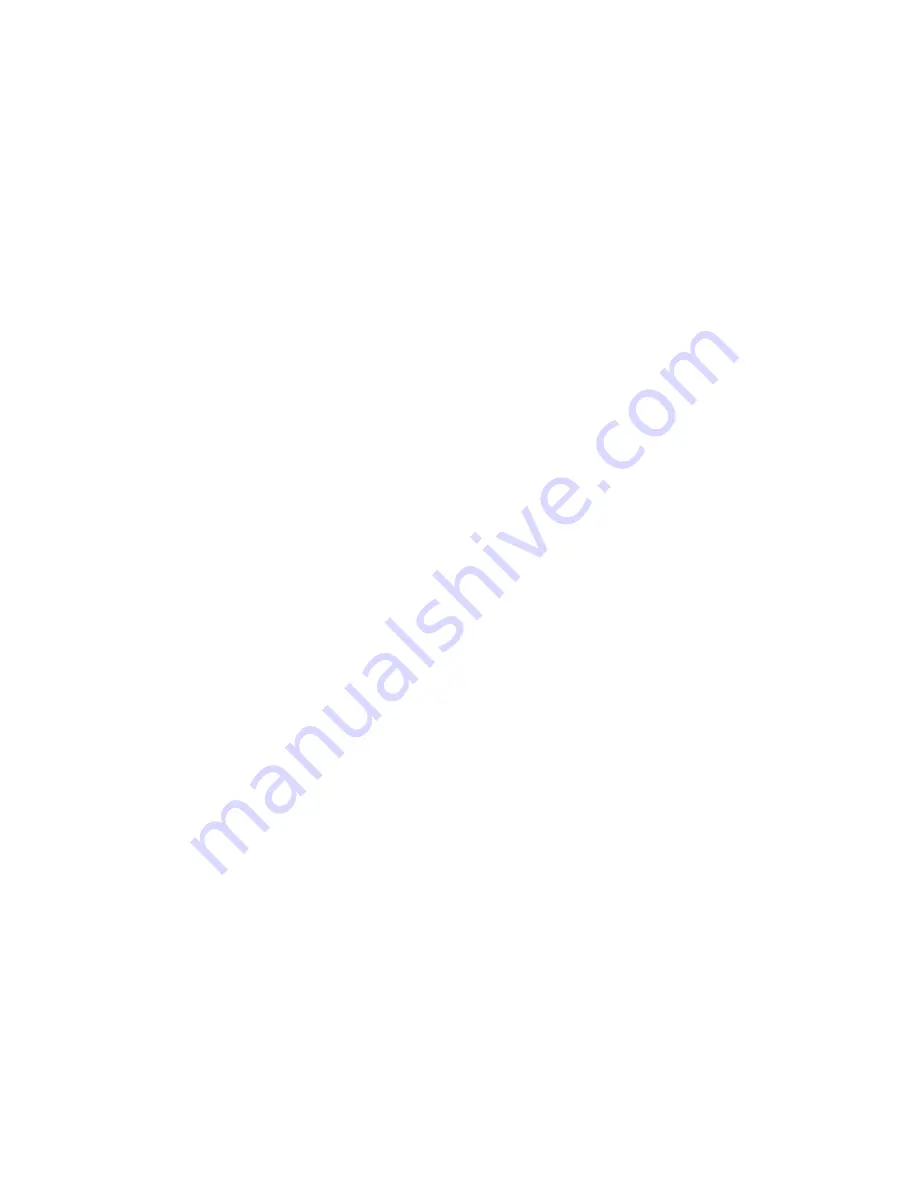
Page 5
SKU 43353
Shearing
1.
Scribe the cutting mark on the sheet metal.
2.
Slide the sheet metal between the upper Blade (23) and the lower Blade (23) so that
the upper Blade (23) is positioned directly over the cutting mark.
If additional cuts of identical size are needed, the Backstop (21) can be adjusted to the
required depth. The sheet metal will stop on the Backstop (21) when inserted. Refer to
the Adjustments section, Adjusting the Backstop.
3.
While holding the material steady, rotate the Handle Arm (18) until the material has
been cut.
For large pieces of sheet metal, it may be necessary to use a front table to support the
metal, or have someone hold it for you.
Angle Bending
1.
Mark the sheet metal where it is to be bent.
2.
Place the sheet metal above the Lower Braking Die (11).
3.
Align the bending mark with the front edge of the Upper Die (12).
If multiple bends of identical size and angle sheet metal are needed, the Backstop (21)
can be adjusted to the required depth. The sheet metal will stop on the Backstop (21)
when inserted. Refer to the Adjustments section, Adjusting the Backstop.
4.
Rotate the Handle Arm (18) until the desired angle been formed.
Use a protractor or other measuring tool to ensure accuracy.
Radius Bending
Radius bending is most commonly used to make cylinders and cones. Both shapes are
formed by making a series of small, closely spaced bends in the work piece. For cylinders,
the bends are even spaced. For cones, move one side of the sheet metal further out each
time a bend is made.
Pan Bending
The Angle Bending feature can be used to make various sizes of pans out of sheet metal.
The maximum lip (side) height is 1 inch.
1.
Pre-measure and cut your material before bending.
Notch the corners to the desired lip (side) height.
2.
Place the sheet metal above the Lower Braking Die (11).
3.
Align the bending mark with the front edge of the Upper Die (12).
4.
Rotate the Handle Arm (18) until 90 degree angle been formed.
Summary of Contents for 43353
Page 10: ...Page 10 SKU 43353...
Page 11: ...Page 11 SKU 43353 WARRANTY...