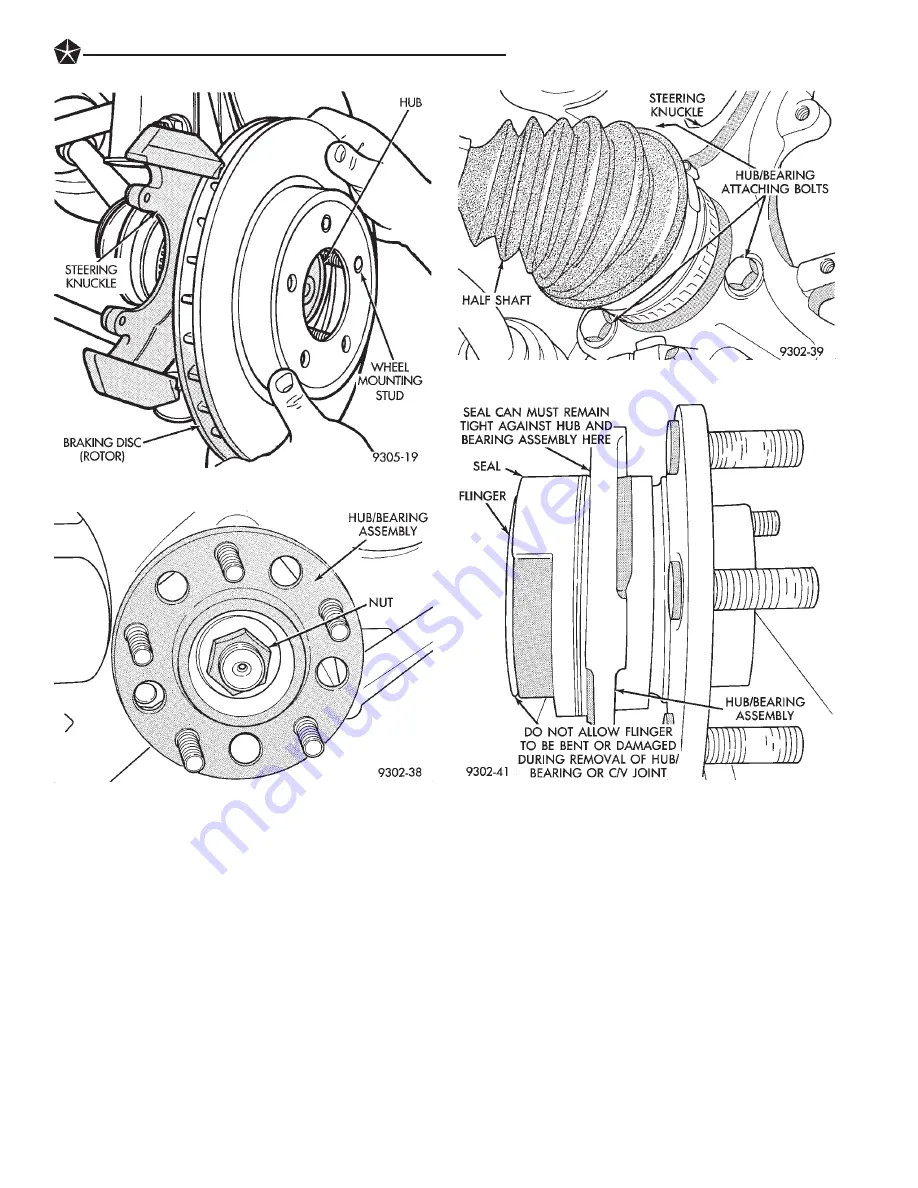
(7) Remove hub and bearing assembly from steer-
ing knuckle, by sliding it straight out of steering
knuckle and off end of stub axle (Fig. 6). If hub and
bearing assembly will not slide out of knuckle. Insert
a pry bar between hub and bearing assembly and
steering knuckle (Fig. 7) and gently pry hub and
bearing from knuckle. If stub shaft is frozen to hub
and bearing assembly tap end of stub shaft with soft
face hammer to free it from hub and bearing spline.
