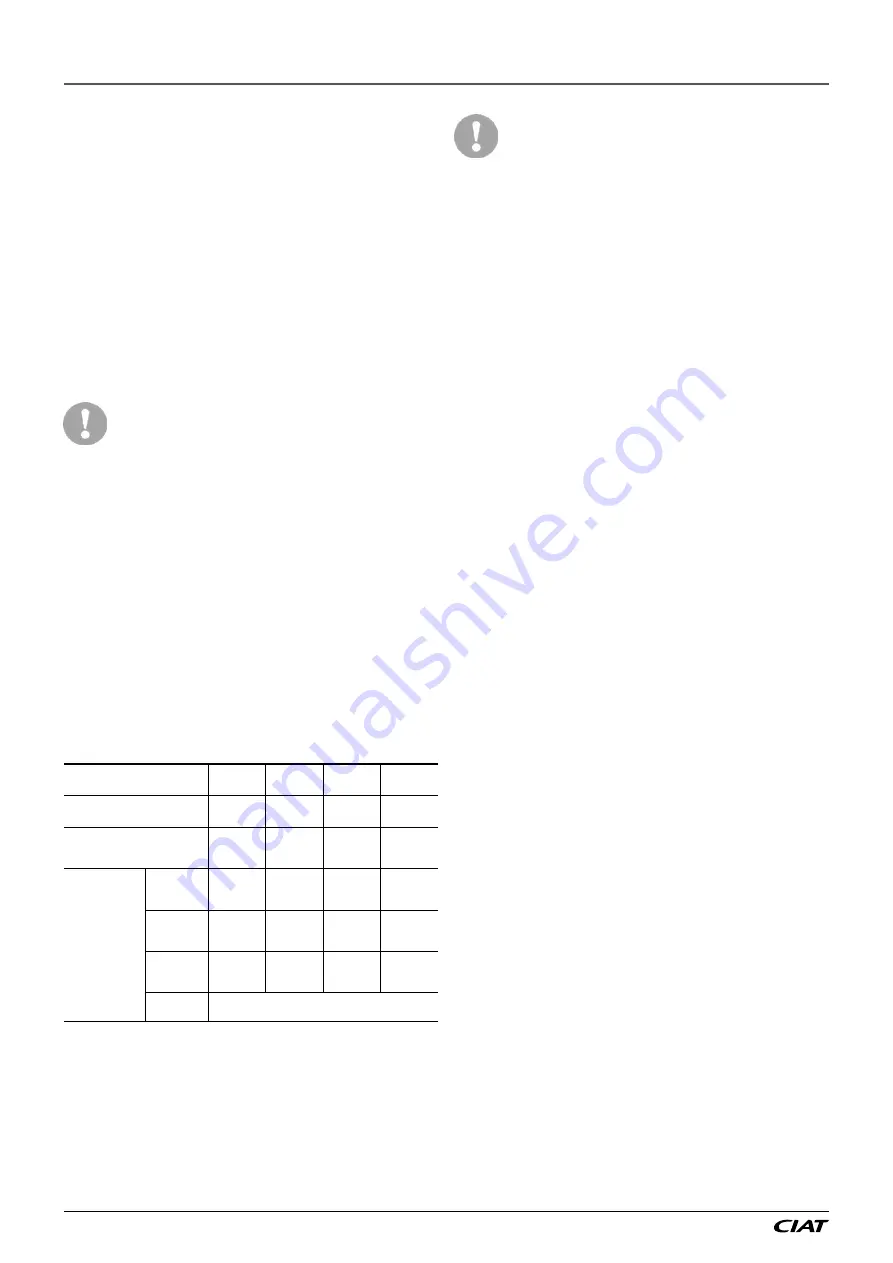
It is recommended to install an indicating device to
show if part of the refrigerant has leaked from the
valve. The presence of oil at the outlet orifice is a
useful indicator that refrigerant has leaked. Keep
this orifice clean to ensure that any leaks are
obvious. The calibration of a valve that has leaked
is generally lower than its original calibration. The
new calibration may affect the operating range. To
avoid nuisance tripping or leaks, replace or re-
calibrate the valve.
Operating checks:
Important information regarding the refrigerant used:
This product contains fluorinated greenhouse gas covered
by the Kyoto protocol.
Fluid type: R407C
Global Warming Potential (GWP): 1774
1. Any intervention on the refrigerant circuit of this
product should be performed in accordance
with the applicable legislation. In the EU, the
regulation is called F-Gas, N°517/2014.
