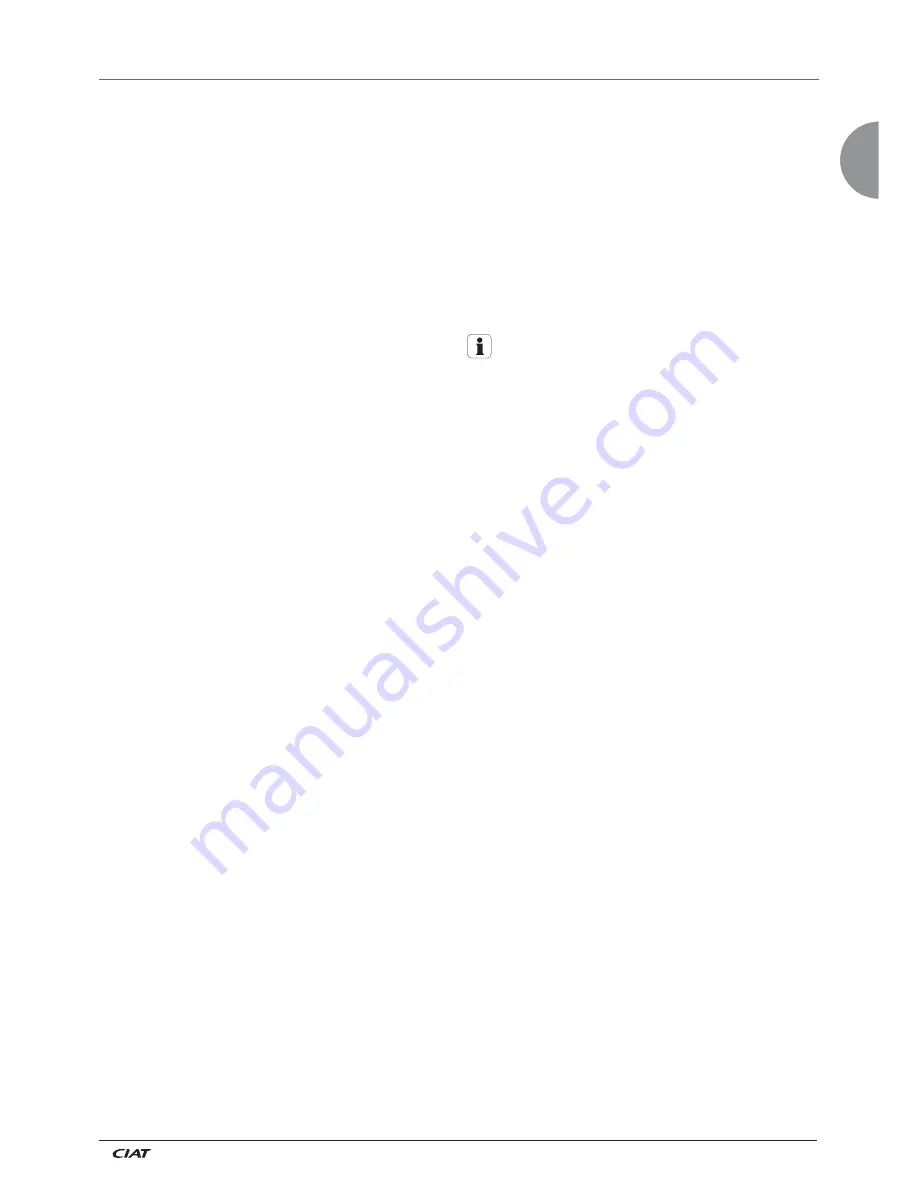
E N
EN - 33
NA13.47 B
13. MAINTENANCE
13.1 Recommendations for maintenance
To ensure the unit operates correctly, we recommend that you
sign a maintenance contract with your installer or an approved
maintenance company.
All work on the unit's electrical or refrigerant systems must
be performed by a qualified authorised technician.
Perform operating inspections in accordance with national
regulations.
