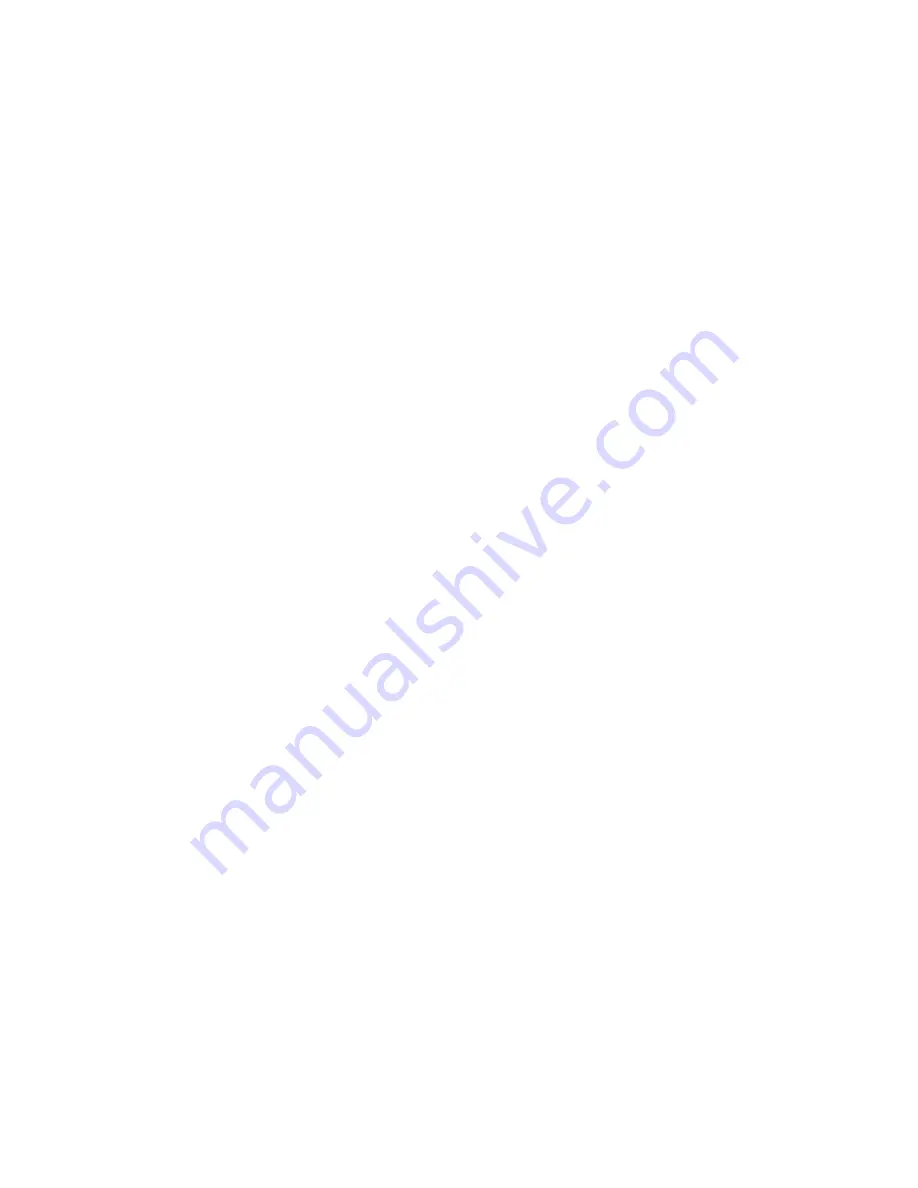
SKU 98058
For technical questions, please call 1-800-444-3353.
Page 5
always use blades with correct
7.
size and shape (diamond versus
round) of arbor holes.
Blades that
do not match the mounting hardware
of the saw will run eccentrically,
causing loss of control.
never use damaged or incorrect
8.
blade washers or bolt.
The blade
washers and bolt were specially
designed for your saw, for optimum
performance and safety of operation.
Causes and Operator prevention
9.
of Kickback:
Kickback is a sudden reaction to a
•
pinched, bound or misaligned saw
blade, causing an uncontrolled saw
to lift up and out of the workpiece
toward the operator;
When the blade is pinched or bound
•
tightly by the kerf closing down, the
blade stalls and the motor reaction
drives the unit rapidly back toward
the operator;
If the blade becomes twisted or
•
misaligned in the cut, the teeth at
the back edge of the blade can dig
into the top surface of the wood
causing the blade to climb out of
the kerf and jump back toward the
operator.
Kickback is the result of saw misuse
and/or incorrect operating procedures
or conditions and can be avoided by
taking proper precautions as given
below:
Maintain a firm grip with both
a.
hands on the saw and position
your arms to resist kickback
forces. position your body to
either side of the blade, but not in
line with the blade.
Kickback could
cause the saw to jump backwards,
but kickback forces can be controlled
by the operator, if proper precautions
are taken.
when blade is binding, or when
b.
interrupting a cut for any reason,
release the trigger and hold the
saw motionless in the material
until the blade comes to a
complete stop. never attempt to
remove the saw from the work or
pull the saw backward while the
blade is in motion or kickback
may occur.
Investigate and take
corrective actions to eliminate the
cause of blade binding.
when restarting a saw in the
c.
workpiece, centre the saw blade in
the kerf and check that saw teeth
are not engaged into the material.
If saw blade is binding, it may walk up
or kickback from the workpiece as the
saw is restarted.
support large panels to minimise
d.
the risk of blade pinching and
kickback.
Large panels tend to sag
under their own weight. Supports
must be placed under the panel on
both sides, near the line of cut and
near the edge of the panel.
do not use dull or damaged
e.
blades.
Unsharpened or improperly
set blades produce narrow kerf
causing excessive friction, blade
binding and kickback.
Blade depth and bevel adjusting
f.
locking levers must be tight and
secure before making cut.
If blade
adjustment shifts while cutting, it may
cause binding and kickback.
use extra caution when making a
g.
″plunge cut″ into existing walls or
other blind areas.
The protruding