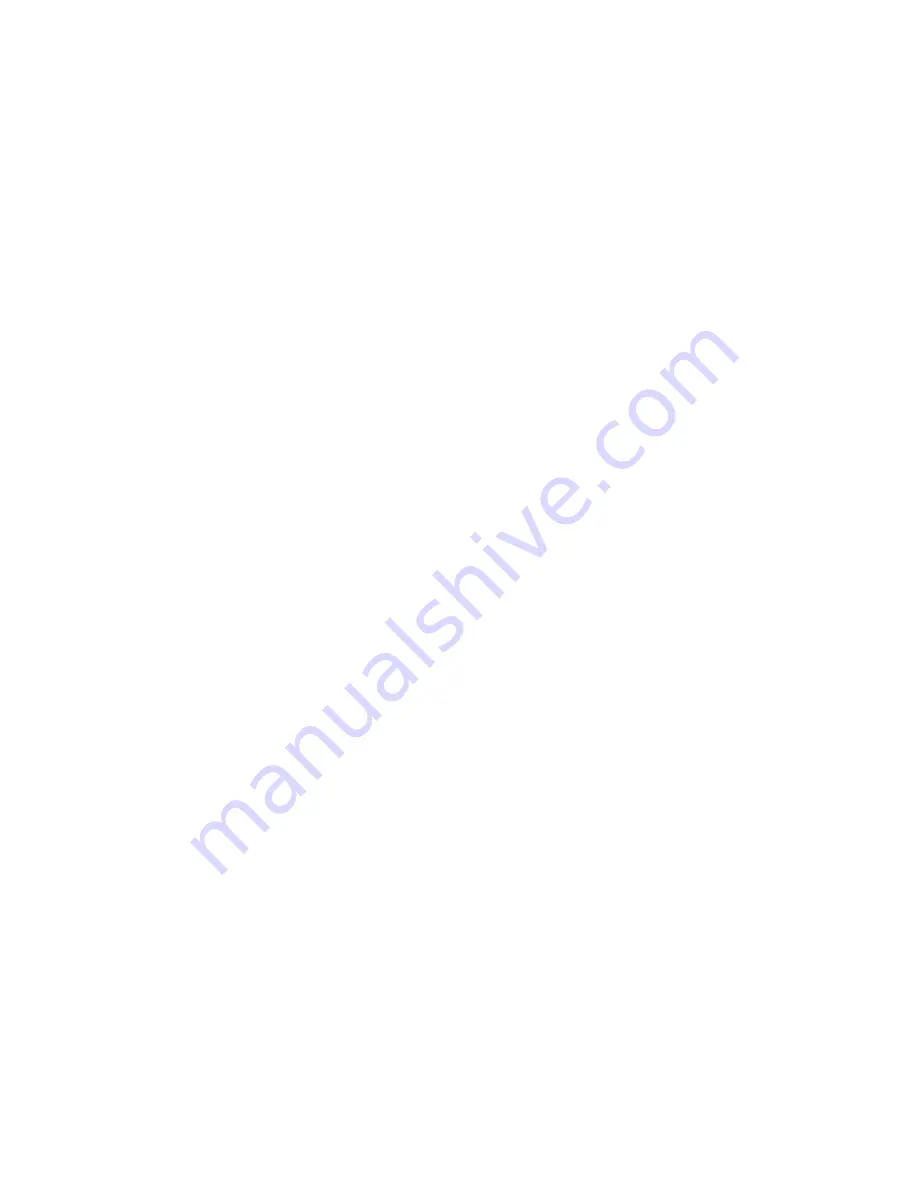
4
3. INSTALLATION
3.1 SETUP
Place the machine in a ventilated area.
Dust, dirt, or any other foreign material that may enter the machine can restrict ventilation which could affect the ma-
chine’s performance.
3.2 INPUT POWER CONNECTIONS
All sections concerning the installation of this machine must be read carefully.
This machine must be installed by skilled personnel.
Make sure that the input power plug has been disconnected before inspecting, maintaining, or servicing.
Connect the yellow-green wire to a good electrical ground.
Do not use water pipes as a ground conductor.
After a final inspection, the machine should be connected to the input supply voltage marked on the input power cord.
Mount a plug on the power supply cable that corresponds to the input power drawn by the machine.
3.3 CONNECTING the work return lead clamp
Attach the work return clamp to the work to be welded.
Make sure the ground clamp is tightly fastened to the work return cable and periodically check this connection remains
well tightened. A loose connection can cause weld current drops or overheating of the work return lead and clamp, which
creates the risk of burns from accidental contact with the work return lead. The weld circuit must not be placed deliberate-
ly in direct or indirect contact with the ground conductor.
If the work to be welded is attached deliberately to the ground by a protection lead, then the connection must be the most
direct possible and must be done using a lead that has a cross section that is at least equal to the cross section of the
work return lead being used for the weld circuit. The protection lead must also be attached to the work at the same spot as
the work return lead. To do so, a second ground clamp, fitted to the protection lead, must be attached next to the ground
clamp of the work return lead.
NOTE:
Small cross section and long extension cable will reduce the output current.
Summary of Contents for M30
Page 10: ...NOTES 10 ...
Page 11: ...NOTES 11 ...