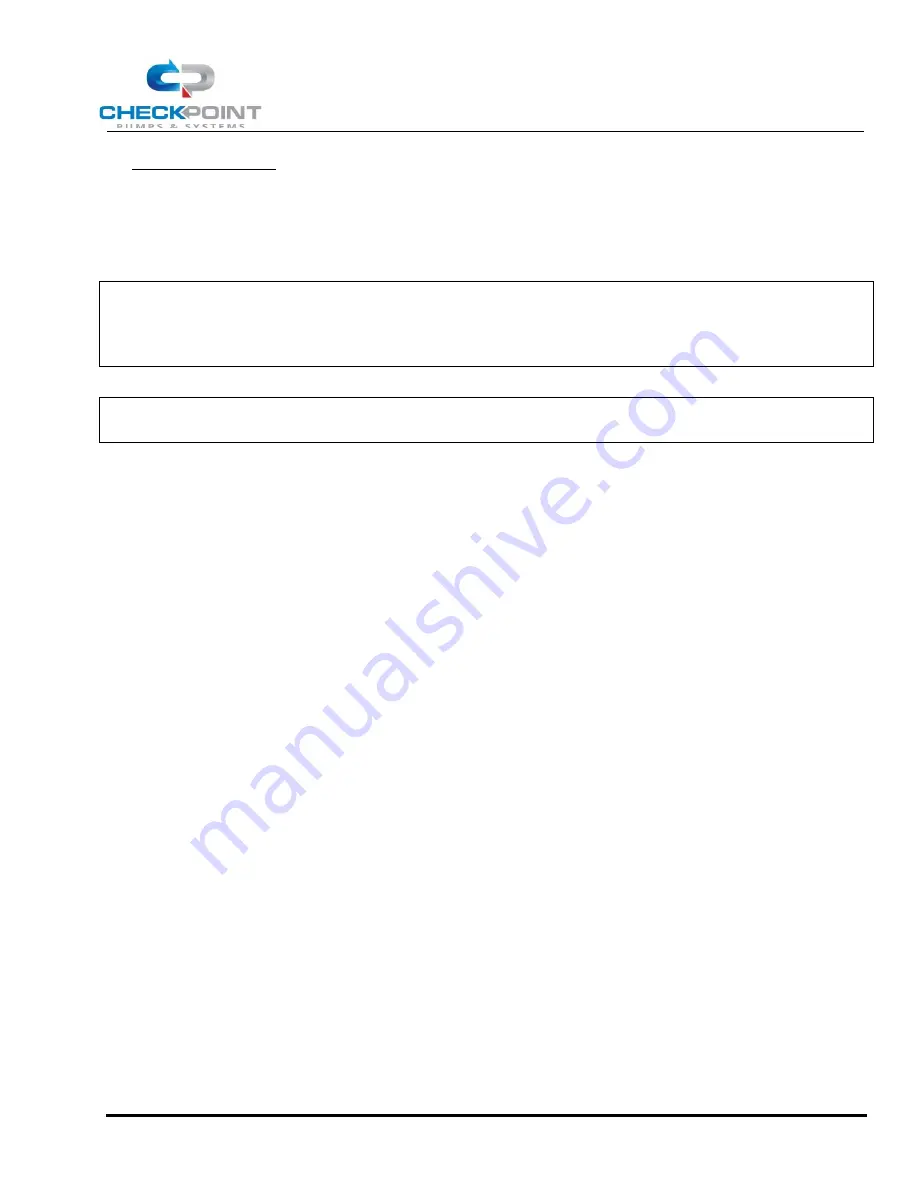
Series GX15 Pneumatic Chemical Injection Pump
Operating Manual
CP-MAN-PRD-GX15
REV06
EFF. DATE 07/23/2019
Page 11 of 12
5.
TROUBLESHOOTING
5.1
Pump runs, but chemical does not discharge at the correct rate
5.1.1
Suction check valve may be clogged with debris
To flush suction check, allow pump to cycle at maximum
rate for at least 60 seconds. If no improvement is noted, remove the suction check valve from pump head. Blow the
check out with air or water pressure. If the first attempts are unsuccessful, a check rebuild could be necessary.
NOTE:
CheckPoint FailSafe
TM
check valves do not need replacement when they do not check properly. A
simple rebuild kit is available to replace the O-rings, which corrects all but the most severe check
problems. Corrosion of the valve seat, retainer or poppet indicates an incorrect check valve material.
Please contact CheckPoint to request chemical compatibility information.
NOTE:
Always replace Teflon
TM
tape or other appropriate thread sealant on check valve threads during
reinstallation to avoid chemical leakage or the introduction of air to the chemical head.
5.1.2
Pump may have lost prime/become “air locked”
Check to ensure that there are no leaks in any process
lines, particularly upstream of the pump within the chemical suction lines. If air is introduced through the suction
side, the pump may lose prime. Read Section 2.1 and its subparagraphs carefully for details. A common source of
air in the supply is the block valve ahead of the suction check. Check this valve to make sure the stem packing is
tight and that the materials of construction are compatible with the chemical being pumped. Also, check that the
pump’s
packing is not leaking. Finally, on pumps supplying chemical into gas lines, it is possible that the discharge
port may be leaking.
A leaky discharge port may allow gas under pressure to “back into” the chemical head.
5.1.3
Check valves may have been re-located away from the chemical head of the pump
The checks must stay
directly attached to the head in order to facilitate chemical movement.
5.1.4
Chemical may be obstructed from entering the pump
Plumbing upstream of the chemical head may have
blockage preventing chemical from getting to the suction check valve. A common example is an in-line chemical
filter becoming clogged with debris. Solution - clean out suction plumbing and clean or replace chemical filter.
5.1.5
Chemical supply line size or configuration may cause NPSHa to drop below NPSHr.
5.1.6
Calibration gauge may read incorrectly due to clogged air vent
If the calibration gauge is not reading
correctly, it may appear chemical is not getting into the process. Check for an obstruction in the gauge or in the air
vent atop the gauge.
5.2
Pump does not stroke
5.2.1
Pump speed control valve may be closed
Open the speed control valve (counterclockwise) until the pump
actuates. Then set desired stroke rate as described in
Section 2.2
5.2.2
Air/Gas supply pressure may be too low to overcome the chemical discharge pressure
Open the chemical
head bleed port. If the pump starts stroking, ensure the air/gas supply pressure is sufficient to overcome the
chemical discharge pressure. Possible cause could be a faulty pressure gauge or regulator. See
Section 1.3.4
on page
6 to determine minimum supply pressure.
5.2.3
Gas recovery pressure is too high relative to gas supply pressure
The pump requires a minimum of 30
PSIG differential pressure. Refer to
Section 1.3.6
on page 6 to determine the appropriate recovery pressure.
5.2.4
Pump switching valve may be clogged or "gummed-up" with paraffin or trash
Disconnect air/gas supply,
then introduce any type of oil or solvent into the pump air/gas inlet. Re-connect air/gas supply and open speed