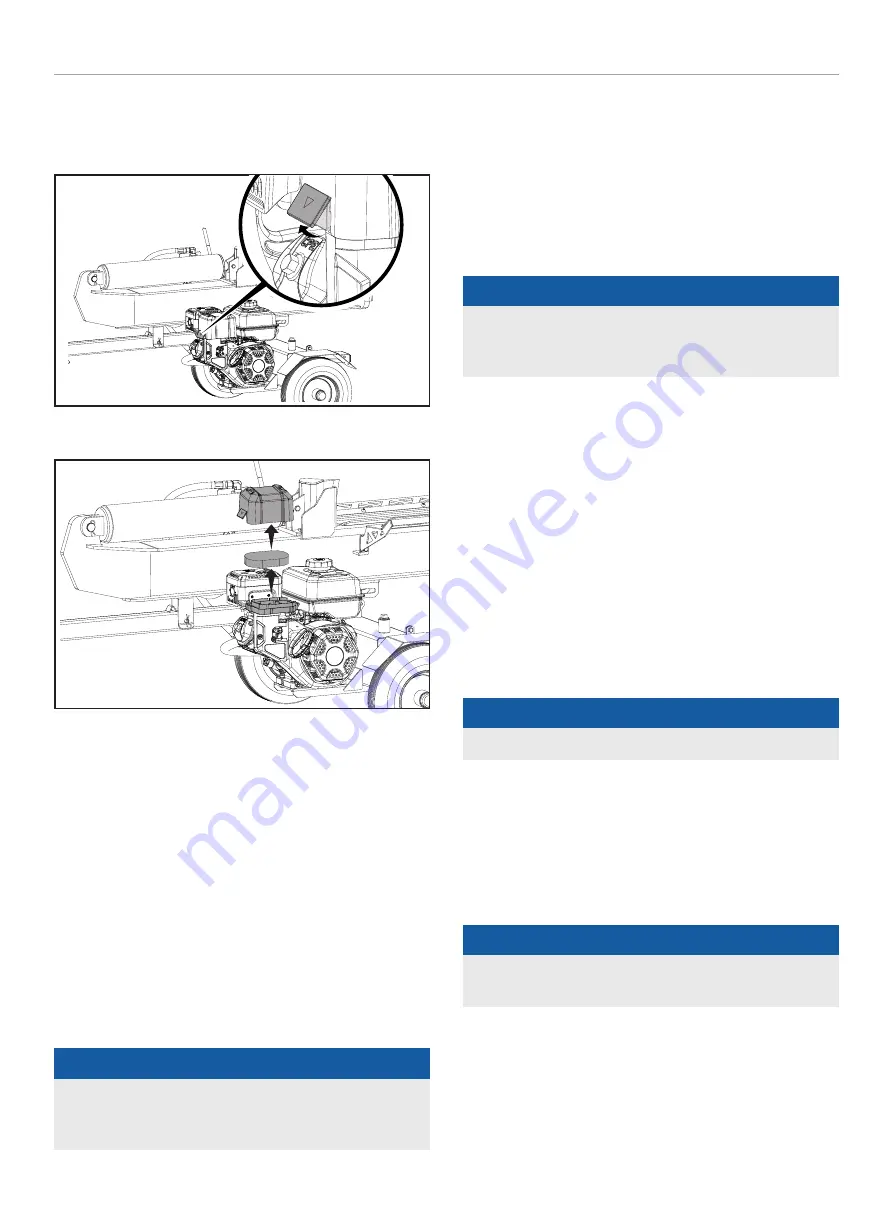
100326-1 - 25 TON FULL BEAM LOg SPLiTTER
MAiNTENANCE
26
Cleaning the Air Filter
1. Using your finger, pry the outer tab up slightly and lift the air
filter cover above the tab lock position.
2. Remove both air filter cover and air filter element.
3. Wash in liquid detergent and water. Squeeze thoroughly dry in
a clean cloth.
4. Saturate in clean engine oil.
5. Squeeze in a clean, absorbent cloth to remove all excess oil.
6. Place the filter in the assembly.
7. Reattach the air filter cover. Attach the side closest to the
gas tank then pivot down to close. Make sure air filter cover
snaps in place.
Changing the Hydraulic Oil
Always shut off the engine, disconnect the spark plug.
Change the hydraulic oil filter after the first 50 hours of use, then
every 100 hours or seasonally.
NOTiCE
When log splitters are not used for extended periods of time
and they are exposed to changing temperature conditions,
moisture through condensation can build up inside the tank.
1. Begin with the cylinder retracted and the engine fuel valve in
the “OFF” position.
2. Release any stored pressure by moving the valve lever
forward and backward several times.
3. Place a container under the hydraulic tank. Make sure
it is large enough to hold the contents of the tank.
See model specification section of this manual for hydraulic
oil capacities.
NOTiCE
The drain plug is sealed with Teflon
®
tape. Add 2-3 wraps of
new Teflon
®
tape as needed when replacing the drain plug to
prevent oil leak.
4. To drain the oil,
–
Place an oil drain container under the drain plug. Unscrew
(counter-clockwise) and remove the tank drain plug on
the bottom of the hydraulic tank. Allow oil to completely
drain from the tank into the container. Re-apply Teflon®
sealing tape to the drain plug threads, then reinsert and
turn (clockwise) in the tank drain plug. Tighten, but do not
over tighten.
–
Place an oil drain container under the external oil filter
(If your log splitter includes this feature). If not, skip to
step “C”. Unscrew (counter-clockwise) and remove the
external hydraulic oil filter and drain any oil in the filter
into the container. A strap or oil filter wrench may be
needed.
NOTiCE
Oil will drain from the filter and filter housing.
–
Locate an approved replacement filter.
–
Lubricate the gasket of the new filter with a thin film
of clean oil.
–
Install a new hydraulic oil filter (A). Screw the new
filter on clockwise. Tighten 3/4 - 1 turn after the
gasket makes contact.
NOTiCE
Install a new hydraulic oil filter each time the hydraulic oil is
changed (if your log splitter includes this feature).
–
Place an oil drain container under the large clear hose
that runs from the tank to the pump.
–
Loosen the hose clamp attached to the fitting on the
tank.
–
Disconnect hose from fitting and drain oil into the
container.