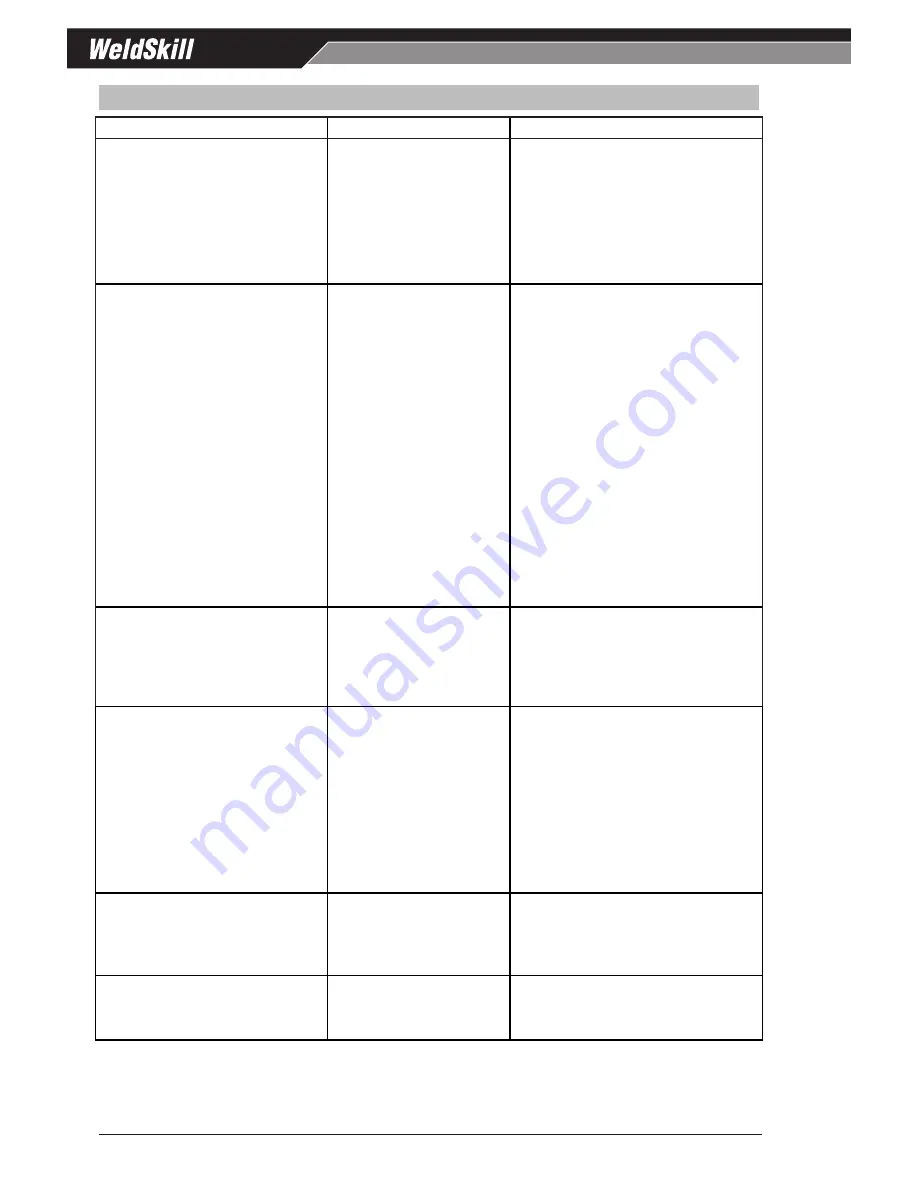
OPERATING MANUAL
200HF
SERVICE 7-2 Manual 0-5406
7.04 Power Source Problems
Description
Possible Cause
Remedy
1
Mains Supply Voltage is On,
the On/Off switch on the rear
panel is in the On position
and the Power indicator on
the front panel is illuminated
however the power source
will not STICK weld.
A
Power Source is not
in the correct mode
of operation.
A
Set the power source to STICK
mode.
B
Work Lead is not
connected to the
work piece.
B
Ensure that the Work Lead is
connected to the work piece and
has a good connection to the
work piece.
2
Mains Supply Voltage is On,
the On/Off switch on the rear
panel is in the On position
and the Power indicator on
the front panel is illuminated
however the power source
will not commence welding in
TIG modes.
A
Power Source is not
in the correct mode
of operation.
A
Set the power source to either
HF TIG or Lift TIG mode with the
process selection control. Refer
to section 4.02.4.
B
Work Lead is not
connected to the
work piece.
B
Ensure that the Work Lead is
connected to the work piece and
has a good connection to the
work piece.
C
TIG Torch 8 Pin
Control Plug not
connected correctly
or loose/faulty
connection in plug.
C
Connect 8 Pin TIG Torch control
plug securely and correctly to
the 8 Pin control socket of the
front of the WeldSkill 200HF
Power Source. Repair or replace
if faulty.
D
Faulty TIG Torch
Trigger.
D
Repair or replace TIG Torch
Trigger switch/lead.
3
Over Temp Indicator is
illuminated and unit will not
commence welding.
Duty cycle of power
source has been
exceeded.
Leave the power source switched
ON and allow it to cool. Note
that Over Temp indicator
must be extinguished prior to
commencement of welding.
4
The welding arc cannot be
established
A
The Mains supply
voltage has not been
switched ON
A
Switch ON the Mains supply
voltage
B
The Welding Power
Source switch is
switched OFF
B
Switch ON the Welding Power
Source
C
Loose connections
internally
C
Have an Accredited CIGWELD
Service Provider repair the
connection
5
Maximum output welding
current cannot be achieved
with nominal Mains supply
voltage
Defective control
circuit
Have an Accredited CIGWELD
Service Provider inspect then
repair the welder
6
Welding current reduces
when welding
Poor work lead
connection to the
work piece
Ensure that the work lead has a
positive electrical connection to
the work piece
Summary of Contents for WELDSKILL 200HF
Page 22: ...OPERATING MANUAL 200HF INSTALLATION 3 4 Manual 0 5406 This Page Intentionally Blank ...
Page 28: ...OPERATING MANUAL 200HF OPERATION 4 6 Manual 0 5406 This Page Intentionally Blank ...
Page 38: ...OPERATING MANUAL 200HF SERVICE 5 10 Manual 0 5406 This Page Intentionally Blank ...
Page 56: ...KEY SPARE PARTS 8 2 Manual 0 5406 OPERATING MANUAL 200HF This Page Intentionally Blank ...
Page 59: ...OPERATING MANUAL 200HF This Page Intentionally Blank ...