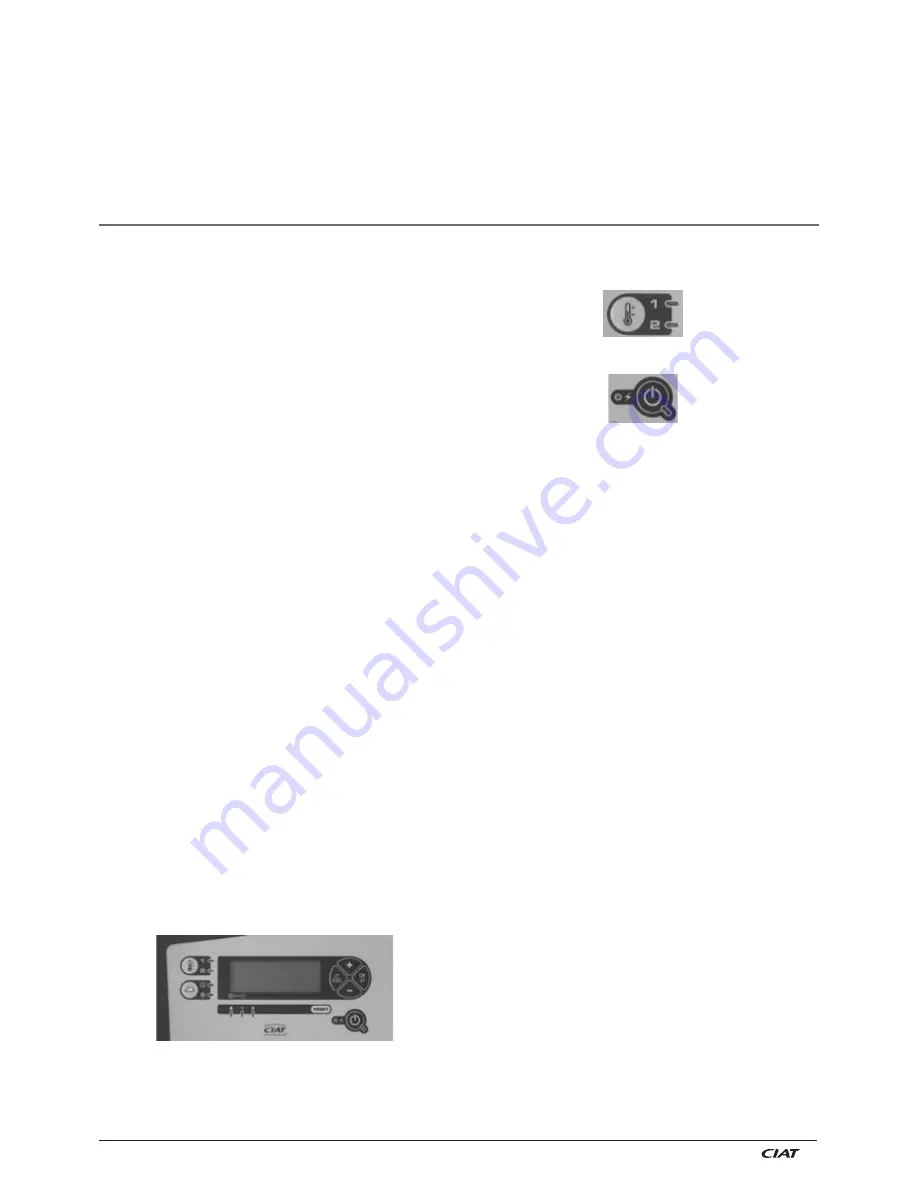
NA13.47 B
EN - 30
11.1 Preliminary checks
Check the following points:
1. Check that the network voltage matches the unit voltage
and that its value remains within the authorised limits
(+10% to -10% compared to rated voltage).
1. Check that the unit complies with the refrigeration and
wiring diagrams.
2. Check that all components are as specified on the
drawings.
3. Check that all documents and safety devices required by
applicable European standards are present.
4. Check that there is sufficient clearance around the
system for maintenance and emergency purposes.
5. Check that the clamps on all pipes are secure.
6. Check that the welds and seals are in good condition.
Check there are no refrigerant leaks.
7. Check that all mechanical guards are in place and
functional.
8. Close the drain valve under the evaporator.
9. After opening the water circuit valves, make sure that
water is flowing in the cooler while the pump is running.
11.2 Starting up the compressors
Before starting up, the hydraulic circuit must be drained.
For this operation, the pump(s) must have been started up.
To enable operation without triggering the
compressor(s), all our machines are delivered with the
parameter "compressor on authorisation" set to "NO".
The operation can therefore be carried out with no risk of
starting up the compressors by setting the machine control
to the "ON" position.
Check that the discharge valves and liquid outlet valves
are open.
Power up the crankcase heaters for the compressors 6
hours before the compressors are to be started up.
Once the hydraulic circuit has been drained, set the
"compressor authorisation parameters" to "YES" to
authorise start-up.
Once the compressors have been started up, check:
1. The operation of the water circulation controller.
2. Touch the crankcases to make sure that the heaters are
operating correctly (they should be warm).
11.3 Starting up the unit
The system must have a heat load and water flowing in the
exchangers when it is started up and tested.
-
1. Power up the main board
-
2. Check the configuration of the
Xtraconnect 2
module.
-
3. Re-enter the setpoints.
-
4. Start the unit by pressing the On/Off button.
The internal safety devices are activated. If one of these
safety devices is triggered, trace the fault, reset the safety
device if necessary and press the RESET button on the
console to clear the fault.
The unit will only start after 2 minutes (time required for
inspection and acknowledgement of all safety devices). The
control stages should operate in cascade mode, depending
on the request.
Use either of the following to switch off the unit in non-
emergency situations:
-
The On/Off button on the console;
-
A dry contact on the automatic operation control.
Do not use the master switch as the electrical cabinet must
remain live (frost protection, crankcase heater).
11.4 Post-start-up checks
Checking the compressors
1. Ensure that each compressor is rotating in the correct
direction by checking that the discharge temperature
rises quickly, the HP increases and the LP drops. If
it is rotating in the wrong direction, the electric power
supply is incorrectly wired (reversed phases). To restore
rotation in the correct direction, swap the two power
supply phases.
2. Check the direction of rotation of the fans.
3. Check for any noise generated by the installation and
remedy if necessary.
4. Check the compressor discharge temperature using a
contact sensor.
5. Check that the absorbed current matches the values
indicated on the compressor's data plate.
6. Check all safety devices to make sure they operate
correctly.
7. During start-up and maintenance, the oil level must be
checked; it must be visible in the sight glass, both at full
load and power reduction.
8. Only check the oil level in operation
.
11. SYSTEM START-UP
The compressors are equipped with an automatic soft
start system which reduces the starting torque and the
acceleration times. This protects the mechanical parts
and the motor, and substantially reduces the load on the
system.
Intake valve (option)
The intake valve is used to isolate the compressor from the
refrigerant when work is being carried out.
IMPORTANT
:
-
Make sure that the valves are fully open when the chiller
is started up.
-
Check the tightness of the valve locking lever and make
sure it is properly locked in order to ensure the valve is
held in position.
Summary of Contents for POWERCIAT2 LX
Page 1: ...POWERCIAT2 LX LXC AQUACIAT 2 Instruction manual 04 2014 N 13 47 B...
Page 2: ......
Page 39: ...EN EN 37 NA13 47 B...
Page 40: ...NA13 47 B EN 38...
Page 41: ......