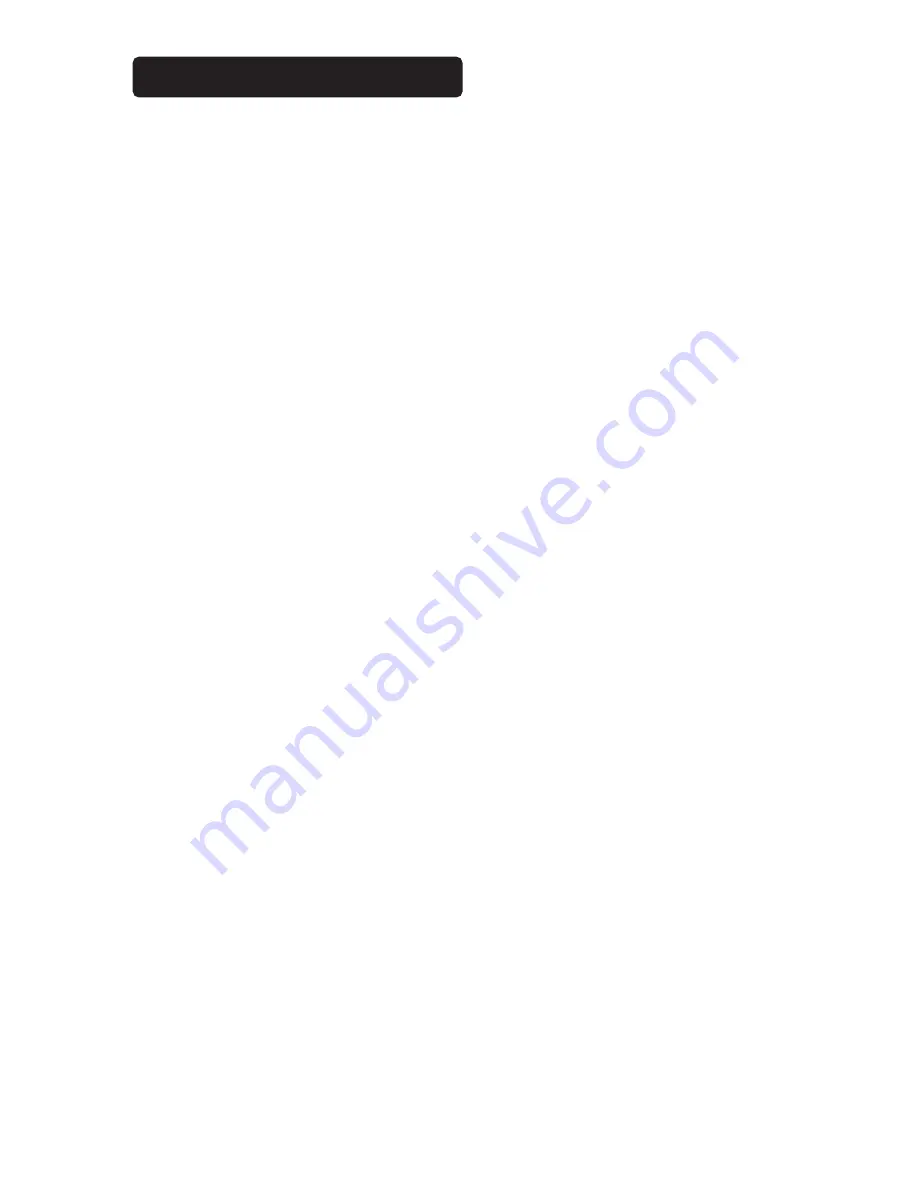
Health and Safety document No 635, “Electricity at
Work Regulations”.
Detailed recommendations are contained in the
following British Standard Codes of Practice.
Codes of Practice.
BS.6798 Installation of gas fired hot water boilers of
rated input not exceeding 70kW.
BS.5440: Part1 and Part 2. Flues (for gas appli-
ances of rated input not exceeding 60kW).
BS 6891 Specification for installation of low pressure
gas pipework.
BS5482:1 Code of practice for domestic butane &
propane gas burning installations.
Building Regulations Part L1.
