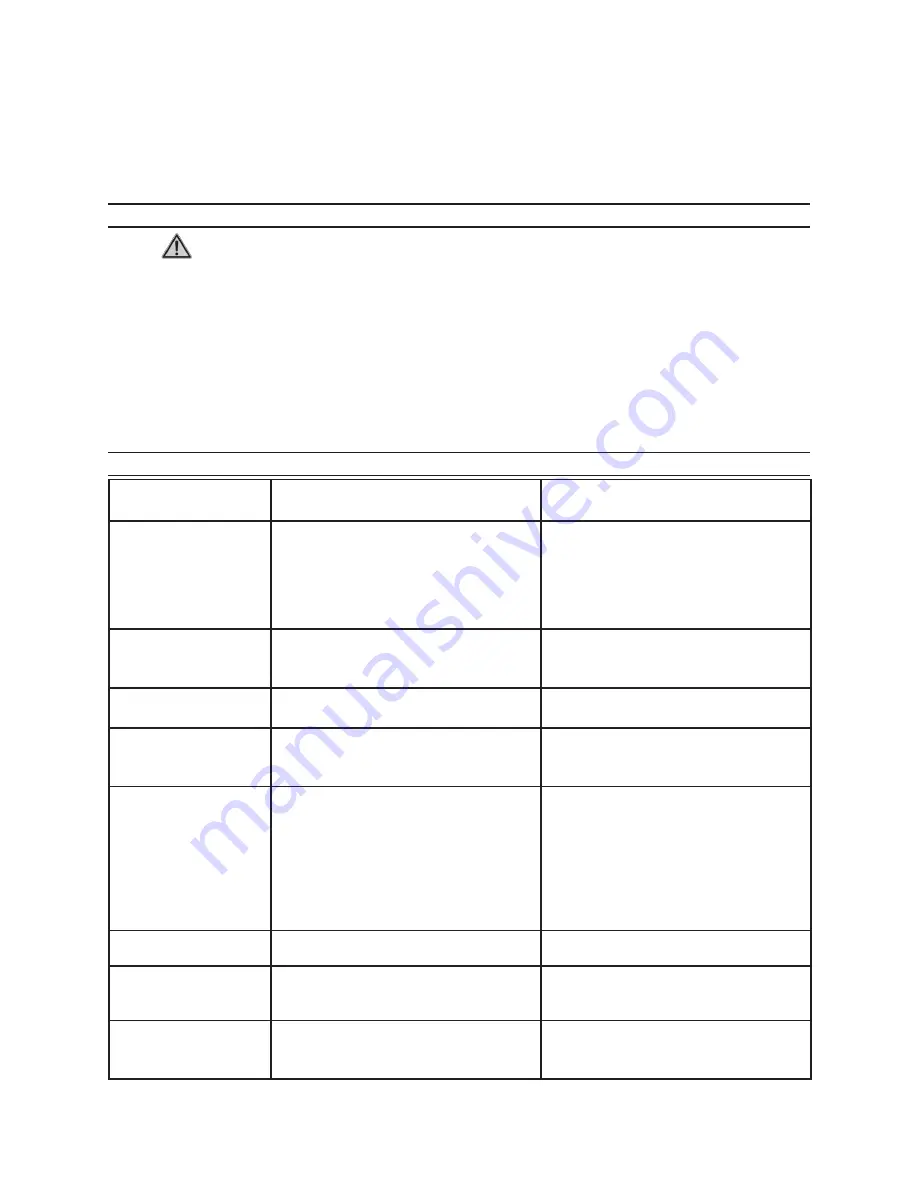
Page 17
SKU 32966
for technical questions, please call 1-800-444-3353.
NOTe:
Practise is required with this operation. It is recommended to make trial
cuts on scrap material.
INSpecTION, MAINTeNANce, AND cleANING
WARNING! Always turn the power Switch (14A) to its “Off” position and
unplug the Rabbeting Jointer from its electrical outlet prior to performing any
inspection, maintenance, and cleaning of the machine.
Before each use, inspect the general condition of the Rabbeting Jointer. Inspect
the Power Switch, Power Plug and Cord, Extension Cord (if used) for damage.
Check for loose Screws, misalignment, binding of moving parts, broken, cracked,
or improper mounting of Cutter Head Assembly and Guard. If abnormal noise or
4.
1.
2.
TROuBleSHOOTING
problem
possible causes
possible Solutions
Jointer will not start.
Fuse blown or circuit breaker tripped.
Power cord damaged.
Power cord unplugged from the power
source.
Power switch in OFF position.
1.
2.
3.
4.
Replace fuse or reset circuit breaker.
Replace power cord.
Plug in power cord.
1.
2.
3.
Overload kicks out
frequently.
Extension cord inadequate size.
Feeding stock too fast.
Cutter Head knives are dull.
1.
2.
3.
Replace cord with proper gauge.
Reduce stock feed rate.
Use only sharp knives.
1.
2.
3.
Jointer does not come up to
full speed.
Extension cord inadequate size.
Power source is not adequate.
1.
2.
Replace cord with proper gauge.
Contact local electrical utility.
1.
2.
Cuts are unsatisfactory.
Dull cutter head knives.
Gum or pitch on cutter.
Feeding work in the wrong direction.
1.
2.
3.
Sharpen or replace knives.
Remove cutter and clean with solvent.
Feed work against the cutter rotation.
1.
2.
3.
Jointer vibrates.
Cutter Head damaged.
Machine on uneven surface.
1.
2.
Replace cutter head.
Machine must rest solidly on level surface.
Bolt to floor if necessary.
Replace V-Belt.
Apply proper tension.
Replace pulley.
Motor must be properly mounted with tight
bolts and nuts.
1.
2.
3.
4.
5.
6.
Work pulled from hand.
Feeding work in wrong direction.
1.
Always feed the work against the rotation of
the cutter head.
1.
Work burns.
Cutting too deep on one pass.
1.
On hardwood, take lighter cuts. Attain full
depth with several passes.
Feed work slowly and steadily.
1.
2.
Cuts not smooth.
Feeding too fast.
Working against the grain.
Cutting too deep on one pass.
1.
2.
3.
Slow feed speed.
Work with grain whenever possible.
Take several passes on very deep cuts.
1.
2.
3.
Turn power switch to its ON position.
4.
Defective V-Belt.
3.
V-Belt incorrectly tensioned.
4.
Bent pulley.
5.
Motor mounted improperly.
6.
Brought To You By Augusta Flint