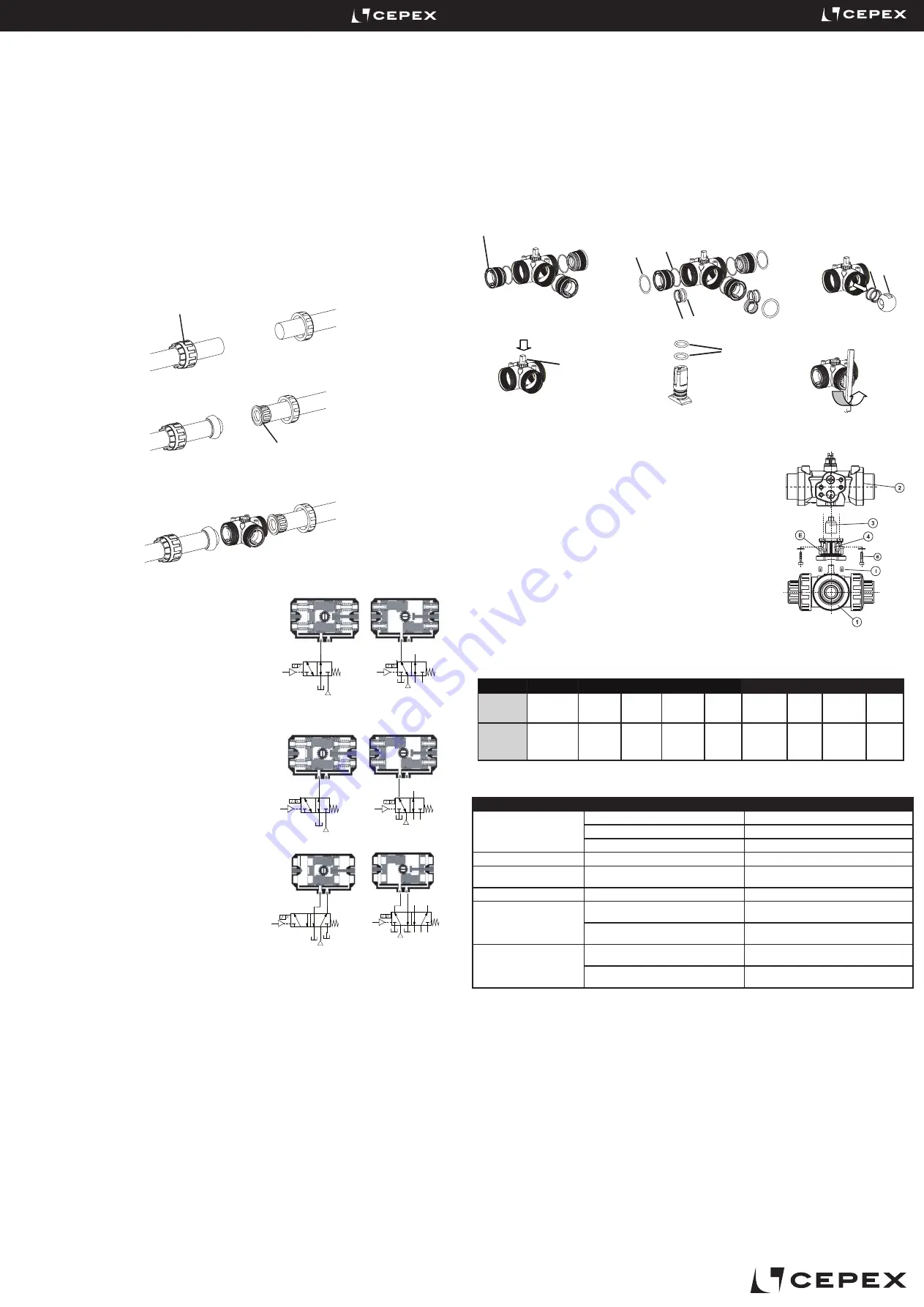
5.
INSTALLATION AND COMMISSIONING
Before starting the installation process, check that all the parts needed for the valve assembly are there, and that the materials, connection
type and nominal pressure are suitable for the installation.
For solvent or welded connections, ensure also that the parts to be connected are of the same material and that the correct solvent or
welding tools are used.
To install the valve, follow best installation practice recommendations provided on the Cepex website, paying specific attention to thermal
expansion and pipe alignment.
When filling the pipes with liquid, check that all the air has been purged from the system and that the initial pressure does not exceed the
nominal pressure of the valve, or of the system element with the lowest nominal pressure rating.