IMPORTANT
.
It is important that no external
control devices are directly connected to this appli-
ance - unless covered by these ‘Installation and
Servicing Instructions’ or otherwise recommended
by the manufacturer. If in doubt, please enquire.
Any direct connection of a control device not
recommended by the manufacturer could infringe
the Gas Safety (Installation & Use) Regulations, the
above regulations and the normal appliance war-
ranty.
Manufacturer’s notes must NOT be taken, in any
way, as overriding statutory obligations.
Location of Heater
The Heater MUST be installed on a flat and level
floor, capable of adequately supporting the weight of
the Heater and any ancillary equipment.
Provision is provided for the heater to be fixed to the
floor.
It is IP 44 Rated and can be installed out of doors in
a suitable position. In all cases the choice of position
should take into account the flue, the plume and the
condensate drainage.
IMPORTANT NOTICE.
If the Heater is to be fitted in a timber framed build-
ing it should be fitted in accordance with the British
Gas publication ‘Guide for Gas Installations in
Timber Frame Housing’, reference DM2. If in doubt,
advice must be sought from the Local Gas Region of
British Gas.
The Heater may be installed in any room or internal
space. Particular attention is drawn to the require-
ments of the current I.E.E Wiring regulations and, in
Scotland, the electrical provisions of the Building
Regulations applicable to Scotland with respect to
the installation of the boiler in a room or internal
space containing a bath or shower.
Where a room sealed appliance is installed in a
room containing a bath or shower then the appliance
and any electrical switch or appliance control,
utilising mains electricity should be so situated that it
Condensing Pool Heater
3
22/12/08
INTRODUCTION
These Instructions cover a range of direct, floor
mounted, gas fired, condensing pool heaters which
are room sealed and fan assisted. The flue system
available is concentric, left, right, rear, and vertical,
all up to 20 metres ‘FEL’. There is also an Outdoor
Top terminal for use where the Heater is installed
out of doors. The ignition system is fully automatic.
There are two models with different outputs - see
the
Technical Data on Inside Cover
for details.
Both can be installed in multiples to obtain a larger,
combined output.
The casing is of green and black polyester powder
coated mild steel. The Heaters use a high perform-
ance stainless steel heat exchanger and are suit-
able for connection to pools using chlorinated and
salt chorinated water provided the following levels of
chemicals are maintained.
pH
7.2 to 7.8
Total Alkalinity
80 to 140 ppm
Calcium Hardness
200 to 400 ppm
Salt maximum
30000 ppm
Free Chlorine
1 to 4 ppm
All chemicals must be introduced and completely
diluted into the pool water before being circulated
through the heater. Do not place chlorine tablets or
bromine sticks in the skimmer, high chemical
concentrations will result when the pump is not
running.
Chlorinators must feed downstream of the heater
and have an anti-siphoning device to prevent
chemical back-up into the heater when the pump is
shut off.
NOTE:
High chemical concentrates from feeders
and chlorinators that are out of adjustment will
cause corrosion to the heat exchanger in the
heaters. Such damage is not covered under the
warranty.
Gas Safety (Installation and Use)
Regulations, (as amended).
It is the law that all gas appliances are installed by a
competent person (e.g. a CORGI registered opera-
tive) in accordance with the above Regulations.
Failure to install appliances correctly could lead to
prosecution.
It is in your own interest, and that of safety, to
ensure that the law is complied with. The installation
of the Heater MUST also be in accordance with the
current I.E.E.. Wiring Regulations, the Local Build-
ing Regulations, Building Standards (Scotland), the
Bye Laws of the Local Water Undertaking, any
relevant requirements of the Local Authority, and
Summary of Contents for MB35S
Page 24: ...Fig 11 0 Condensing Pool Heater 21 22 12 08 Schematic Wiring ...
Page 33: ...Condensing Pool Heater 30 22 12 08 This page has been intentionally left blank ...
Page 34: ...Condensing Pool Heater 31 22 12 08 This page has been intentionally left blank ...
Page 36: ...Station Lane Industrial Estate Witney Oxon Tel 01993 778855 Fax 01993 703407 22 12 08 ...