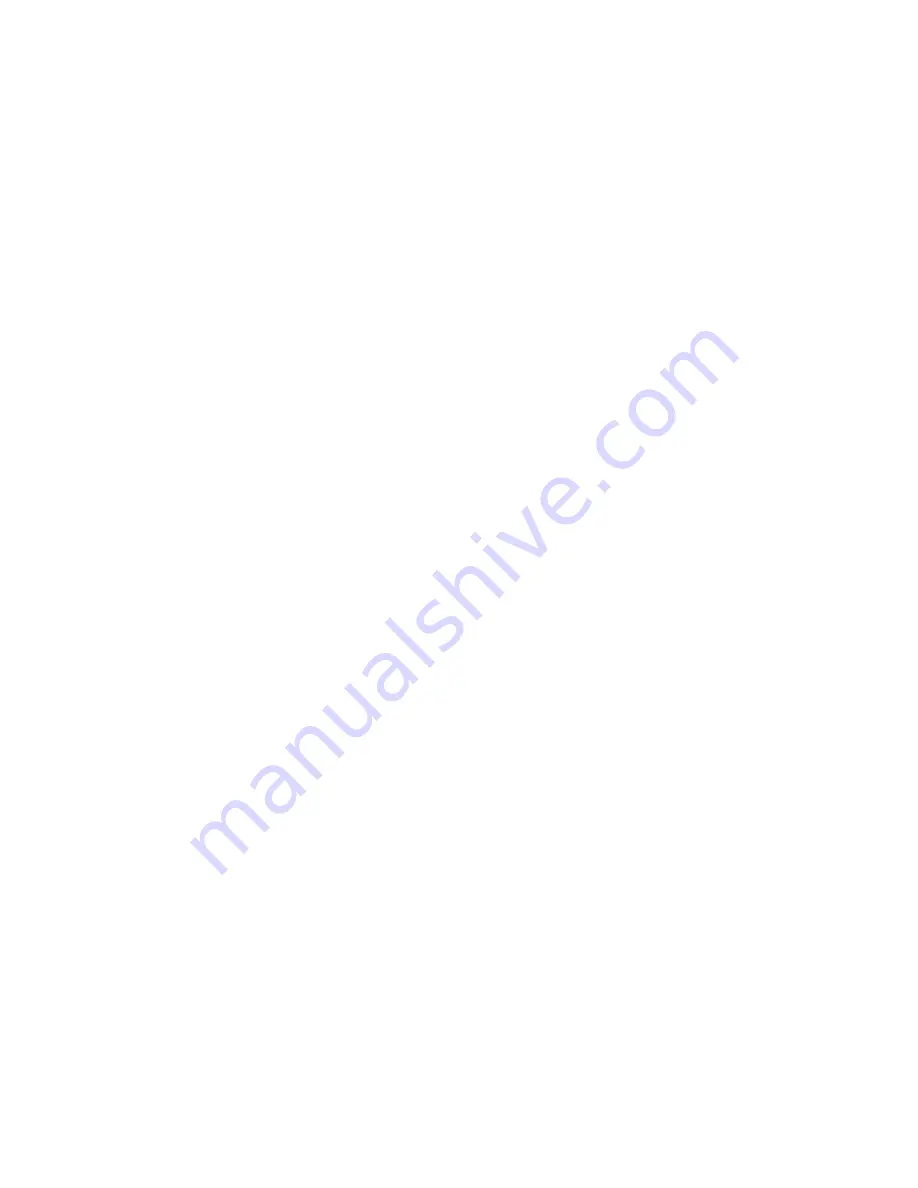
SERVICE
Clark Foam will repair planers we have sold at the California Factory. Clark Foam stocks and
sells the commonly used parts like brushes, triggers, blades, blade holders, depth adjustment
components, bearings, foam filters, and knobs. We can usually rob parts we do not stock
from new planers being assembled. We can also order any part on the planer. It will probably
be easier to purchase parts from Clark Foam rather than from a local repair center because so
many parts are modified.
HELP LINE
Weekdays between 6:00 AM and 2:30 PM Pacific Standard Time there will be an expert avail-
able to answer planer and vacuum system technical questions at (949) 582-2000. FAX ques-
tions to (949) 582-5085 or e-mail to [email protected]. Also most representatives of Clark
Foam have some planer experience.
FIRE DANGER
The first rule is “no fuel - no fire”. Keep a clean shop. Also if you burn down it hurts every-
one building surfboards. Fire Marshals read statistics and newspapers. You will not be very
popular!
Wiring is the number one cause of surfboard factory fires. Maintain good wiring and use
common sense. Poor housekeeping is the second most common cause of fires.
CUSTOM PLANERS
While developing the 2003 Model we identified three important things: First the really good
shapers have developed an incredible level of skill with their planers. Second we noticed that
once an experienced shaper has a planer set up a certain way they do not like change. Last we
noticed there are significant differences of opinion in several areas of planer design.
During our developmental work we tried a number of configurations including knobs, cut
depth indicators, base plates, handles, base plates, and modifications to the main plastic frame.
This information is available to customers.
Often we can build a special planer to the customer’s specification.
Summary of Contents for 2003 Model Foam Planer
Page 1: ...CLARK FOAM PLANER 2003 MODEL SAFETY AND OPERATING INSTRUCTIONS Version 1 2003 ...
Page 4: ......
Page 13: ......