Install the valve pointing in the direction of flow marked on the body of the valve (downstream).
Install the valve once the sockets are solvent-bonded and dry, to avoid problems with the adhesive (entry of the latter into the valve).
7.
OPERATION AND MAINTENANCE INSTRUCTIONS
9.
SPARE PARTS
10.
TROUBLESHOOTING
T 9.1
The valve is supplied assembled from the factory and the following steps should be followed for its installation:
1. Check that the diameter of the pipe corresponds to the inside of the end connector (if it is a solvent socket).
2. Adjust the valve to the installation leaving the union nut (3) Fig. 6 on the pipe before gluing the end connector (5) Fig. 7.
3. Leave an exact distance between end connectors (see Fig. 8), so that the body of the valve can be easily introduced, preventing it from
being strained by both ends of the piping.
4. Solvent sockets (PVC-U / PVC-C / ABS) are made by cleaning the areas to be joined with a suitable solvent and then adding adhesive. It not
recommended that pressure be applied until 24 hours after gluing.
The body of the end connectors should be separated during the solvent operation, to avoid that the adhesive damages the valve’s internal
parts.
5. PTFE tape is placed on the male threads of the threaded unions: “it is very important not to use an excessive amount as when it is put
together it could cause the breakage of the female housing”.
The welded unions (PE / PP-H / PVDF) are made taking into account the instructions of the welding tool used.
This range of valves allows the valve to be fixed to a base using threaded inserts at the bottom.
When using the inserts, take note of the dimensions of the screws.
3
5
Fig. 6
Fig. 7
Fig. 8
Fig. 12
Fig. 14
15
10
11 10
13
2
10
Fig. 13
1
9
Fig. 16
Fig. 17
Fig. 19
ENGLISH
3WAY PNEUMATIC BALL VALVE
ENGLISH
3WAY PNEUMATIC BALL VALVE
Fig. 18
8.
MOUNT AND DISMANTLE THE ACTUATOR
If the actuator or the valve needs to be replaced, proceed as follows:
1. Move the ball valve to the closed position.
2. Depressurise and drain the plant or the plant component.
3. Depressurise the control medium.
4. Remove the control medium line(s) from the actuator.
5. Remove the screws (E, Fig. 19).
6. Separate the pneumatic actuator (2) with the mounting clamp (4) from the bare
shaft valve (Fig. 19).
7. Remove the screws (B) in order to dismantle the actuator from the mounting
clamp.
8. In the case that the actuator needs to be replaced by a handle, also remove the
coupling bush (3, Fig.19).
In order to assemble a new actuator or a new valve, proceed in opposite direction to
the description above.
FAULT
POSSIBLE CAUSE
FAULT CLEARANCE
Leak in the valve body.
Wear of the body o’ring.
Change the o’ring.
Loosening of the seal carrier.
Adjust the seal carrier.
Presence of solids or strange elements.
Remove the valve and replace damaged parts.
Leak in the valve shaft
Wear of the shaft o’rings.
Change the o’rings.
The torque is too strong or the valve
is blocked.
The seal carrier is over-tight
Adjust the seal carrier.
The valve does not open or close.
Lack of pressured air.
Check air supply to actuator
The valve does not close completely.
The actuator stroke is not properly adjusted to the
valve.
Check adjustment limits according to the actuator manual.
The torque of the valve has increased above the
calculated value.
Check the valve: obstructions in the disc or malfunction
of the valve.
The valve does not change the
position.
The solenoid valve does not operate properly due to
the use of unfiltered air.
Add filtration equipment to the air supply input.
The solenoid does not work properly due to impurities
or oxidation by a corrosive environment.
Change the solenoid valve and ask the technical
department about the most appropriate solenoid valve.
SPRING RETURN PNEUMATIC ACTUATOR
DOUBLE ACTING PNEUMATIC ACTUATOR
DN
VALVE
Ch-Air
Mounting
kit
Ch-Air
Actuator
Prisma
Mounting
kit
Prisma
Actuator
Ch-Air
Mounting
kit
Ch-Air
Actuator
Prisma
Mounting
kit
Prisma
Actuator
DN40
SEE TECHNICAL
CATALOG TO
KNOW THE
SPECIFIC CODE
30844
30718
30632
30728
30843
30711
30631
30723
6.
