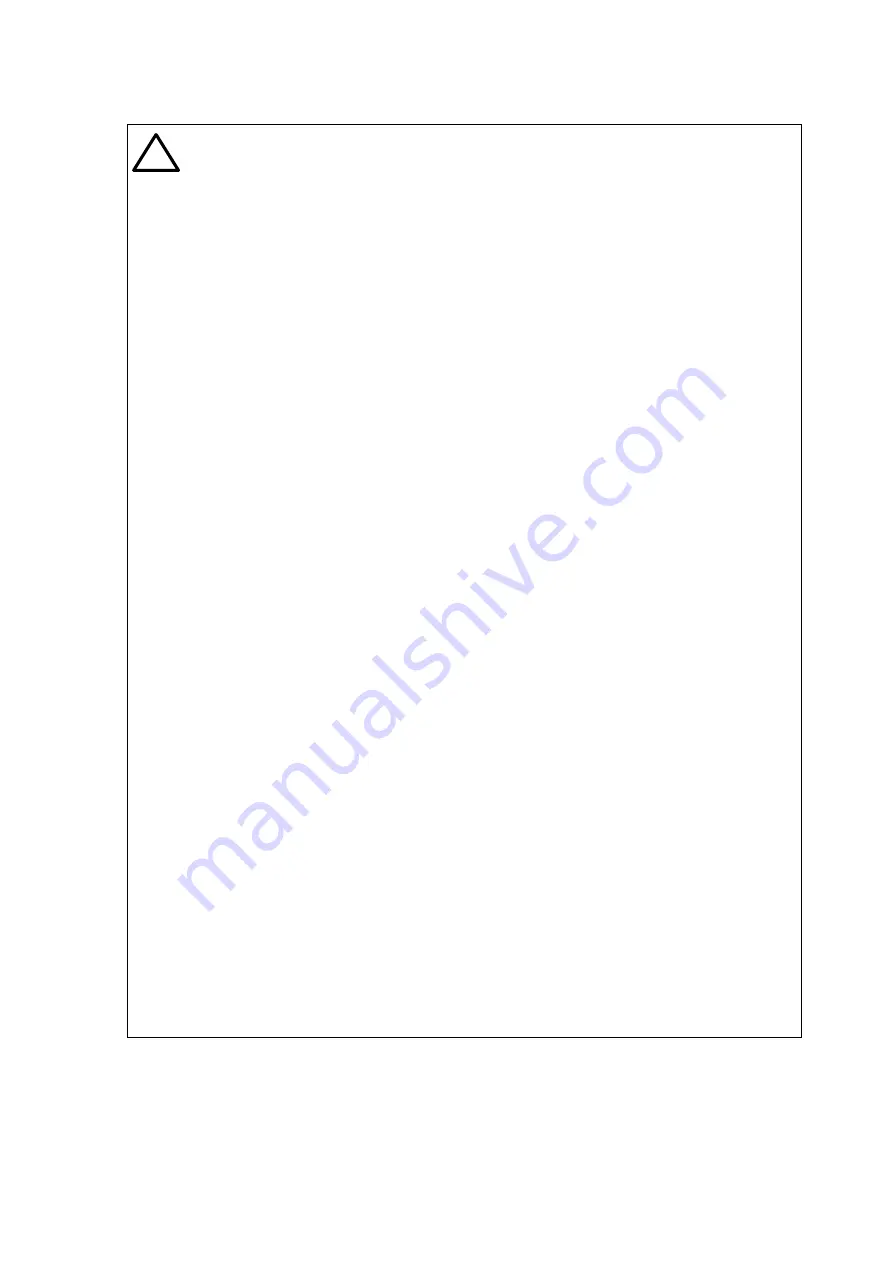
[SM-206790-A/5]
―
5
―
PIPING (Section 4.3)
a) Observe the recommended tightening torque when
connecting pipes.
Observing the recommended tightening torque prevents
air leakage and damage to the screw threads. To prevent
damage to the screw threads, first use your hand to lightly
tighten the screw and then use a tool to tighten the screw
to the recommended torque.
b) Make sure that the pipes will not be disconnected at
the joints by mechanical movements, vibrations or
tension.
If the exhaust piping of the pneumatic circuit is discon-
nected, the actuator speed control is disabled.
If the above happens to a chuck holding mechanism, the
chuck will open. The inadvertent opening of the chuck
may cause a serious accident.
c) When supplying the compressed air for the first time
after completing the piping, be sure to check every
joint in the piping for air leakage.
d) When supplying the compressed air for the first time
after completing the piping, increase the air pressure
gradually but never introduce a highly-pressurized air
suddenly.
A sudden introduction of a highly-pressurized air may
disconnect pipes at joints and/or cause the tubes to jump
around, any of which may cause an injury.
e) Do not decrease the inside diameter of the piping from
any of the solenoid valve exhaust ports to a diameter
less than the exhaust pipe connecting port size.
Normal operation of the actuator depends on the
smoothness of the exhaust flow. With a manifold system,
a restriction to the exhaust flow may prevent normal op-
eration of other solenoid valves.
f) Removal of foreign matter
Rust and other foreign matter in the pneumatic circuit
may cause a malfunction or leakage from the valve seat.
Insert a filter (maximum allowable particle size 5μm or
less) immediately upstream of the solenoid valve.
g) Air supply
Do not restrict the flow of air through the air supply pip-
ing. With a manifold system with multiple stations, a drop
in the air supply pressure may cause trouble through a
delay in the operation timing.
!
CAUTION :