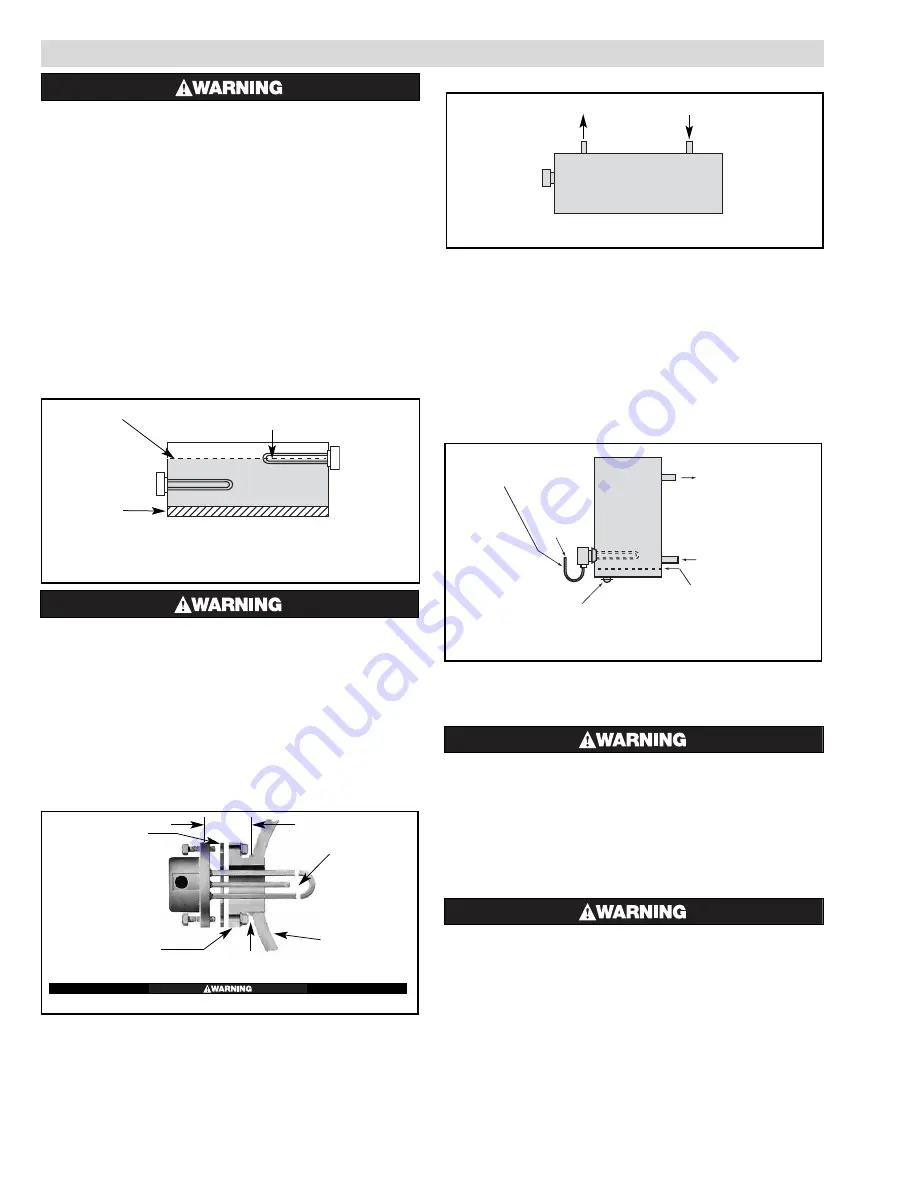
INSTALLATION
ELECTRIC SHOCK HAZARD. Disconnect all power
before installing or servicing heater. Failure to do so
could result in personal injury or property damage.
Heater must be installed by a qualified person in accor-
dance with the National Electrical Code, NFPA 70.
1.
Before installing, unpack and check your TM series immersion
heater for any damage that may have occurred during shipment.
Report any claims to you carrier if damage has ocurred in ship-
ment.
Do not operate damaged equipment. Consult
factory for instructions.
2.
Check to ensure that the line voltage is the same as that stamped
on the nameplate. Verify wattage and capacity versus the require-
ments at installation site.
3.
Do not bend the heating elements. If bending is necessary,
consult factory.
4. IMPORTANT:
Mount the heater in the tank so that the liquid
level will always be above the effective heated portion of the
heater. If the heater is not properly submerged, it may overheat and
damage the heating elements (see Figure 1).
FIRE HAZARD. If the heater is not properly sub-
merged, the heating elements will overheat and could
result in a fire or damaged equipment.
5.
Where work will pass over or near equipment, additional protec-
tion such as a metal guard may be needed.
6.
Heater must not be operated in sludge.
7.
The gasket surface must be clean and dry before the heater is seat-
ed (see Figure 2).
8.
Closed Tank Installation
Note:
When heating in closed vessels, controls and
back-up controls must be used to prevent buildup of temper-
ature and/or pressure.
A. Horizontal Position (Figure 3)
A1.
Place heater at an elevation so that natural circulation can
take place.
A2.
Position outlet and inlet in a vertical plane, facing upward
to prevent air pockets. Be sure all trapped air is removed from
the closed tank. Bleed the air out of the liquid piping system
and heater enclosure prior to operation.
A3. IMPORTANT:
Heater should never be located at the
highest point of the water system. Provide expansion tank
if necessary.
A4.
Heaters shall be supported if the immersion length is greater
than 36”.
B. Vertical Position (Figure 4)
9.
A drip loop is recommended to minimize passage of moisture
from condensation along wiring into terminal box enclosure and
connections.
FIRE HAZARD. Since heaters are capable of developing
high temperatures, extreme care should be taken to:
A.
Use explosion-resistant terminal enclosures in hazardous loca-
tions. See Chromalox catalog for selection of explosion-resis-
tant terminal enclosure for hazardous locations.
B.
Avoid contact between heater and combustible materials.
C.
Keep combustible materials far enough away to be free of the
effects of high temperatures.
FREEZE HAZARD. This unit may be equipped with a
thermowell for process control or over-temperature
control. Do not allow moisture to accumulate in ther-
mowell. Freezing temperatures can cause damage
that may result in the heated medium leaking into ter-
minal enclosure.
Note:
Locate Heater as low as possible for maximum heated liquid storage capac-
ity. Heat does not move downward.
Figure 1 - Open Tank Installation
Expected Low Liquid
Level
This Portion of the Heater Above Liquid Level and
Exposed to Air Will Lead to Premature Failure of Element
Expected Maximum
Sediment Level
Figure 2 - Flanged Mounting
Care must be taken to ensure the heated portion does not extend into the coupling area.
Gasket
Cold End (See Warning)
Element
Tank
Wall
Standard
Pipe Flange
Weld
Locate Drain Pipe at Bottom of Heater,
Sediment Deposits may be
Removed Through Drain Pipe
Maximum Sediment Level.
Install Heater
Above
This Level But As
Near to it as Possible for Maximum
Heated Liquid Storage Capacity
Suitable
Wiring
Drip Loop Recommended
to Minimize Passage of Moisture
Along Wiring Into Terminal
Wiring and Connections
Outlet
Inlet
Figure 4 - Closed Tank in Vertical Position
Heater
Outlet
Inlet
Note: In A Forced Circulation System, Use Pump In Inlet Side.
Figure 3 Closed Tank in Horizontal Position
2