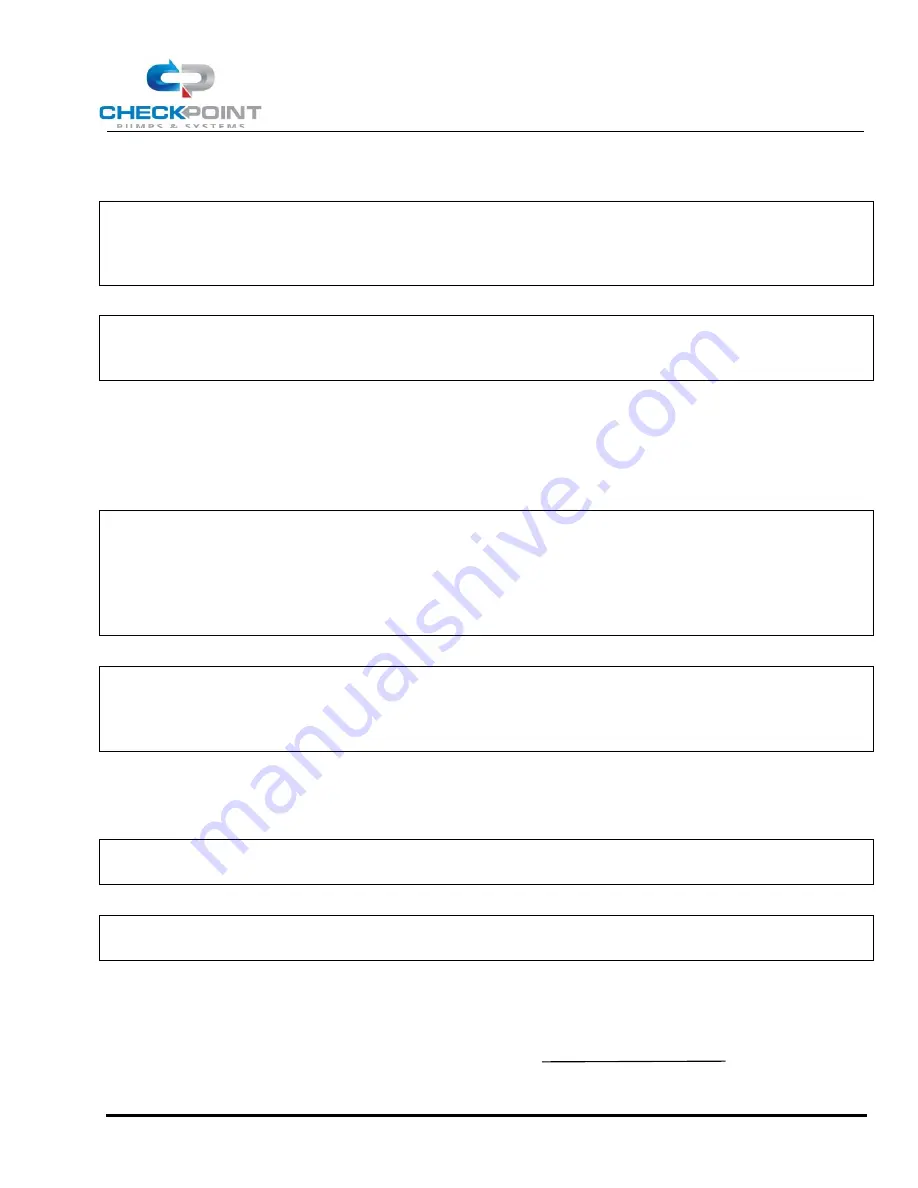
Series GX15 Pneumatic Chemical Injection Pump
Operating Manual
CP-MAN-PRD-GX15
REV06
EFF. DATE 07/23/2019
Page 6 of 12
1.2.4
Open the process block valve (shown as number 7 in Fig 1), allowing the process pressure to reach the
chemical head or in-line check valve. Observe & correct any leakage.
CAUTION:
The Series GX15 chemical head is rated for a maximum working pressure of 6,500 PSIG (448
BARG). Checkpoint recommends always installing a pressure relief valve between the discharge
check and the process flow to prevent catastrophic failure of process equipment or bodily
harm. Checkpoint is not responsible for any damage caused by over-pressurization.
NOTE:
Always open the process block valve prior to operating the pump. Operating the pump with a closed
process block valve may generate enough pressure to rupture the discharge line, damage process
equipment and the chemical head. Improper procedures may reduce the life of your CheckPoint pump.
1.3
Connecting the Supply Gas
1.3.1
Gas supply to the pump should be clean compressed air or natural gas at 20 PSIG (1.38 BARG) minimum, 150
PSIG (10.34 BARG) maximum. Supply gas should be free of abrasive dust, sand or other grit that could abrade the
motor seals. Checkpoint recommends installation of a pressure regulator in the supply line to ensure a constant
supply pressure and within limits.
NOTE:
It is not necessary to remove most liquids from the supply gas such as distillate carryovers. The pump
will not stall no matter how much liquid reaches the air/gas inlet. However, certain chemicals, including
but not limited to methanol and corrosion inhibitor may attack the seals in the pumps motor end and
should be removed prior to reaching the pump air/gas inlet. Alternatively, if damaging chemicals or
other unusual liquids will be present in the supply gas, CheckPoint may be able to supply other motor
seal materials.
NOTE:
Always use a gas pressure regulator if the possibility of supply pressure in excess of 150 PSIG (10.3
BARG) exists. Allowing gas pressures above 150 PSIG to enter the air/gas inlet may result in damage to
the motor seals and will produce excessive discharge pressures capable of rupturing chemical
discharge tubing.
1.3.2
Liquids may be used as a driver fluid but pump speed will vary widely with the liquid viscosity. Call CheckPoint
for performance data for the liquid you intend to use.
1.3.3
Ensure the supply gas line is clean and free of all foreign matter and debris.
NOTE:
Take care to prevent debris in the supply gas line from entering the housing where it could accelerate
seal wear and damage the main switching valve components.
NOTE:
In situations where sand, dirt, and other particulate matter may be carried in with the supply gas, a
chemical filter or a gas scrubber is recommended.
1.3.4
Connect the supply gas line to the 1/4" NPT female connection on the housing. To ensure positive injection,
the supply gas pressure should be a minimum of 20 PSIG (1.38 BARG) and a maximum of 150 PSIG (10.34 BARG),
set according to the following formula:
MINIMUM REQUIRED GAS INLET PRESSURE
=
[DISCHARGE PRESSURE]
X 1.3
[AMPLIFICATION RATIO]