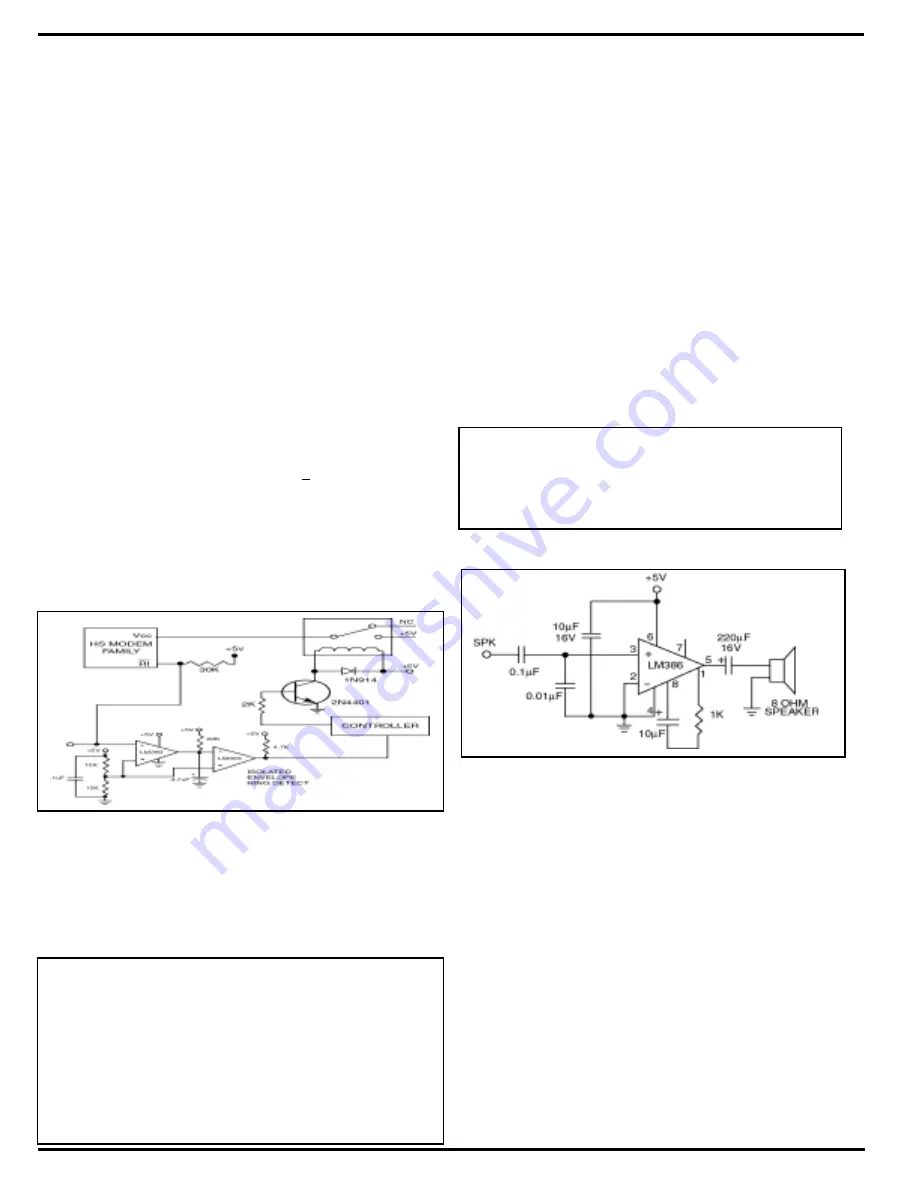
© 2000 Cermetek Microelectronics, Inc. Page 4
Document No. 607-0017 Rev. B (06/00)
Table 1. Data Formats Recognized by iModem® Family.
Table 2. iModem® Auto Configuration Based on DTE
Configuration.