2. Ensure that the refrigerant is never released to
the atmosphere during installation, maintenance
or equipment disposal.
3. The deliberate gas release into the atmosphere
is not allowed.
4. If a refrigerant leak is detected, ensure that it is
stopped and repaired as quickly as possible.
5. Only a qualified and certified personnel can
perform installation operations, maintenance,
refrigerant circuit leak test as well as the
equipment disposal and the refrigerant
recovering.
6. The gas recovery for recycling, regeneration or
destruction is at customer charge.
7. Periodic leak tests have to be carried out by the
customer or by third parties. The EU regulation
set the periodicity here after:
System WITHOUT leakage
detection
No Check 12 Months 6 Months
3 Months
System WITH leakage
detection
No Check 24 Months 12 Months 6 Months
Refrigerant charge/circuit
(CO
2
equivalent)
< 5 Tons
5 ≤ Charge
< 50 Tons
50 ≤
Charge
< 500 Tons
Charge
> 500
Tons
(1)
Refrigerant
charge/
Circuit (kg)
R134A (GWP
1430)
Charge
< 3,5 kg
3,5 ≤
Charge
< 34,9 kg
34,9 ≤
Charge
< 349,7 kg
Charge
> 349,7 kg
R407C
(GWP 1774)
Charge
< 2,8 kg
2,8 ≤
Charge
< 28,2 kg
28,2 ≤
Charge
< 281,9 kg
Charge
> 281,9 kg
R410A (GWP
2088)
Charge
< 2,4 kg
2,4 ≤
Charge
< 23,9 kg
23,9 ≤
Charge
< 239,5 kg
Charge
> 239,5 kg
HFO’s:
R1234ze
No requirement
(1) From 01/01/2017, units must be equipped with a leakage detection system
8. A logbook must be established for equipments
subject to periodic leak tests. It should contain
the quantity and the type of fluid present within
the installation (added and recovered), the
quantity of recycled fluid, regenerated or
destroyed, the date and output of the leak test,
the designation of the operator and its belonging
company, etc.
9. Contact your local dealer or installer if you have
any questions.
Protection device checks:
-
If no national regulations exist, check the protection
devices on site in accordance with standard EN378: once
a year for the high-pressure switches, every five years
for external relief valve.
The company or organisation that conducts a pressure switch
test shall establish and implement a detailed procedure to fix:
• Safety measures
• Measuring equipment calibration
• Validating operation of protective devices
• Test protocols
• Recommissioning of the equipment.
Consult CIAT Service for this type of test. CIAT mentions here
only the principle of a test without removing the pressure switch:
• Verify and and record the set-points of pressure switches
and relief devices (valves and possible rupture discs)
• Be ready to switch-off the main disconnect switch of the
power supply if the pressure switch does not trigger (avoid
over-pressure or excess gas in case of valves on the high-
pressure side with the recovery condensers)
• Connect a pressure gauge protected against pulsations
(filled with oil with maximum pointer if mechanical),
preferably calibrated (the values displayed on the user
interface may be inaccurate in an instant reading because
of the scanning delay applied in the control)
• Complete an HP Test as provided by the software (refer to
the Control IOM for details).
If the machine operates in a corrosive environment, inspect
the protection devices more frequently.
Regularly carry out leak tests and immediately repair any
leaks.
Ensure regularly that the vibration levels remain acceptable
and close to those at the initial unit start-up.
Before opening a refrigerant circuit, transfer the refrigerant
to bottles specifically provided for this purpose and consult
the pressure gauges.
Change the refrigerant after an equipment failure, following
a procedure such as the one described in NF E29-795 or
carry out a refrigerant analysis in a specialist laboratory.
If the refrigerant circuit remains open for longer than a day
after an intervention (such as a component replacement),
the openings must be plugged and the circuit must be
charged with nitrogen (inertia principle). The objective is to
prevent penetration of atmospheric humidity and the
corrosion on the unprotected internal steel walls.
1.5 - Repair safety considerations
All installation parts must be maintained by the personnel in
charge, in order to avoid deterioration and injury. Faults and leaks
must be repaired immediately. The authorized technician must
have the responsibility to repair the fault immediately. After each
repair of the unit, check the operation of the protection devices
and create a report of the parameter operation at 100%.
Comply with the regulations and recommendations in unit and
HVAC installation safety standards, such as: EN 378 and ISO 5149.
1 - INTRODUCTION
AQUACIAT
CALÉO™
TD
EN-6