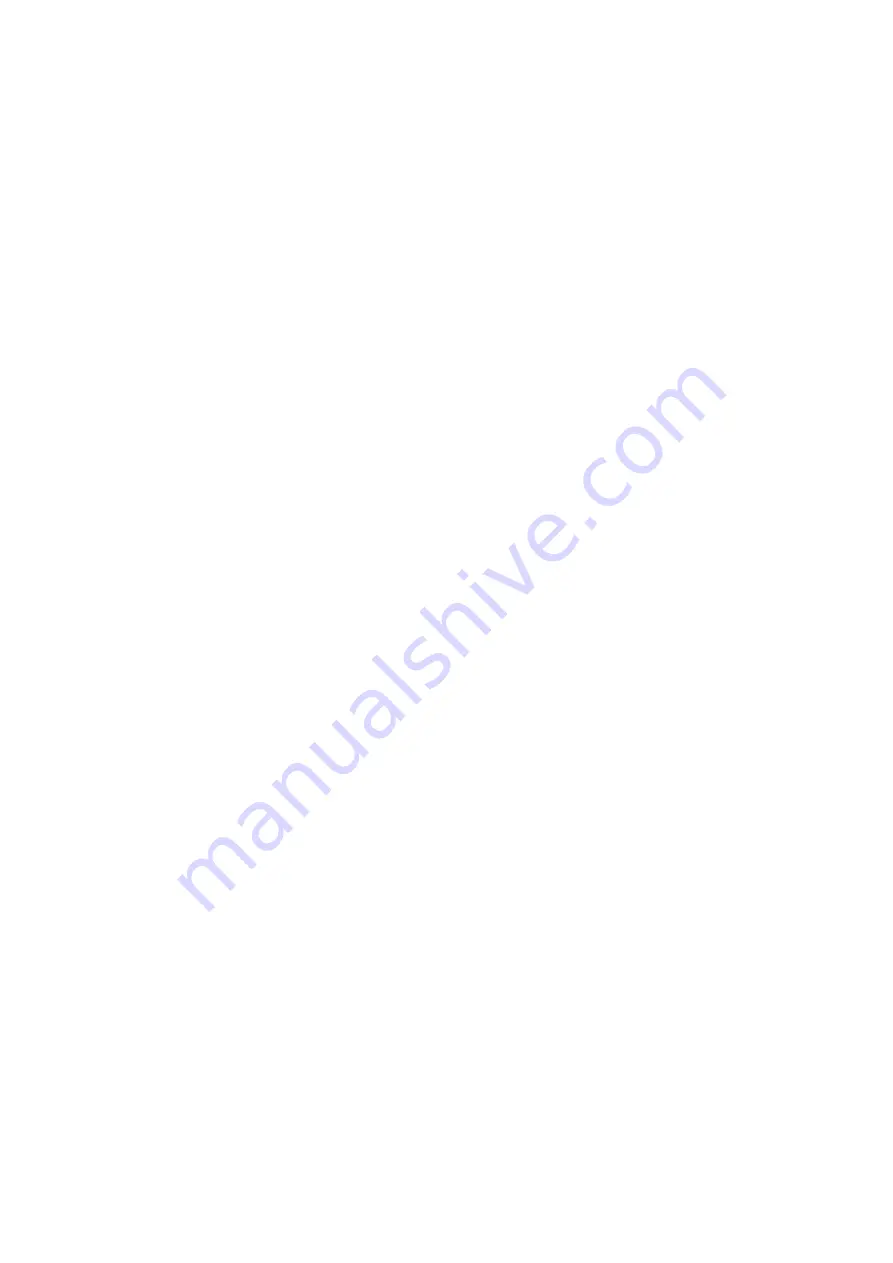
F i l o x S e r i e s F i l t e r
FILOX WS ISS 1 \page 19
9.0 FAULT FINDING AND RECTIFICATION
9.1 NO FLOW TO SERVICE
Check mains pressure is above 1.7 bar.
Check inlet water supply
Check inlet and outlet isolating valves are open.
Check service outlet valve is open.
Check pressure drop across media. If excessive, media may be
fouled, or internals blocked. Initiate a backwash. If this does not free
up the media the filter will need to be inspected and serviced by a
competent engineer.
Backwash with chlorine solution to remove organic build up
9.2 POOR TREATED WATER QUALITY
Check manual by-pass closed.
Check raw water pressure above minimum. If flow is less than design rate,
channelling of water can occur in media, which results in inadequate
treatment.
Backwash with chlorine solution to remove organic build up
Increase frequency of backwash as media may be becoming
overloaded.
Increase backwash flow.
Check piston and seals & spacers. Check raw water analysis for changes