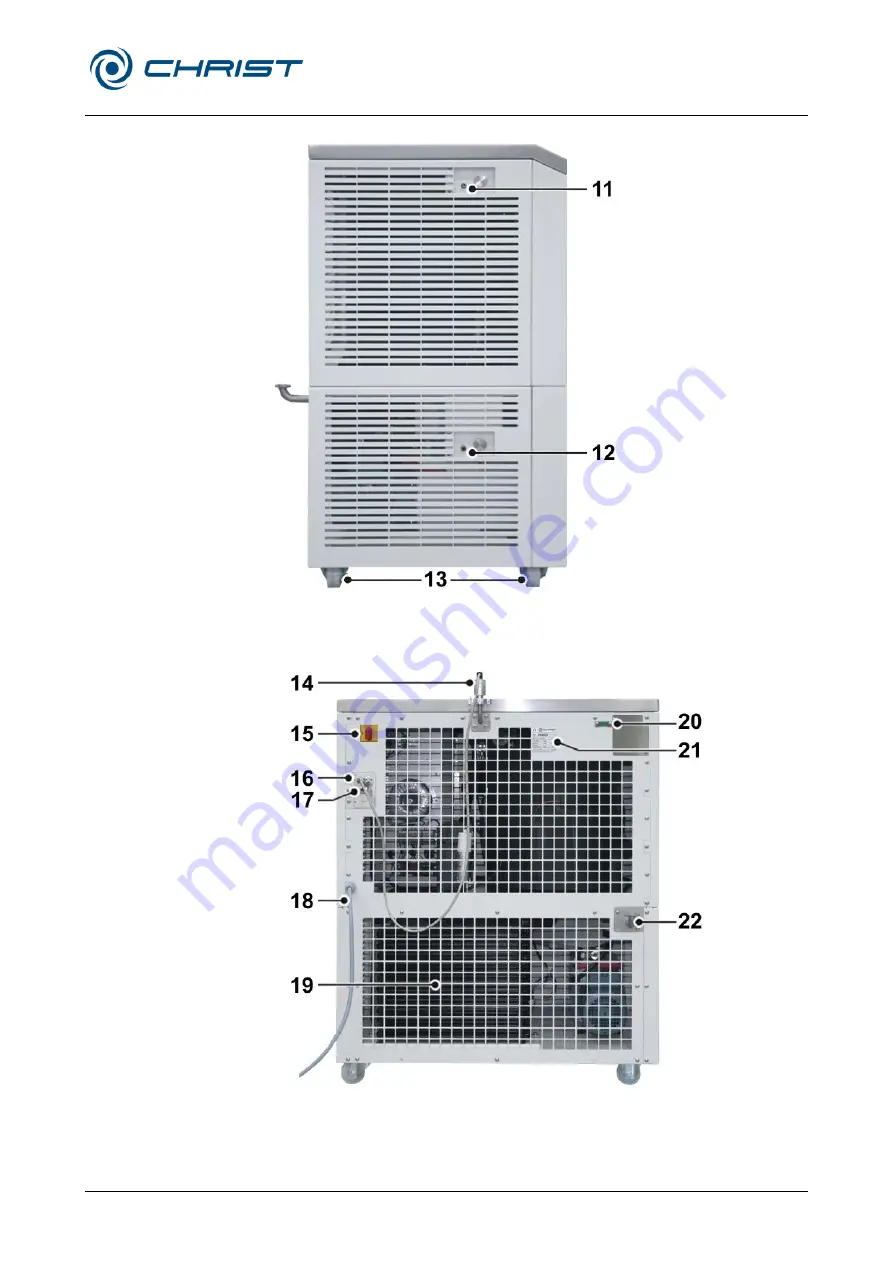
Freeze-dryer Delta 1-24 LSCplus
Freeze-dryer Delta 2-24 LSCplus
2 Layout and mode of operation
Version 04/2013, Rev. 2.9 of 09/03/2020
• sb-dc
15 / 125
Translation of the original operating manual
11
Aeration valve
12
Media drain valve
13
Fixed castors
Fig. 5: Left side of the freeze-dryer
14 Vacuum sensor
15 Mains voltage (Main
switch)
16 Electrical connection
of the vacuum sensor
17 Serial interface
18 Mains cable
19 Heat exchanger of the
refrigeration unit
(behind the panel)
20
Option: Connection
for electrical lifting
device
21 Name plate (see
chapter 2.1.2 - "Name
plate")
22 Vacuum connection
Fig. 6: Rear side of the freeze-dryer