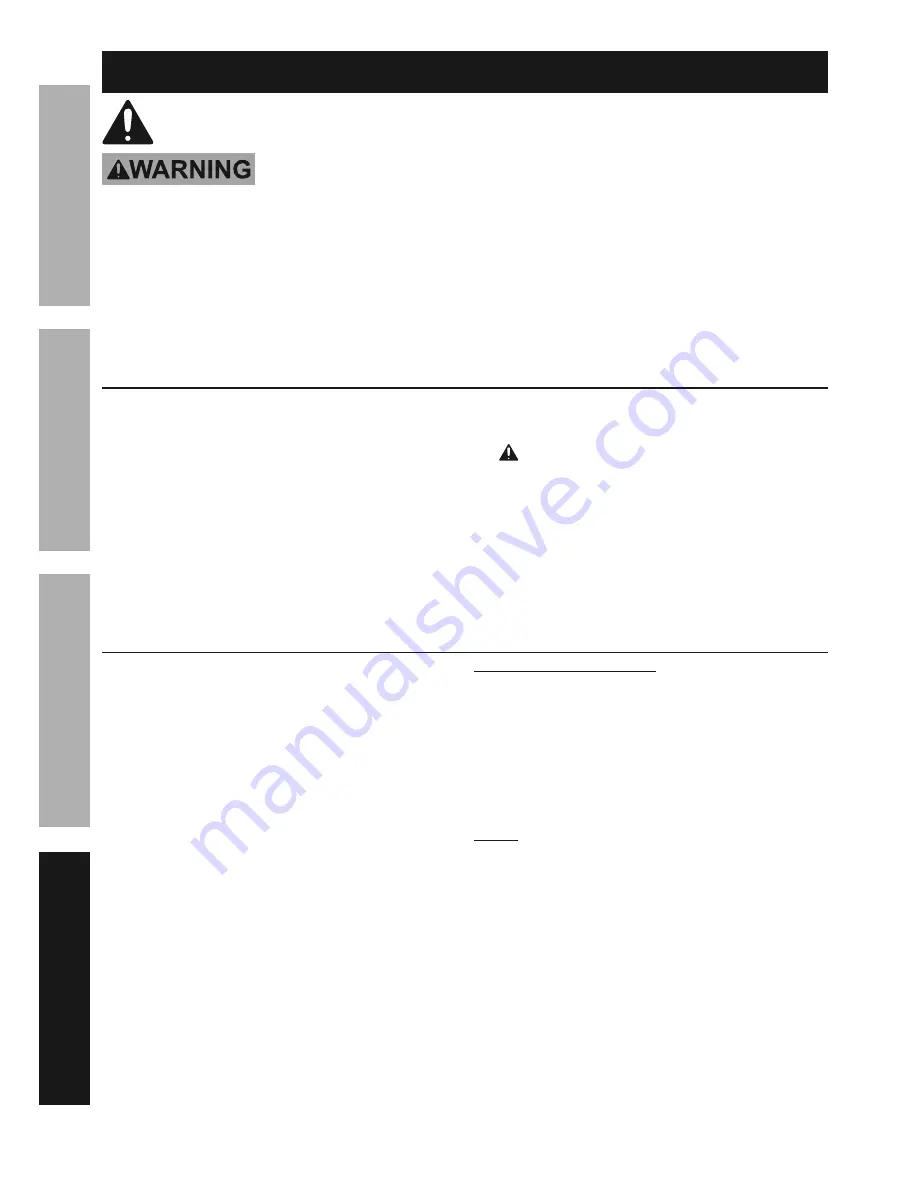
Page 14
For technical questions, please call 1-888-866-5797.
Item 61971
SAFETY
O
PERA
TION
M
AINTENANCE
SETUP
Maintenance and Servicing
Procedures not specifically explained in this manual must
be performed only by a qualified technician.
TO PREVENT SERIOUS INJURY FROM ACCIDENTAL OPERATION:
Turn the Power Switch of the tool off and unplug the tool from its electrical
outlet before performing any procedure in this section.
TO PREVENT SERIOUS INJURY FROM TOOL FAILURE:
Do not use damaged equipment. If abnormal noise or vibration
occurs, have the problem corrected before further use.
Cleaning, Maintenance, and Lubrication
1.
BEFORE EACH USE,
inspect the general
condition of the tool. Check for:
• loose hardware
• misalignment or binding of moving parts
• damaged cord/electrical wiring
• cracked or broken parts
• any other condition that may
affect its safe operation.
2.
AFTER USE,
wipe external surfaces
of the tool with clean cloth.
3.
WARNING! If the supply cord of this
power tool is damaged, it must be replaced
only by a qualified service technician.
Checking and Calibrating the Fence
The Fence holds the workpiece in a fixed position
while the Table and/or the blade assembly
are adjusted in a miter or bevel angle.
To make accurate cuts, the Fence must be
perpendicular (at a 90º angle) to the Saw Blade.
1. Before beginning work, make a test cut on
scrap material with the Table set at 90º.
2. Check the cut with an accurate square.
You can also reverse the two pieces, hold
the cut ends together, and hold a good
straight edge along the side of the pieces.
3. If either test reveals that the cut is not a true 90º
angle, adjust the Fence before beginning work.
If Fence needs adjustment:
1. First unplug the tool.
2. Lower the blade assembly and lock it in
place using the Head Lockdown Pin.
3. Lay a carpenter’s square on the Table with one
edge along the Blade and the other along the
Fence. Any inaccuracy should be visible.
NOTE:
The square must contact the surface of the
Blade, not the teeth, for an accurate reading.
4. The Fence is held in place with bolts at each
end. Loosen the bolts slightly, and gently tap the
Fence into position using a soft mallet. Retighten
the bolts and make another test cut. Repeat the
process until the Fence is adjusted accurately.
5. Once the Fence is accurately adjusted,
tighten the bolts firmly in place. Recheck
one last time, then proceed to work.