OPERATION OF THE ACTUATOR
6.1 SPRING RETURN NORMALLY CLOSED VALVE (Fig. 9)
The valve is closed without an air supply. When the actuator is supplied with
pressurized air, the valve opens. If the supply of the pressurized air is closed and
the air can escape, the valve will be closed because of the actuator’s internal
springs.
A 3/2 solenoid valve or 5/2 solenoid valve is required to carry out the action. In
the case a normally closed monostable solenoid valve is installed, the electrical
signal should be maintained during the time that the valve needs to be kept open.
In the case of a spring return actuator, Cepex will normally serve the closed valve
as standard.
6.2 SPRING RETURN NORMALLY OPEN VALVE (Fig. 10)
The valve is opened without an air supply. When the actuator is supplied with
pressurized air, the valve closes. If the supply of the pressurized air is closed and the
air can escape, the valve will be opened because of the actuator’s internal springs.
A 3/2 solenoid valve or 5/2 solenoid valve is required to carry out the action. In the
case a normally closed monostable solenoid valve is installed, the electrical signal
should be maintained during the time that the valve needs to be kept closed.
6.3 DOUBLE ACTING VALVE (Fig.11)
The valve has no defined fail safe position. The valve is opened and closed by
applying air pressure to the corresponding control connections.
A 5/2 solenoid valve is required to carry out the action. In the case a normally
closed monostable solenoid valve is installed, the electrical signal should be
maintained during the time that the valve needs to be kept open (according to
the drawing).
2
3
1
10
OPEN VALVE
2
3
1
10
CLOSED VALVE
2
3
1
10
CLOSED VALVE
2
3
1
10
OPEN VALVE
Fig. 9
Fig. 10
Fig. 11
6.4 LIMIT SWITCH BOX
To electrically confirm the position of the valve, a limit switch box can be
mounted to the actuator according to NAMUR specification.
IP67 Protection. Temperature range: -20ºC to 80ºC.
Limit switch boxes are available made from plastic and aluminium.
Electromechanical SPDT switches are used as standard.
See the specific manual and the electrical diagram inside the box.
14
4
2
3
1
5
14
4
2
3
1
5
CLOSED VALVE
OPEN VALVE
6.5 SOLENOID VALVE
Different types of solenoid valve can be installed defined by:
- 3/2 (3 ways, 2 positions) and 5/2 (5 ways, 2 positions).
- Power supply: 230 V AC, 110 V AC, 24 V AC, 24 V DC, 12 V DC.
- Monostable / bistable.
See the specific manual for more options.
Optionally, the solenoid valve can be sold included with the actuator; it can then be assembled in the factory attached to the actuator
(NAMUR VDE/VDI 3845 standard).
6.6 RELIEF REGULATORS
Cepex strongly recommend relief regulators be installed so as to control the actuator’s operating speed and prevent water hammer. The
silencer can be included within the relief regulator.
If the valve is installed correctly pointing in the direction of flow marked on the body, it is possible to carry out the maintenance downs-
tream without any problems. By simply closing the valve this acts as a plug. If on the contrary maintenance is required upstream, it is
essential that there is no pressure in the circuit when dismantling the union nut and end connector.
The operations described below should always be carried out without any fluid in the line.
The valve is adjusted in the factory for correct and prolonged operation. Nevertheless, the tightening of the sealing gasket on the ball can
be readjusted when the conditions of use so require it.
This operation should be carried out with the help of the tool provided (Fig. 18.1).
Dismantle the valve’s union nuts (3) and remove them from their housing. Put the tool into the slot that is found in the seal carriers for this
purpose (12) and turn the key anti-clockwise to tighten the o-ring and clockwise to loosen it. If any of the components of the valve wear
out, they can be replaced by dismantling the valve’s body. To do so, proceed in the same way as with the adjustment but turn it clockwise
until the seal carriers (12) are released. When this has been done any of the body’s O-rings may be replaced. Turn the shaft until the ball is
in a closed position; remove the ball (2) and remove the ball seats (9).
To replace the shaft, this must be forced as shown in Fig.16. Once the shaft has been removed (1) the o-rings can be replaced (7). Remem-
ber that excessive force on the seal carriers can affect the action which can damage the actual functioning of the valve.
Assembly can be done by reversing the process but always taking the precaution of lubricating the o-rings with PTFE oil. Do not use grea-
se or mineral oils that may attack the material of the o-rings.
COPYRIGHT © CEPEX, S.A.U. - ALL RIGHTS RESERVED
CODE: xxxxxxx - Version: 2016/03