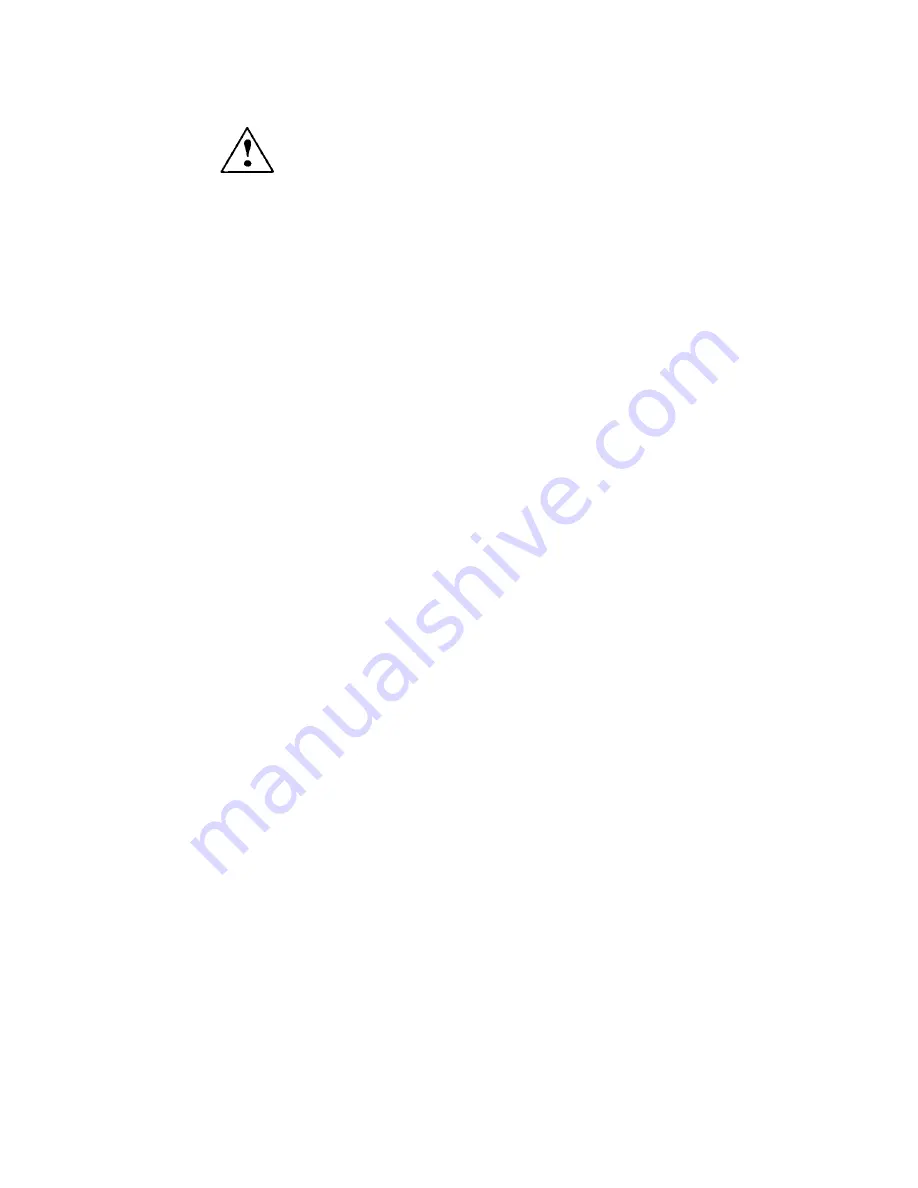
3-7
3.4 Loading the Paper
CAUTION
Be careful of the edges of the plates so injury or
property damage is possible.
The printer is designed to easily load the paper and ribbon. After
opening the cover, set the register paper as follows:
1) Push down the open lever (1) to have the head open (see the
figure).
2) Push the lever (3) to have the guide rail upper (2) open.
3) Insert the roll holder (4) in the roll paper and roll guide (5) and set
on the paper holder (6). Adjust the roll guide (5) to match the
width of the paper. The roll paper must be positioned into the
reference plane.
4) Slide the moving paper guide (7) to the right end to secure the
paper insertion course.
5) Set the paper as shown in the figure.
6) Align the left edge of the paper with the stationary paper guide (8)
and put the moving paper guide to the edge of the paper so that
the paper does not shift sideways.
7) Push down the guide rail upper until the lever is hooked and lock it.
8) Align the paper with the peeling plate (9) positioning notch and
push down the ribbon bearing flat (10) to close the print head.
The open lever is hooked.
9) Close the cover.
10) Turn on the power to the printer. The LCD screen on the control
panel will show the "On line." Press the Feed key. The paper will
advance to the next label and stop there.
Summary of Contents for CLP-2001
Page 1: ...CLP 2001 User s Manual...
Page 2: ......
Page 14: ...xii...
Page 24: ...1 10...
Page 34: ...3 4...
Page 38: ...3 8 Roll paper 5 Reference plane Positioning notch 4 6 3 2 10 1 8 7 9...
Page 54: ...4 12...