INSTALLATION
CAUTION: Hub and bearing assembly mounting
surfaces on steering knuckle (Fig. 8) must be
smooth and completely free of foreign material or
nicks.
CAUTION: When installing hub and bearing assem-
bly into steering knuckle, be careful not to damage
the flinger disc (Fig. 5) on hub and bearing assem-
bly. If flinger disc becomes damaged, hub and bear-
ing assembly MUST not be used and MUST be
replaced with a new hub and bearing assembly.
(1) Install hub and bearing assembly onto stub
shaft and into steering knuckle until squarely seated
on face of steering knuckle. (Fig. 6).
(2) Install the 3 hub and bearing assembly to
steering knuckle attaching bolts (Fig. 9). Equally
tighten all 3 mounting bolts until hub and bearing
assembly is squarely seated against front of steering
knuckle. Then torque all 3 hub and bearing assembly
mounting bolts to 110 N
I
m (80 ft.lbs.).
Fig. 2 Removing Braking Disc
Fig. 3 Hub And Bearing To Stub Axle Retaining Nut
Fig. 4 Hub And Bearing Assembly Retaining Bolts
Fig. 5 Hub And Bearing Assembly Seal
SUSPENSION AND DRIVESHAFTS
2 - 35
Summary of Contents for Concorde 1993
Page 4: ......
Page 7: ...LUBRICATION AND MAINTENANCE SCHEDULES LUBRICATION AND MAINTENANCE 0 3 ...
Page 22: ......
Page 24: ...Fig 1 L H Platform Front Suspension 2 2 SUSPENSION AND DRIVESHAFTS ...
Page 25: ...SUSPENSION STEERING DIAGNOSIS FRONT WHEEL DRIVE SUSPENSION AND DRIVESHAFTS 2 3 ...
Page 27: ...Fig 2 L H Platform Front Suspension SUSPENSION AND DRIVESHAFTS 2 5 ...
Page 44: ...Fig 1 Front Stabilizer Bar And Stabilizer Bar Mounting 2 22 SUSPENSION AND DRIVESHAFTS ...
Page 63: ...SUSPENSION STEERING DIAGNOSIS FRONT WHEEL DRIVE SUSPENSION AND DRIVESHAFTS 2 41 ...
Page 75: ...Fig 1 L H Platform Fully Independent Rear Suspension SUSPENSION AND DRIVESHAFTS 2 53 ...
Page 92: ...SPECIFICATIONS ALIGNMENT SPECIFICATIONS AT CURB HEIGHT 2 70 SUSPENSION AND DRIVESHAFTS ...
Page 94: ......
Page 97: ...Fig 3 Proper Nut Thread Size And Tube Routing ABS Equipped BRAKES 5 3 ...
Page 105: ...BRAKE SYSTEM DIAGNOSTICS BRAKES 5 11 ...
Page 106: ...BRAKE SYSTEM DIAGNOSTICS 5 12 BRAKES ...
Page 107: ...BRAKE SYSTEM DIAGNOSTICS BRAKE SYSTEM DIAGNOSTICS BRAKES 5 13 ...
Page 145: ...FIG 2 PARKING BRAKE CABLE ROUTING BRAKES 5 51 ...
Page 198: ...BRAKE ACTUATION SYSTEM TIGHTENING REFERENCE 5 104 ANTI LOCK BRAKE SYSTEM ...
Page 200: ...COOLING SYSTEM DIAGNOSIS 7 2 COOLING SYSTEM ...
Page 201: ...COOLING SYSTEM DIAGNOSIS COOLING SYSTEM 7 3 ...
Page 202: ...COOLING SYSTEM DIAGNOSIS 7 4 COOLING SYSTEM ...
