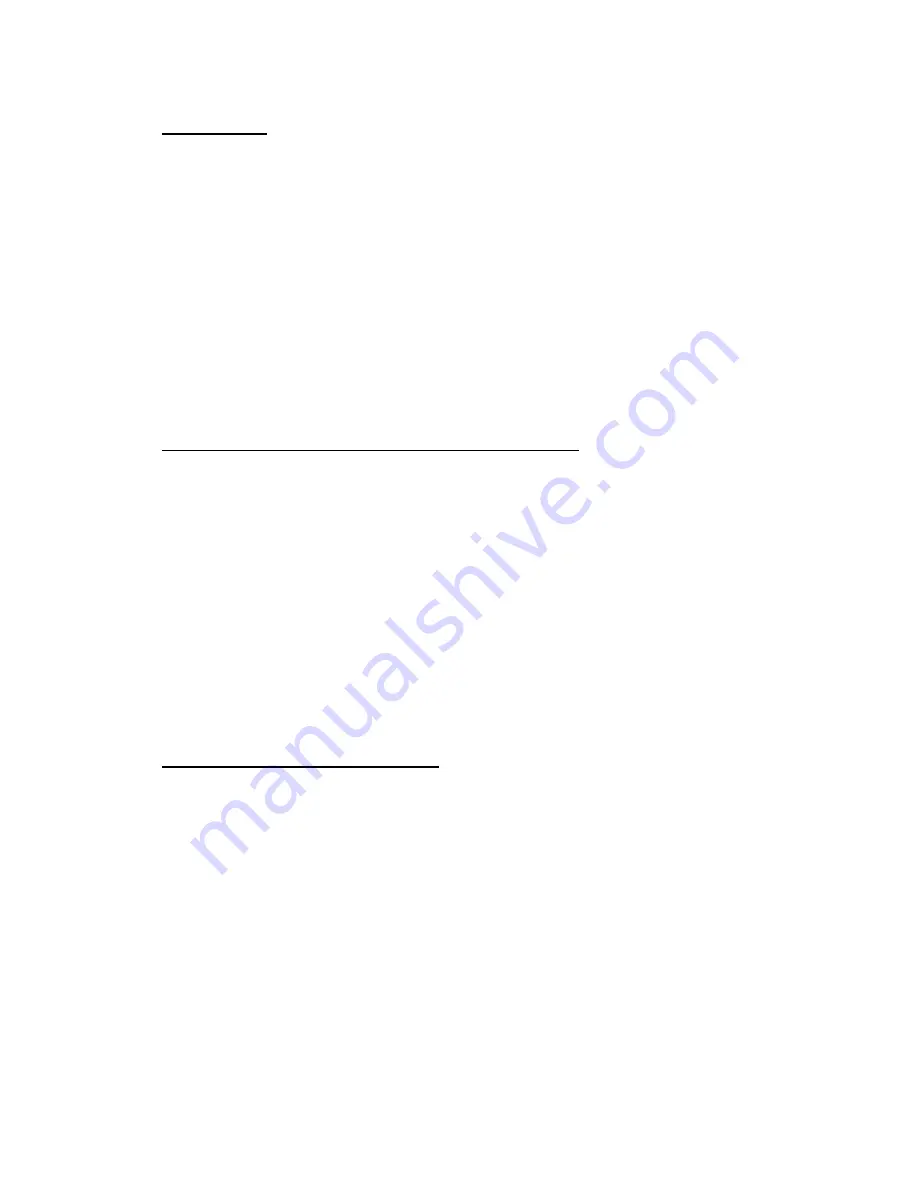
Chemtrac Systems, Inc.
Page 42
4.2
FUNDAMENTAL STREAMING CURRENT KNOWLEDGE
Introduction
It will take several weeks or maybe even a few months for an operator who has
come to rely on Jar test, eye-balling, turbidity readings, or any other method for
determining coagulant dosage to become comfortable using the monitor as a
tool for controlling coagulant feed. Very few plants install an monitor and start
controlling in Automatic mode in the first few weeks. Monitoring the response
and repeatability of the monitor through several different turbidity excursions,
and comparing process results obtained by controlling dosage to maintain a
streaming current setpoint against the results of previous methods used to
determine dosage changes is the only way to prove the reliability of the
instrument and gain the confidence needed to realize the full potential of the
technology. The operator will soon realize that the time consuming jar testing
procedure is no longer where his comfort lies. The information provided by the
monitor is equivalent to a 5 second jar test once the operator understands how
to interpret the reading.
The Importance Of Trending And Manual Control
It is suggested to hook up a chart recorder, or connect the monitor to SCADA, so
that the response and trend of the monitor can be monitored and compared to
turbidity readings, flow rates, and coagulant dosage adjustments. The
information derived from comparing the streaming current value to these other
parameters will assist the operator in understanding how the monitor responds to
changing conditions. During the first few weeks of operation, the monitor should
be used in Manual mode and all the operators should become familiar with how
to interpret the monitor reading. If the reading moves in the negative direction
from the setpoint as a result of an increase in turbidity, the operator should
manually increase the dosage to re-establish the setpoint and feel free to run a
Jar test to compare the results with. Following this procedure and closely
reviewing the monitor trends and responses will speed up the process of the
operators becoming comfortable with using the monitor to determine or
automatically control the coagulant dosage.
Setpoint – Why Does It Change?
It is important for the operator to understand that the ideal monitor setpoint can
occasionally change due to changes in water chemistry and wear on the probe
and piston assemblies. For example, a WTP may find that under the exact same
turbidity conditions a setpoint of 150 works great in the summer, but that a
setpoint of 50 works best in the fall. Unfortunately, there is no calibration
technique that can be used to correct for the monitor’s response to seasonal,
chemistry changes. This is the reason the monitor is considered a relative
reading. The dominating cause for the setpoint changing is due to seasonal
water chemistry changes (e.g. changes in PH or Color / Organics). Seasonal
additions of chemicals such as Potassium Permanganate or Powder Activated
Carbon can also have an effect on the monitor’s setpoint. Extreme changes in
turbidity can result in a significant enough change in chemistry that it may effects
the setpoint. Because the monitor’s setpoint can change, occasional
verifications of the setpoint need to be made. If Jar testing or operator
experience show that the setpoint currently being used may no longer be ideal,
simply readjust the chemical feed manually to re-optimize the process and
establish the new stabilized reading as the new ideal setpoint. These