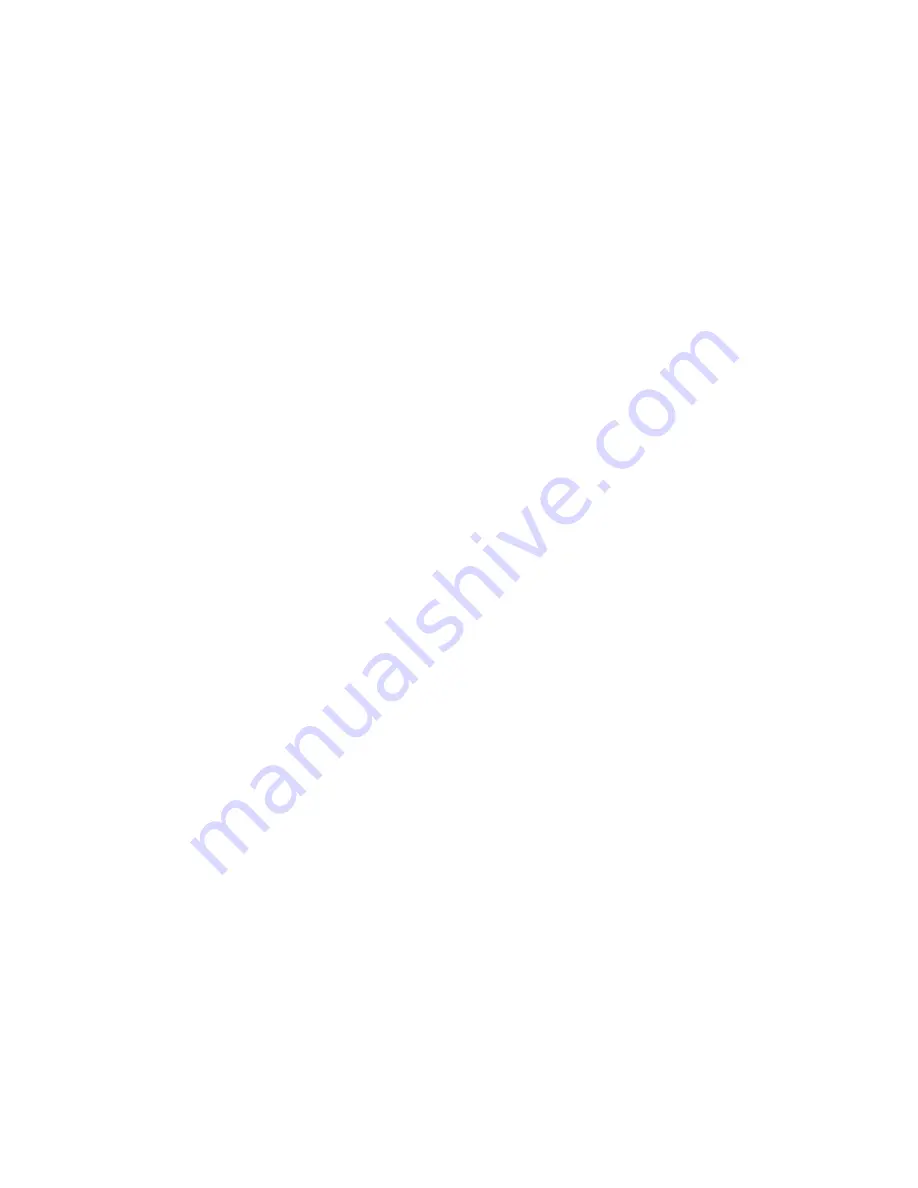
7
The FLEX-IR™ should be attached directly to the power unit funnel as shown on page 6. Below
the FLEX-IR™ a 3” PVC tube can be used to extend to the feeder. If a 3” tube is used, make
sure the tube is fully inserted into the FLEX-IR™ to provide a smooth inner wall for feed to
slide on.
In some applications a 4” tube may be required below the FLEX-IR™ in order for feed to
completely clear out of the FLEX-IR™ sensor. In this case the 3” tube would not be used and a
4” tube would go around the outside of the outlet of the FLEX-IR™. In any case the extension
tube below the FLEX-IR™ should be straight and not get smaller as it approaches the feeder or
else feed bridging will result.
If the tubing from the power unit funnel to the feeder is required to be at an angle, such as 45
degrees, a 45 degree elbow should be placed between the FLEX-IR™ and the power unit funnel.
An elbow should not be placed between the FLEX-IR™ and the feeder unless it causes the feed
flow to be more vertical.
A "Y" drop at the last feeder may require the addition of an extra drop in the line right before
feed reaches the power unit. This extra drop would supply one side of the "Y" and the FLEX-
IR™ mounted at an angle on the power unit funnel would supply the other side of the "Y".
Electrical Wiring
The FLEX-IR™ is capable of operating a feed motor up to 1.5 HP at 240 volts without an
external relay. Use of an external relay above these loads is required; use of an external relay at
or below these loads is optional.
Description of FLEX-IR™ Wires:
Black: 50-300 VAC
Blue:
50-300 VAC
Red:
Dry Contact
Orange: Dry Contact
Grounding is not required.