Page 203: ...COOLING SYSTEM DIAGNOSIS COOLING SYSTEM 7 5 ...
Page 204: ...COOLING SYSTEM DIAGNOSIS 7 6 COOLING SYSTEM ...
Page 205: ...COOLING SYSTEM DIAGNOSIS COOLING SYSTEM 7 7 ...
Page 220: ...SPECIFICATIONS TORQUE COOLING SYSTEM CAPACITY 7 22 COOLING SYSTEM ...
Page 225: ...Fig 7 Battery Diagnostics BATTERY STARTING CHARGING SYSTEMS DIAGNOSTICS 8A 5 ...
Page 236: ...Fig 14 Starter Relay Tests 8A 16 BATTERY STARTING CHARGING SYSTEMS DIAGNOSTICS ...
Page 239: ...Fig 1 Charging Diagnostics BATTERY STARTING CHARGING SYSTEMS DIAGNOSTICS 8A 19 ...
Page 242: ...Fig 6 Generator Fault Codes 8A 22 BATTERY STARTING CHARGING SYSTEMS DIAGNOSTICS ...
Page 243: ...Fig 7 Check For Inadequate Low Charging BATTERY STARTING CHARGING SYSTEMS DIAGNOSTICS 8A 23 ...
Page 244: ...Fig 8 Check For Overcharging 8A 24 BATTERY STARTING CHARGING SYSTEMS DIAGNOSTICS ...
Page 258: ......
Page 282: ......
Page 291: ...Fig 25 Instrument Panel Breakdown INSTRUMENT PANEL AND GAUGES 8E 9 ...
Page 292: ...Fig 26 Instrument Panel Breakdown 207 8E 10 INSTRUMENT PANEL AND GAUGES ...
Page 296: ......
Page 298: ...Fig 1 Radio Diagnosis 8F 2 AUDIO SYSTEM ...
Page 299: ...Fig 2 Radio Connector Circuits AUDIO SYSTEM 8F 3 ...
Page 306: ......
Page 308: ...Fig 2 Horn Diagnosis 8G 2 HORNS ...
Page 310: ......
Page 313: ...Fig 4 System Diagnosis SPEED CONTROL SYSTEM 8H 3 ...
Page 314: ...Fig 5 System Diagnosis Continued 8H 4 SPEED CONTROL SYSTEM ...
Page 320: ......
Page 324: ......
Page 327: ...Fig 5 Wiper Motor Runs Diagnosis WINDSHIELD WIPER AND WASHER SYSTEMS 8K 3 ...
Page 328: ...Fig 6 Wiper Motor Will Not Run Diagnosis 8K 4 WINDSHIELD WIPER AND WASHER SYSTEMS ...
Page 350: ......
Page 360: ......
Page 364: ......
Page 370: ......
Page 374: ......
Page 382: ......
Page 388: ...ENGINE DIAGNOSIS PERFORMANCE ENGINE 9 5 ...
Page 389: ...ENGINE DIAGNOSIS MECHANICAL 9 6 ENGINE ...
Page 416: ...ENGINE SPECIFICATIONS 3 3L ENGINE 9 33 ...
Page 417: ...ENGINE SPECIFICATIONS CONT 9 34 3 3L ENGINE ...
Page 418: ...ENGINE SPECIFICATIONS CONT 3 3L ENGINE 9 35 ...
Page 419: ...ENGINE SPECIFICATIONS CONT 9 36 3 3L ENGINE ...
Page 420: ...TORQUE 3 3L ENGINE 9 37 ...
Page 450: ...ENGINE SPECIFICATIONS 3 5L ENGINE 9 67 ...
Page 451: ...ENGINE SPECIFICATIONS CONT 9 68 3 5L ENGINE ...
Page 452: ...ENGINE SPECIFICATIONS CONT TORQUE 3 5L ENGINE 9 69 ...
Page 453: ......
