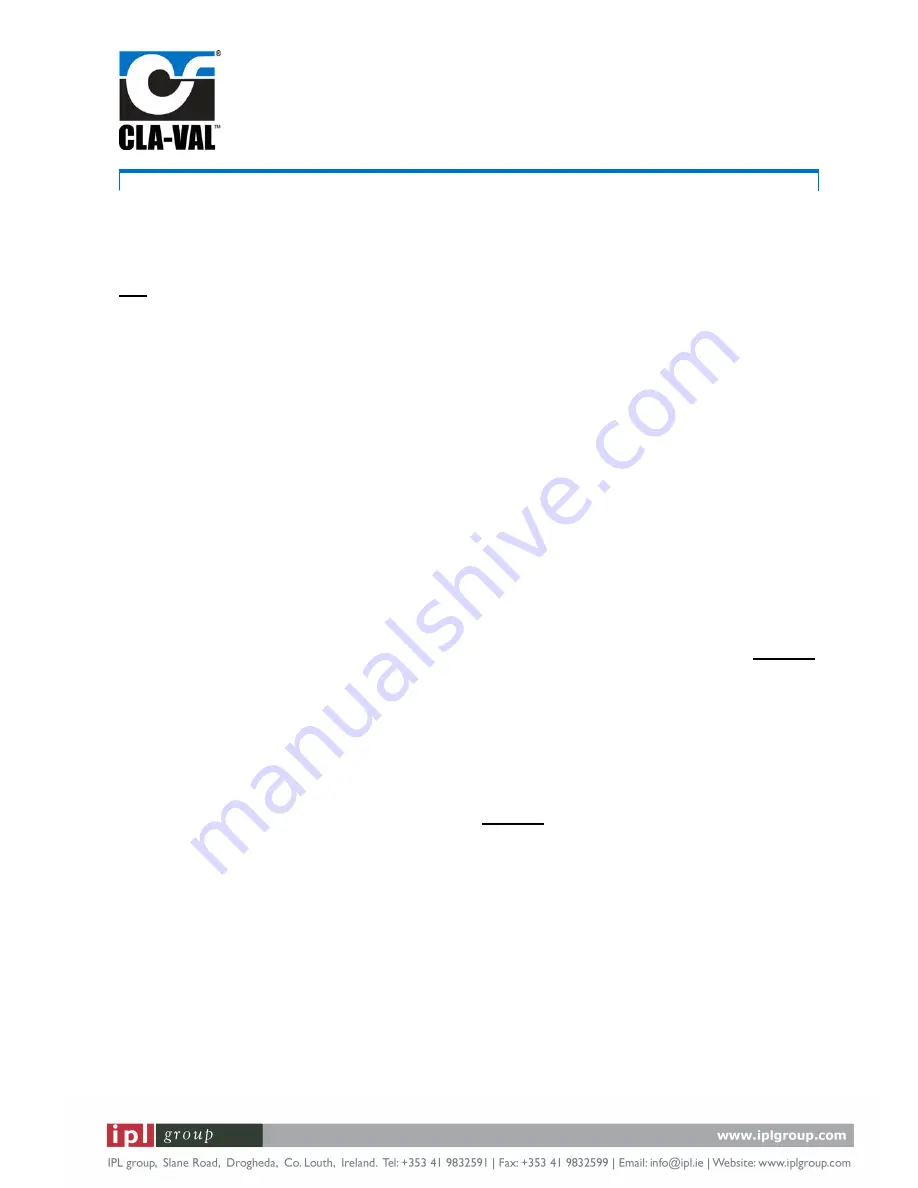
CLA-VAL
100-01
Installation - Operation - Maintenance
NGE - GE - AE
`
CLA-VAL
Europe
www.cla-val.ch
6
-
HYT001SE
C 11/08
INSPECTION OF PARTS
After the valve has been disassembled, each part should be examined carefully for signs of wear, corrosion, or any other
abnormal condition. Usually, it is a good idea to replace the rubber parts (diaphragm and disc) unless they are free of signs
of wear. These are available in a repair kit. Any other parts which appear doubtful should be replaced. WHEN ORDERlNG
PARTS, BE SURE TO GIVE COMPLETE NAMEPLATE DATA, ITEM NUMBER AND DESCRlPTlON.