Do not work on any electrical components without first
switching off the unit's main disconnect switch in the
electrics box. Although the compressors are switched off,
the power circuit remains live until the unit's disconnect
switch is opened. Other components may remain energised
by external controllers connected to the orange disconnect
terminals on the main terminal strip. Disconnect the
removable portion of these terminals before commencing
any work.
The surfaces of the compressor and pipes may reach
temperatures of over 100°C and cause burns if touched.
Likewise, the surfaces of the compressor may in some
cases drop to freezing temperatures which can cause
frostbite.
Keep the unit clean. Retouch the paintwork if necessary.
To prevent accidents and ensure proper ventilation of the
condenser, keep the unit and the space around it clean and
clear of clutter.
Check the fouling level of the coil. If necessary, remove any
dust, fibres or leaves using a soft brush or vacuum cleaner.
It can be cleaned using a water spray:
-
at low pressure;
-
in the direction of the fins;
-
in the opposite direction to the air.
Never climb on the machine or its copper refrigerant pipes.
Use a platform when working at height.
Any opening or closing of a shut-off valve must be
performed with the unit off.
The liquid valve (located just before the dryer) must be
opened completely when there is refrigerant in the circuit.
The small size of the micro-channel condensers means
that not all of the fluid can be stored in the HP section.
13.2 Preventive maintenance
Keep informed about current environmental standards
and applicable regulations concerning the site, particularly
regarding regular inspections.
The intervals for cleaning are given as a guide and should
be adapted to each unit.
Weekly checks
With the unit running at full capacity, check the following
values:
-
look for traces of water or oil under or around the unit,
and listen for any unusual noises;
-
LP compressor suction pressure;
-
HP compressor discharge pressure;
-
the water inlet and outlet temperatures in the exchangers;
-
the charge via the liquid sight glass and the condition
of the charge using the coloured indicator on the sight
glass;
-
the oil level and its appearance. If the colour changes,
check the quality;
-
check whether the safety devices operate correctly.
Monthly checks
In addition to the weekly checks, you should also check:
-
the operation of the compressor's capacity control
system;
-
for corrosion on all metal parts (base frame, casing,
exchangers, electrics boxes, etc.).
-
the condition of the insulating foam (detachment or
tears);
-
the energy transfer fluids for any impurities which could
cause wear or corrosion in the exchanger;
-
the sealing of the various circuits;
-
whether the safety devices and expansion valves
operate correctly.
Annual checks
In addition to the monthly checks, you should also check:
-
that the intake valve locking lever operates correctly, as
its position can change due to vibrations in the pipes.
Actuate the intake valve (option) at least once a year.
-
the sealing of the retaining valve on the compressor
discharge/separator. Clean or replace this valve if
necessary.
-
the filter dryer for clogging (measure the difference in the
temperature of the copper pipes at the filter dryer inlet
and outlet).
-
the electrical connections to ensure they are tight and in
good condition.
-
the insulation of the motor and the resistance of the
coils. Disconnect all the cables.
-
the condition of the contacts and the current at full load
on all 3 phases.
-
for the presence of moisture in the electrics box.
-
the operation of the water circulation controller.
-
the water quality or condition of the heat transfer fluid.
-
the concentration of the antifreeze solution (MEG or
PEG)
-
Clean the water filter and bleed air from the circuit.
-
Clean the exchangers and check the pressure drop in
the evaporator.
Take an oil sample from the separator every 5000 hours for
analysis. if acid, water or metal particles are found, replace
the oil in the circuit concerned and the filter dryer. The oil
should in principle be changed every three years.
If the whole oil charge is being changed, use only new oil of
the same grade as the original oil, which has been stored
in a hermetically sealed container until charging. The same
oil type must be used.
Check the voltage of the expansion valve coils.
Replace these if necessary (max. lifespan: 4 years).
Summary of Contents for POWERCIAT2 LX
Page 1: ...POWERCIAT2 LX LXC AQUACIAT 2 Instruction manual 04 2014 N 13 47 B...
Page 2: ......
Page 39: ...EN EN 37 NA13 47 B...
Page 40: ...NA13 47 B EN 38...
Page 41: ......