Data Length
No. of
Character Length
Parity
(No. of Bits)
Stop Bits
(No. of Bits)
None
7
2
10
Odd
7
1
10
Even
7
1
10
None
8
1
10
Odd
8
1
11*
Even
8
1
11*
*11 bit characters are sensed, but the parity bits are stripped off dur-
ing data transmission in Normal and Error Correction modes.
DTE Configuration
iModem® Configuration
7 mark
7 none
7 space
8 none
8 mark
8 none
8 space
8 even.
Figure 4. Speaker Control Circuit.
Referring to Figure 5, use the variable resistor (POT) to set required
speaker volume.
To maintain FCC compliance, frequencies transmitted while in
voice mode should be between 300Hz and 3000Hz.
When voice and data are both being used, and the RXA and TXA
pins are active, it is typical for voice communication to precede data
communication. In this case, the following commands should be
used to configure the iModem® to allow for full utilization of the
Voice/Tone injection feature.
Voice/Tone Injection Port.
T
h
e iModem® Family provides pin T1 to allow the user to share the
PSTN line interface associated with the iModem® for voice and
DTMF applications. Figure 5 contains a schematic indicating one
possible configuration for voice/tone utilization.
All iModem® products are
designed with pin T1 coupled directly to
the internal DAA. When using the iModem® in data mode, T1
should float and be disconnected from any potential signal because
any signal on T1 during data operation will affect the iModem®
output. If T1 is being asserted from another application, use a relay
or zero impedance switch to disconnect T1 when in data mode.
Automatic Speed/Format Sensing.
The iModem® supports both Command and Data modes of opera-
tion.
The iModem® can automatically determine the speed and format of
the data sent from the DTE over the serial interface; and can sense
the following broad range of speeds:
Figure 3. Zero Power Operation
The iModem® Family requires a 5V +5% supply. It is
recommended that bypass capacitors be placed on the power
supply as close to the iModem® supply input pins as practical. It is
recommended that a 10
m
F or greater tantalum capacitor in parallel
with a 0.1
m
F ceramic capacitor be used. The user must also
provide shielding from nearby sources of EMI, such as relays,
motors and other power supplies.
The iModem® is trained to a selected speed with an AT [CR] training
sequence. Thus, the DTE to modem serial interface speed can be
set independent of the DCE or line carrier connecting speed (with
minor restrictions, see the AT + MS command). This allows greater
flexibility when selecting DCE line carrier modulation speed thereby
affording the user with optimum data throughput performance. To
maximize effective modem data throughput speed, the DTE to mo-
dem serial interface speed should be set to the highest speed avail-
able without invoking the use of the iModem® built-in flow control.
Although flow control facilitates communication with higher speed
modes by the DTE, use of flow control causes an overall throughput
data rate penalty.
Power Supply.
The iModem® module is a complex set of sensitive sub-
systems. During the course of normal operation, the iModem®
decodes analog signals from the telephone line that are in
millivolt range. Steps must be taken by the user to guarantees
that power supply noise on all supply lines, including ground,
does not exceed 25 mV peak to peak. If necessary, use
dedicated power and ground planes. Failure to provide such
operating conditions could cause the iModem® to malfunction
or to function erratically.
The data formats in Table 1 are recognized by the iModem® family
of products.
The iModem® can sense data with mark or space parity and config-
ures itself as described in Table 2.
Referring to Figure 2, the controller activates the relay switch,
supplying power (+5V) to the iModem®. In this configuration, the
ring signal is used to “wake up” the iModem® when the iModem® is
in the power down state.
The pins of the iModem® will be in an undefined state when power
is switched off. This must be taken into consideration to assure that
no unwanted signals are presented to the iModem® during power
down.
Zero Power Mode.
If an application calls for zero power during standby periods, the
power may be switched off using external circuitry and then
reapplied when the iModem®’s RI pin becomes active. The
iModem® can thus be powered down to zero.
300, 600, 1200, 2400, 4800, 7200, 9600, 12000, 14400, 16800,
19200, 21600, 24000, 26400, 28800, 38400, 57600, 115200 and
230400bps.