Page 456: ...EXHAUST SYSTEM DIAGNOSIS EXHAUST SYSTEM AND INTAKE MANIFOLD 11 3 ...
Page 467: ......
Page 470: ...EXHAUST SYSTEM DIAGNOSIS EXHAUST SYSTEM AND INTAKE MANIFOLD 11 3 ...
Page 481: ......
Page 485: ...Fig 6 Engine Compartment Side View 13 4 FRAME AND BUMPERS ...
Page 486: ...Fig 7 Forward Frame Section and Engine Cradle FRAME AND BUMPERS 13 5 ...
Page 487: ...Fig 8 Rear Frame Section 13 6 FRAME AND BUMPERS ...
Page 491: ...Fig 6 Engine Compartment Side View 13 4 FRAME AND BUMPERS ...
Page 492: ...Fig 7 Forward Frame Section and Engine Cradle FRAME AND BUMPERS 13 5 ...
Page 493: ...Fig 8 Rear Frame Section 13 6 FRAME AND BUMPERS ...
Page 507: ...Fig 37 Chassis Fuel Tubes 14 14 FUEL SYSTEMS ...
Page 534: ...3 3L FUEL INJECTOR DIAGNOSIS FUEL SYSTEMS 14 41 ...
Page 535: ...3 5L FUEL INJECTOR DIAGNOSIS 14 42 FUEL SYSTEMS ...
Page 544: ...POWERTRAIN CONTROL MODULE 60 WAY CONNECTOR FUEL SYSTEMS 14 51 ...
Page 545: ...DIAGNOSTIC TROUBLE CODE DESCRIPTION 14 52 FUEL SYSTEMS ...
Page 546: ...DIAGNOSTIC TROUBLE CODE DESCRIPTION CONTINUED FUEL SYSTEMS 14 53 ...
Page 547: ...DIAGNOSTIC TROUBLE CODE DESCRIPTION CONTINUED 14 54 FUEL SYSTEMS ...
Page 567: ...STEERING COMPONENTS SERVICE DIAGNOSIS POWER STEERING SERVICE DIAGNOSIS 19 2 STEERING ...
Page 568: ...POWER STEERING SERVICE DIAGNOSIS STEERING 19 3 ...
Page 569: ...POWER STEERING SERVICE DIAGNOSIS 19 4 STEERING ...
Page 570: ...POWER STEERING SERVICE DIAGNOSIS STEERING 19 5 ...
Page 571: ...POWER STEERING SERVICE DIAGNOSIS 19 6 STEERING ...
Page 572: ...POWER STEERING SERVICE DIAGNOSIS STEERING 19 7 ...
Page 591: ...Fig 1 L H Platform Saginaw Tilt Steering Column 19 26 STEERING ...
Page 604: ...DIAGNOSIS GUIDE VEHICLE WILL NOT MOVE TRANSAXLE 21 5 ...
Page 605: ...DIAGNOSIS GUIDE FLUID LEAKS 21 6 TRANSAXLE ...
Page 606: ...DIAGNOSTIC TROUBLE CODE CHART A TRANSAXLE 21 7 ...
Page 607: ...DIAGNOSIS CHART B 21 8 TRANSAXLE ...
Page 682: ...DIAGNOSTIC TROUBLE CODE 11 DIAGNOSTIC TROUBLE CODE 12 TRANSAXLE 21 83 ...
Page 683: ...DIAGNOSTIC TROUBLE CODE 13 DIAGNOSTIC TROUBLE CODE 14 21 84 TRANSAXLE ...
Page 684: ...DIAGNOSTIC TROUBLE CODE 15 DIAGNOSTIC TROUBLE CODE 16 TRANSAXLE 21 85 ...
Page 685: ...DIAGNOSTIC TROUBLE CODE 17 DIAGNOSTIC TROUBLE CODE 18 21 86 TRANSAXLE ...
