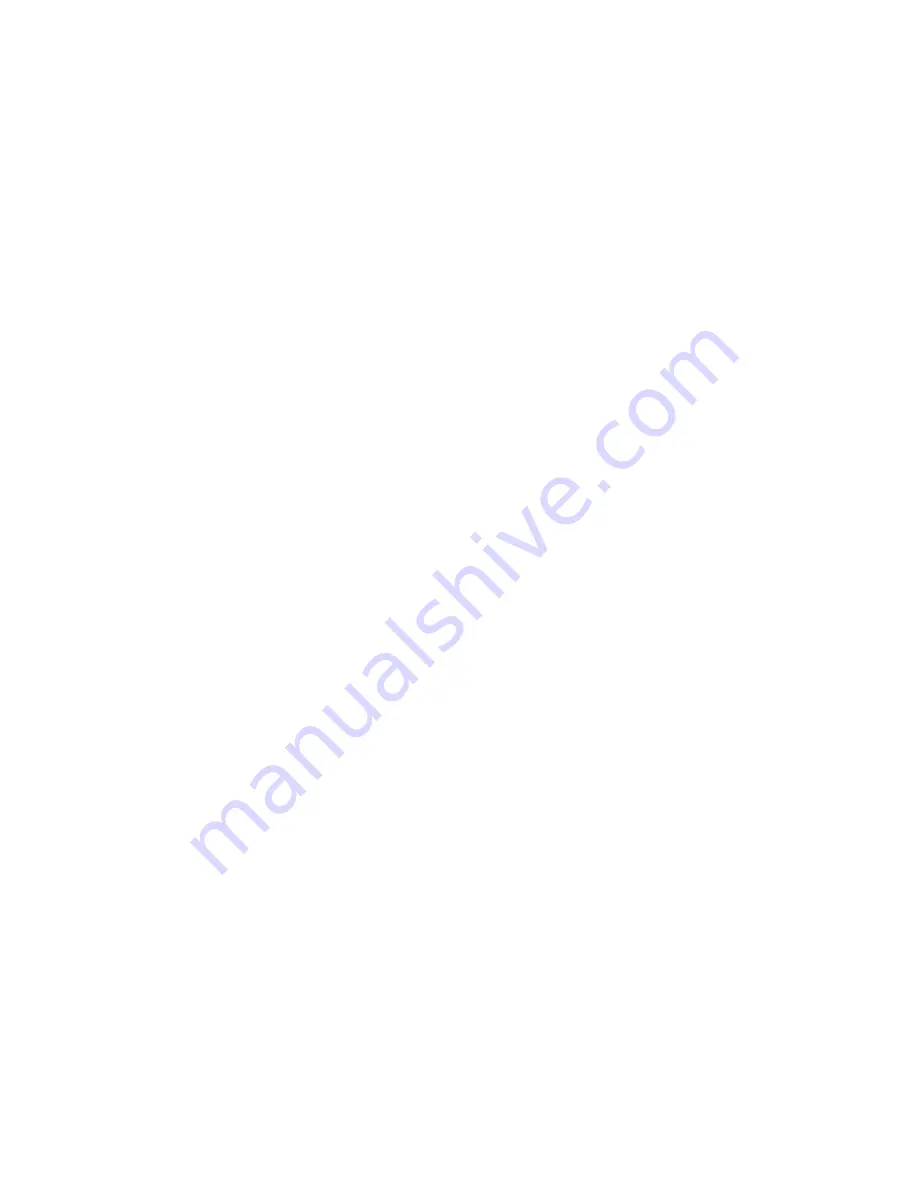
Chemtrac Systems, Inc.
Page 34
determine the best ideal alarm value. The HI Alarm value should be set above the
setpoint value and at a point where testing shows an unacceptable amount of overfeed.
After verifying proper response, the next step should be to optimize the process to
establish a SCV setpoint. The SCV setpoint can then be zero’d, or offset, so that the
setpoint will be adjusted to a reading of zero (0). This is done by entering the Setup
menu and changing the Offset mode to “IN”. Offsetting the SCV is not necessary for
normal monitor operation as it is only provided so that an easier reference of zero can
be used for monitoring changes in the process. For example, if the true SCV setpoint
reading was –150, and the user offset that reading to equal zero (0), if chemical dosage
was decreased the reading may go from 0 to –50. If the reading had not been zero’d,
then the true SCV would have gone from –150 to –200 (a –50 unit change). Once the
setpoint has been zero’d, it is easier to determine whether chemical is being under or
overdosed since going negative (anionic) from 0 would be an under-dose and going
positive (cationic) would be an overdose. A setpoint of zero (0) is also easier for
multiple operators (night and day shift) to remember. Since the setpoint will change
seasonally, adjusting the setpoint so that it equals zero (0) helps to avoid confusion.
A common mistake made with the monitor’s offset function is that it has been used to re-
zero the reading as it drifts from the previously offset reading of zero. Once the process
has been optimized and the Streaming Current Value has been zero’d at that point, it is
no longer necessary or correct to re-zero the reading. If the reading changes from the
setpoint of zero (or the true SCV setpoint if the offset is out), the chemical dosage
should be adjusted to bring the reading back to the setpoint and not the offset function.
Eventually, a new setpoint might need to be established due to seasonal changes or
large excursions in turbidity, but under normal conditions, the setpoint should not be
changed on a daily or even weekly basis. It is recommended to use the monitor for a
few weeks in the Offset Out mode to become familiar with the operation and response
of the unit.
3.5
TREATMENT OPTIMIZATION PROCEDURE
The treatment optimization process should be done slowly and stepwise. Assuming that
the plant is producing acceptable water with present chemical dosages, trim
approximately 10%, wait for the reading to stabilize, and record the reading as the
setpoint. You may need to change GAIN setting to increase magnitude of response. If
the settled and finished water quality is still acceptable at the reduced dosages, trim
another increment, wait for the reading to stabilize, and record the reading as the new
setpoint. Continue this process, being sure to wait long enough each time to see the full
effect of the chemical feed changes on the process (i.e. settled water turbidity,
appearance of floc). In between these dosage changes it will be necessary to maintain
the setpoint. Failure to maintain the setpoint while trying to reach a lower dosage level
could result in under dosing the chemical if turbidity starts to increase. By maintaining
the setpoint, the chemical dosage is kept in check with process changes (i.e. turbidity,
flow rates).
If the Offset function is being used, re-zero the monitor reading as described in section
3.3 after each reduction in chemical feed. If a cationic coagulant is being used, the
streaming current value will become more negative with each reduction in dosage. The
"optimum setpoint" is obtained when a minimum dosage of coagulant is being fed and
produces desired results for the particular treatment process. This setpoint will remain
very close to the same reading even when raw water turbidities increase or decrease.
Simply adjust the coagulant dosage to maintain this setpoint reading on the monitor.