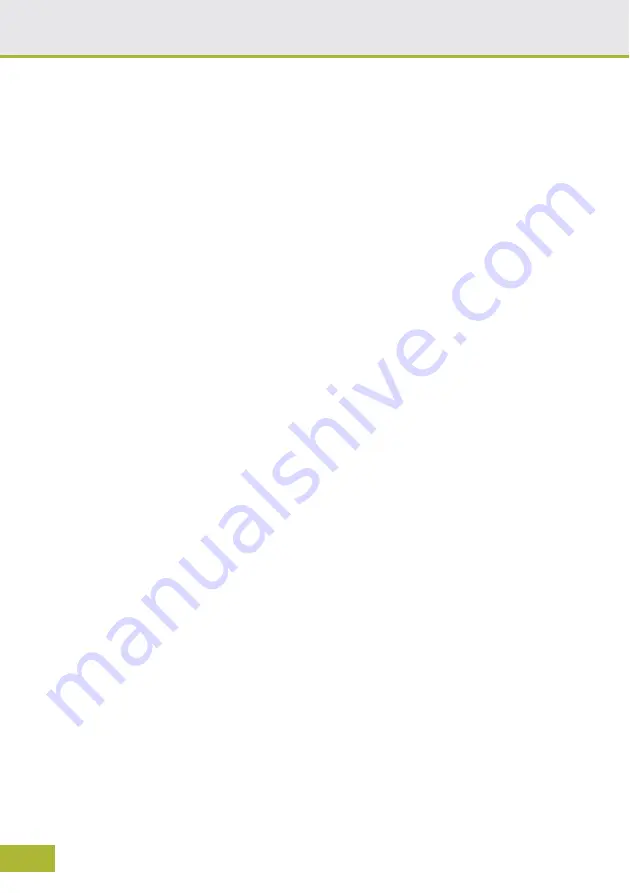
Wet Harvest Recommendations
42
When unloading wet grain
Reduce the flow into the unloading auger by shutting down the slides on both
the cross augers in the grain tank. This will reduce the load on the unloading
system, bringing it down to a ‘normal’ level.
If wet and dirty grain is being unloaded
It is also likely that dirt will build up in the turret auger. This can and should be
checked regularly through the inspection doors, and cleaned if required.
If the shear bolt on the unloading drive fails
This is often the first sign that either the slides in the tank are too high, or
there is too much dirt in the system, check auger timing.
Chopping wet straw
This adds an extra load to the chopper drive. Regularly check the tension of
the drive belts and the blade condition. Do not forget the 2 ‘stops’ at either end
of the main tensioner.
Chopper blade wear
This can be accelerated when chopping wet straw due to the increased levels
of soil in it. Check the condition of the blades regularly. Do not forget to check
the stationary blades.
In wet conditions
It is possible for material to stick to the return floor under the walkers. This
then impedes the flow of grain back to the preparation pan and affects the
sample. Check the pan regularly and clean as required.
Summary of Contents for TUCANO 400-300
Page 1: ...Information and Basic Field Settings for TUCANO 400 300...
Page 2: ......
Page 13: ...Notes 13...
Page 35: ...Notes 35...