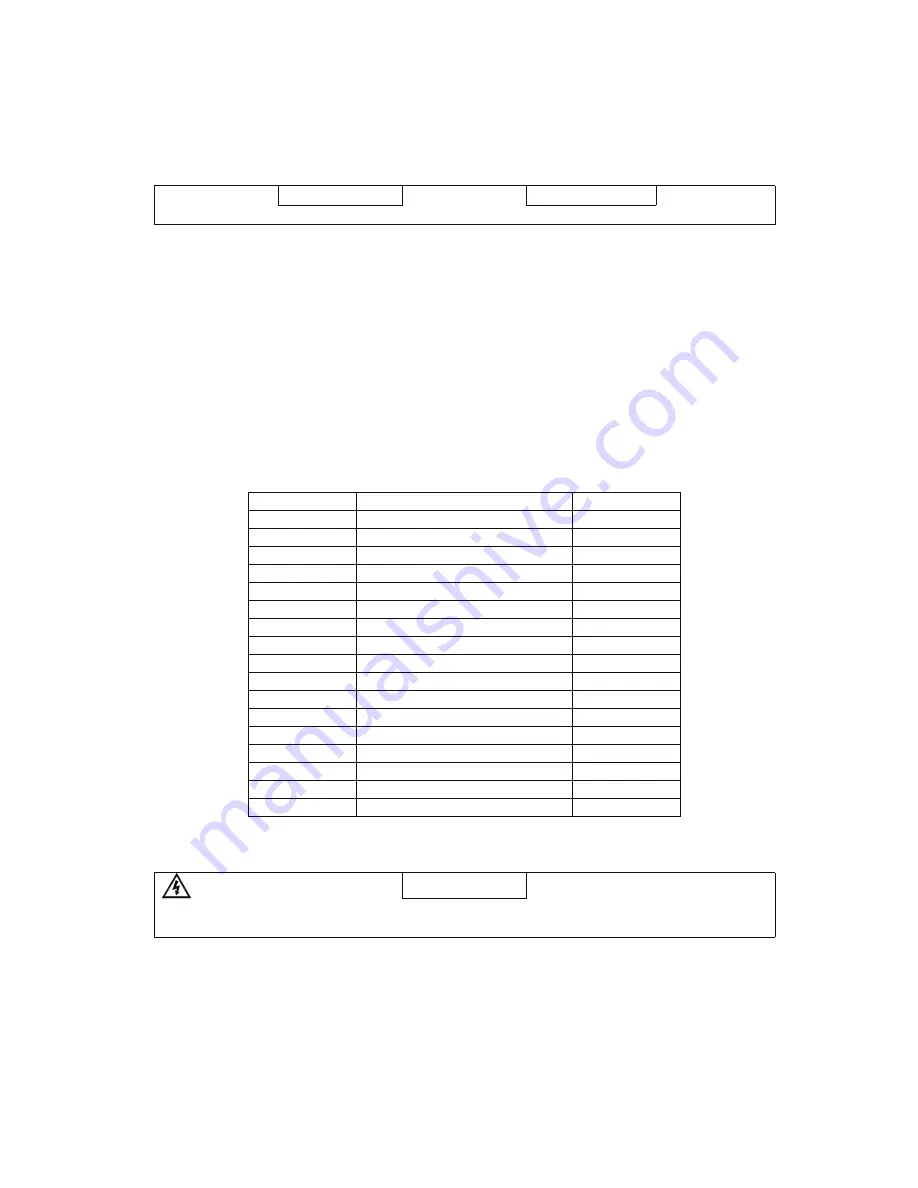
OPERATION
Structural Limits
Operating conditions, such as speed, fluid viscosity, inlet pressure, discharge pressure, temperature,
filtration, duty cycle, mounting etc. are interrelated. Due to these variable conditions, specific application
limitation may be different from structural limitations. This equipment must not be operated without
verification that operating requirements are within its capabilities.
CAUTION
ATTENTION
Under no circumstances are the following structural limitations to be exceeded:
Maximum Inlet Pressure ................................................................................................... 50 PSIG
Maximum Discharge Pressure:
Series 110 ...................... 400 PSI (1500 SSU max., 40 SSU min. viscosity at pumping temp.)
Series 210 ...................... 400 PSI (1500 SSU max., 40 SSU min. viscosity at pumping temp.)
Maximum Fluid Temperature ................................................................................................ 240°F
INSPECTION AND PARTS LIST
Intervals for inspection and replacement of wear parts will vary greatly with the properties of pumped fluid
and can only be determined by experience. All internal parts of unit are lubricated and cooled by pumped
fluid. Fluid that contains abrasive materials or is corrosive will significantly reduce service life and require
shorter service intervals. Wear in pump will normally show as vibration, noise, and loss of capacity or
reduction in flow or pressure.
Table 1 – Pump Parts List
IDP DESCRIPTION
QTY
118 Orifice
1
201 Housing
1
202 Inlet
1
203 Hex
Bolt
4
204 Outlet
1
205 Hex
Bolt
4
207 Lock
Washer
4
208
Balance Piston Bushing
1
213 Key
1
216 Bearing
1
217 Truarc
Ring
2
222 Retainer
1
223 Cap
Screw
4
311 Power
Rotor
1
314
Idler Rotor Assembly
2
409 O
Ring
2
432 O-Ring
1
MAINTENANCE
WARNING
BEFORE working on equipment, make sure all power to the equipment is
disconnected.
GENERAL
: To perform maintenance on canned motor pump, the following initial conditions shall be
completed prior to maintenance action. Close inlet and outlet valves and tag “Out of
Service”. De-energize pump drive motor and vent all pressure from pump. Remove drain
plug (105) and drain fluid from pump and motor.
NOTE:
Part numbers contained within parenthesis such as (103) refer to the balloon numbers as shown
on Figure 3 and the IDP numbers in Table 1.
3
Summary of Contents for IMO 110
Page 7: ...Figure 4 5...