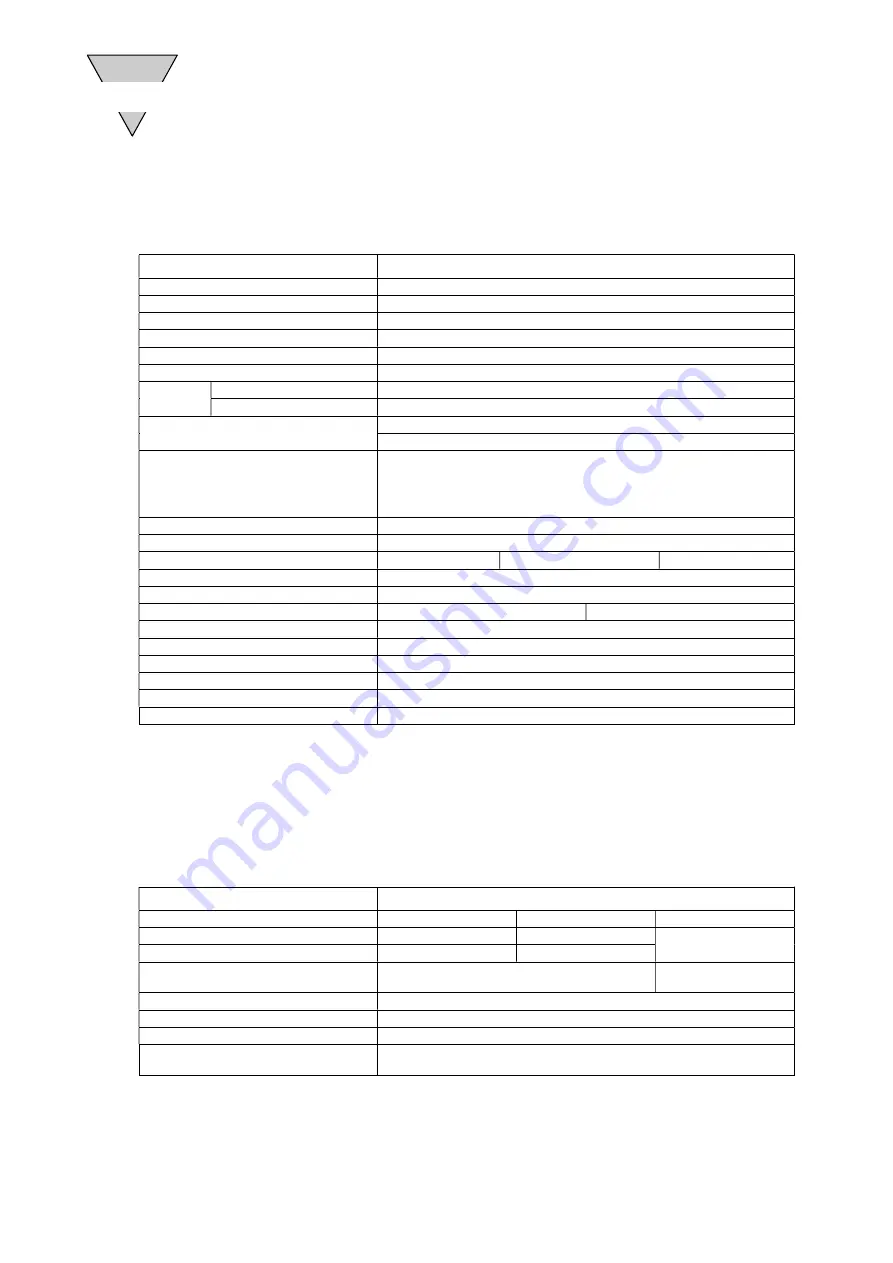
[SM-213928-A/2]
―
35
―
SPECIFICATION
HOW TO ORDER
8
8. PRODUCT SPECIFICATIONS AND HOW TO ORDER
8.1 Product Specifications
1) Specifications of the Block Manifold
Item
Specifications
Manifold
Block manifold (DIN rail mount)
Applicable solenoid valve
(N) 4KB2 Series (not including the external pilot series)
No. of stations
2 to 25
Valve type and operation
Pilot operated soft spool valve
Working fluid
Compressed Air
Piping method(Note1)
Common air supply (P), common exhaust (R)
Port size
Air supply exhaust P
・
R
Top (
φ
8,
φ
10
、φ
12 push-in joint)
Cylinder port A
・
B
Side (
φ
6,
φ
8,
φ
10 push-in joint)
Tube to be used
Soft nylon (F-15 Series)
Urethane (U-95 Series), New urethane (UN Series)
Flow characteristics C(Sonic conduct-
ance) dm
3
/(s
・
bar)
4KB210,4KB220:2.6
4KB230:2.4
4KB240:3.1
4KB250:2.3
Ambient temperature
℃
5 to 50
Fluid temperature
℃
5 to 50
Min. working pressure
MPa
0.15(2-pos.single)
0.10(2-pos.double)
0.20(3-pos.)
Max. working pressure
MPa
0.70
Proof pressure
MPa
1.05
Response time
ms
30 or less(2-pos)
60 or less(3-pos)
Lubrication
Not required (Use Grade turbine oil type 1. ISO VG 32 when required)
Protection structure
Dust-proof
Vibration resistance
m/s
2
50 or less
Shock resistance
m/s
2
300 or less
Atmosphere
No corrosive gas should exist
Manual operating device
Non-locking type (Option : locking)
Above-mentioned response time is the figure on the non-lubricated at 0.5 MPa ,
and depends on the pressure and quality of lubricant.
Pressure is converted as 1MPa=10.1972kgf/cm
2
≒
10.2kgf/cm
2
In case of use, consult separately of the continuous energizing.
Note1
:
Common pilot exhaust(except pilot exhaust of 3-position)
2) Electrical Specifications
Item
Specifications
Rated voltage
V
AC100V (50 / 60Hz)
AC200V (50 / 60Hz)
DC24V
Starting current
A
0.056 / 0.044
0.028 / 0.022
0.075
Holding current
A
0.028 / 0.022
0.014 / 0.011
Power consumption (with indicator
light)
W
1.8 / 1.4 (1.8 / 1.5)
1.8 (2.0)
Voltage fluctuation range
±
10%
Thermal class
B(mold coil)
Temperature rise
℃
43
Electric connection
Grommet with lead wire
(option : small terminal box, C-connector, D-connector)