Page 686: ...DIAGNOSTIC TROUBLE CODE 19 DIAGNOSTIC TROUBLE CODE 20 TRANSAXLE 21 87 ...
Page 687: ...DIAGNOSTIC TROUBLE CODE 21 27 21 88 TRANSAXLE ...
Page 689: ...DIAGNOSTIC TROUBLE CODE 29 DIAGNOSTIC TROUBLE CODE 31 32 21 90 TRANSAXLE ...
Page 690: ...DIAGNOSTIC TROUBLE CODE 36 DIAGNOSTIC TROUBLE CODE 37 TRANSAXLE 21 91 ...
Page 691: ...DIAGNOSTIC TROUBLE CODE 38 21 92 TRANSAXLE ...
Page 692: ...DIAGNOSTIC TROUBLE CODE 41 44 TRANSAXLE 21 93 ...
Page 693: ...DIAGNOSTIC TROUBLE CODE 45 DIAGNOSTIC TROUBLE CODE 46 21 94 TRANSAXLE ...
Page 695: ...DIAGNOSTIC TROUBLE CODE 50 58 21 96 TRANSAXLE ...
Page 696: ...DIAGNOSTIC TROUBLE CODE 60 62 TRANSAXLE 21 97 ...
Page 697: ...42LE HYDRAULIC SCHEMATICS 21 98 TRANSAXLE ...
Page 698: ... TRANSAXLE 21 99 ...
Page 699: ...21 100 TRANSAXLE ...
Page 700: ...TRANSAXLE 21 101 ...
Page 701: ...21 102 TRANSAXLE ...
Page 702: ...TRANSAXLE 21 103 ...
Page 703: ...21 104 TRANSAXLE ...
Page 704: ...TRANSAXLE 21 105 ...
Page 705: ...21 106 TRANSAXLE ...
Page 706: ...TRANSAXLE 21 107 ...
Page 707: ...21 108 TRANSAXLE ...
Page 708: ...TRANSAXLE 21 109 ...
Page 709: ...21 110 TRANSAXLE ...
Page 710: ...42LE SPECIFICATIONS 42LE FOUR SPEED AUTOMATIC TRANSAXLE TRANSAXLE 21 111 ...
Page 712: ...MASTER SHIM CHART TRANSAXLE 21 113 ...
Page 713: ......
Page 717: ...Fig 4 Tire Wear Patterns 22 4 WHEELS TIRES ...
Page 718: ...LEAD CORRECTION CHART WHEELS TIRES 22 5 ...
Page 765: ...Fig 5 Charge Determination Graph 24 6 HEATING AND AIR CONDITIONING ...
Page 781: ...DRB II SCAN TOOL FLOW CHART MANUAL ATC 24 22 HEATING AND AIR CONDITIONING ...
Page 782: ...DRB II SCAN TOOL MENU BODY SECTION CLIMATE CONTROL ITEMS HEATING AND AIR CONDITIONING 24 23 ...
Page 783: ...DRB II SCAN TOOL FLOW CHART SYSTEM TESTS 24 24 HEATING AND AIR CONDITIONING ...
Page 786: ...ENGINE VACUUM SCHEMATIC 3 3L ENGINE EMISSION CONTROL SYSTEMS 25 3 ...
Page 787: ...ENGINE VACUUM SCHEMATIC 2 5L ENGINE 25 4 EMISSION CONTROL SYSTEMS ...
Page 796: ...EGR DIAGNOSIS CHART 3 3L ENGINE EMISSION CONTROL SYSTEMS 25 13 ...
Page 804: ...CONVERSION TABLES INTRODUCTION 5 ...
Page 805: ...CONVERSION TABLES INTERNATIONAL CONTROL AND DISPLAY SYMBOLS 6 INTRODUCTION ...
Page 810: ... 520 QVWDOODWLRQ QG 2SHUDWLRQ QVWUXFWLRQ RRNOHW ...