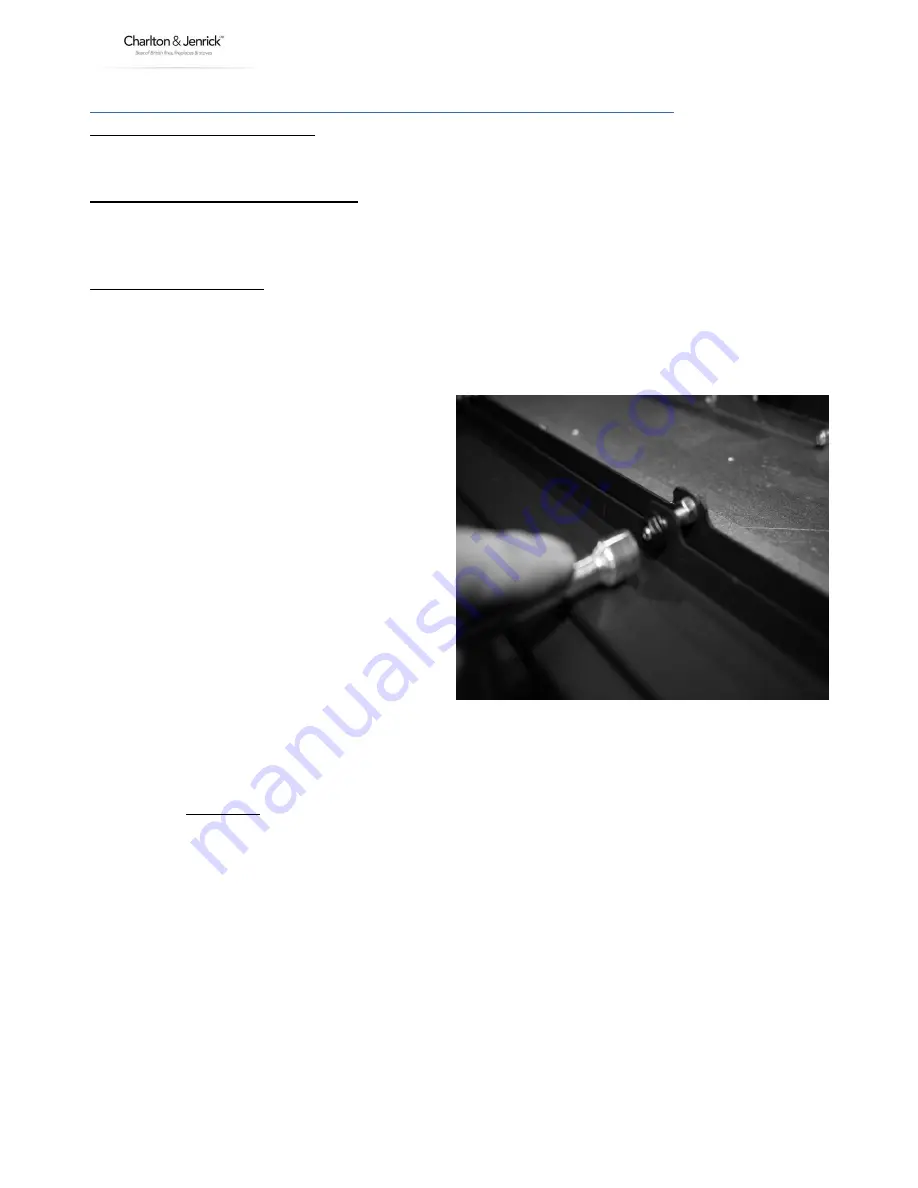
10
LT6541 (ISS 11)
SECTION FOUR Cleaning & Laying the fuel bed (users instructions)
CLEANING: DECORATIVE FASCIA
Fascia assembly can be wiped with a soft, clean, dry, cloth only.
CLEANING: BLACK PAINTED SURFACES
These surfaces should be dusted regularly and any marks removed with a soft cloth.
Abrasive or chemical cleaner should never be used.
CLEANING: GLASS PANEL
From time to time it may be necessary to clean the glass panel.
We recommend you use a Ceramic Hob Cleaner (brands such as HOB BRITE and VITRO CLEN have been found to be
acceptable) these are available from most leading Supermarkets.
Remove the glass panel as follows:
Undo the 3 screws that secure the heat
deflector and remove
Carefully lift off the outer fascia held in place by
magnets.
Remove the 4 nuts at the bottom securing the
glass assembly.
Remove the Top 5 castle nuts on Glass Clamp,
and slide the Glass Frame & Retaining Bracket
completely off and disengage both parts
Lay the glass panel down on a flat working
surface on top of an old opened newspaper
with the side to be cleaned uppermost.
Follow the Instructions on the Hob Cleaner Bottle.
On stubborn stains (where the appliance has been used for a long period without glass panel being cleaned), use a
new Brillo Pad well wetted with the Hob cleaner applied directly to it.
Ensure all the residues of the cleaner are removed with a damp cloth and the glass panel is completely dry before
fitting to the appliance.
Note: - If the loose shapes have not been placed correctly, causing the gas flame to contact the glass this may result
in glass staining that cannot be removed by cleaning.
Re-assemble in reverse order ensuring a tight seal against glass assembly.
Re-fit the fascia.
Summary of Contents for infinity 890 BF
Page 28: ...28 LT6541 ISS 11 ...
Page 29: ...www charltonandjenrick co uk 29 LT6541 ISS 11 ...