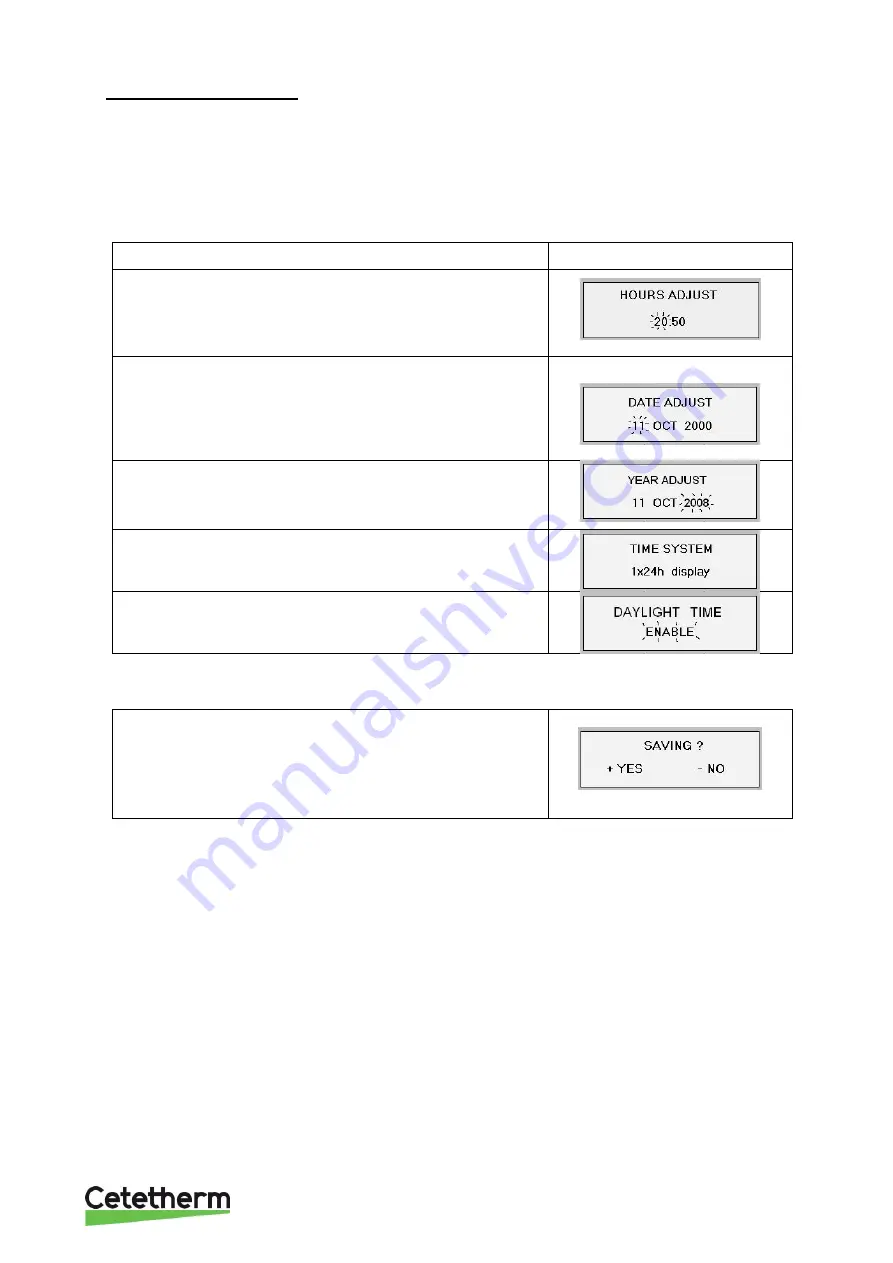
21
SET HOUR AND DATE
This menu allows you to set hour & date
Press:
white
to enter the menu.
white
to get to the next frame/setting,
white
to get to the previous frame/setting.
ACTION
DISPLAY
Set the hour and minutes
Press white
,
Press + or
– to adjust the hour,
Press white
,
Press + or
– to adjust the minutes,
Set the date and month
Press white
,
Press + or
– to adjust the day,
Press white
,
Press + or
– to adjust the month,
Press white
,
Set the year
Press + or
– to adjust the year,
Press white
,
Set the hour format
Press + or
– to adjust the hour format,
Press white
.
Set automatic wintertime/summertime change
Press + or
– to adjust,
Press white
.
SAVE MODIFICATIONS
At any time, you can interrupt the setting procedure and save
the changes by pressing the Validation key.
To save your modifications, Press + for YES and
– for NO.
ANY PARAMETER MODIFICATION SHOULD BE
VALIDATED THIS WAY