Note:
If a new disc isn’t available, the existing disc can be turned over, exposing the unused surface for contact with the
seat. The disc should be replaced as soon as practical.
REASSEMBLY
1. Reassembly is the reverse of the disassembly procedure. If a new disc has been installed, it may require a different
number of spacer washers to obtain the right amount of “grip” on the disc. When the diaphragm assembly has been
tightened to a point where the diaphragm cannot be twisted, the disc should be compressed very slightly by the disc
guide. Excessive compression should be avoided. Use just enough spacer washers to hold the disc firmly without
noticeable compression.
2.
MAKE SURE THE STEM NUT IS VERY TIGHT.
Attach a good fitting wrench to the nut and give it a sharp “rap” rather
than a steady pull. Usually several blows are sufficient to tighten the stem nut for final tightening. Failure to do so could
allow the diaphragm to pull loose and tear when subjected to pressure.
3. Carefully install the diaphragm assembly by lowering the stem through the seat bearing. Take care not to damage the
stem or bearing. Line up the diaphragm holes with the stud or bolt holes on the body. On larger valves with studs, it may
be necessary to hold the diaphragm assembly up part way while putting the diaphragm over the studs.
4. Put spring in place and replace cover. Make sure diaphragm is Iying smooth under the cover.
5. Tighten cover nuts firmly using a cross-over pattern until all nuts are tight.
6. Test HYTROL Valve before re-installing pilot valve system.
TEST PROCEDURE AFTER VALVE ASSEMBLY
There are a few simple tests which can be made in the field to make sure the HYTROL Valve has been assembled properly.
Do these before installing pilot system and returning valve to service. These are similar to the three troubleshooting tests.
1-
Check the diaphragm assembly for freedom of movement after all pressure is removed from the valve.
SEE CAUTlON!.
Insert fabricated tool into threaded hole in top of valve stem, and lift the diaphragm assembly manually. Note any
roughness, sticking or grabbing. The diaphragm assembly should move smoothly throughout entire valve stroke. The tool
is fabricated from rod that is threaded on one end to fit valve stem (See chart in Step 4 of “Disassembly” section.) and
has a “T” Bar handle of some kind on the other end for easy gripping.
Place marks on this diaphragm assembly lifting tool when the valve is closed and when manually positioned open. The
distance between the two marks should be approximately the stem travel shown in stem travel chart. (See “Freedom of
Movement Check” section.) If the stroke is different than that shown, there is a good reason to believe something is
mechanically restricting the stroke of the valve. The cover must be removed, the obstruction located and removed. (See
“Maintenance” Section for procedure.) Due to the weight of the diaphragm assembly this procedure is not possible on
valves 8” and larger. on these valves, the same determination can be made by carefully introducing a low pressure-less
than five psi) into the valve body with the cover vented.
SEE CAUTION!
. Looking in cover center hole see the diaphragm
assembly lift easily without hesitation, and then settle back easily when the pressure is removed.
2-
To check the valve for drip-tight closure, a line should be connected from the inlet to the cover, and pressure applied at
the inlet of the valve. If properly assembled, the valve should hold tight with as low as ten PSI at the inlet. See “Tight
Sealing Check” section.)
3-
With the line connected from the inlet to the cover, apply full working pressure to the inlet. Check all around the cover for
any leaks. Re-tighten cover nuts if necessary to stop leaks past the diaphragm.
4-
Remove pressure, then re-install the pilot system and tubing exactly as it was prior to removal.
Bleed air from all high
points.
5-
Follow steps under “Start-Up and Adjustment” Section in Technical Manual for returning complete valve back to service.
Summary of Contents for CPC 138-01
Page 3: ......