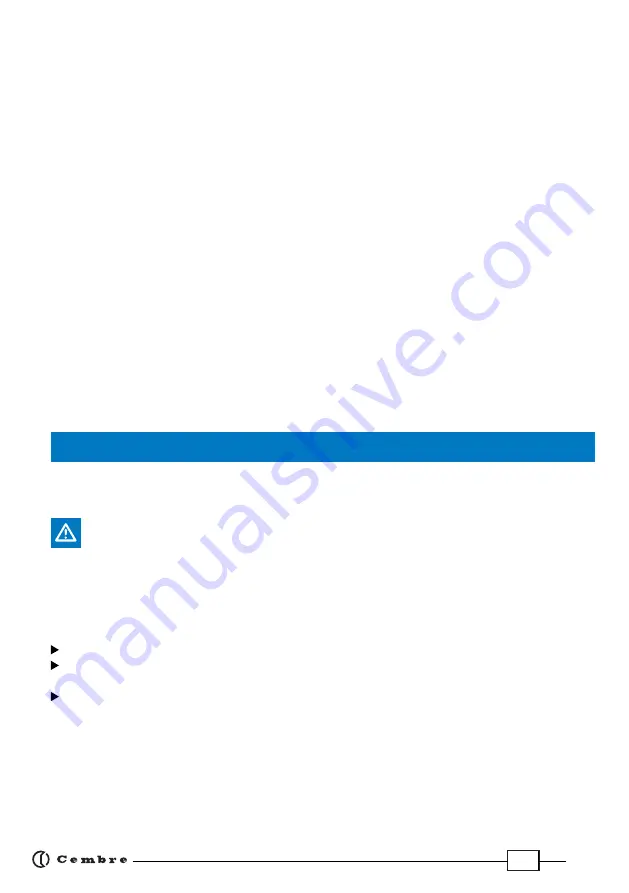
24
TROUBLESHOOTING
When the starting cable is pulled, the engine fails to start:
Is the Stop/Emergency button (17) released? (see
§ 4.4
).
Is there enough oil in the engine?
–
The engine has an oil alert system to prevent damage caused by too little oil. Before the level drops below safe
limits, the alarm system automatically stops the engine.
Refer to the
"HONDA owner’s manual"
for the recommended oil type and topping up procedure.
THE HYDRAULIC OIL SUPPLIED WITH THE MACHINE IS INTENDED ONLY FOR USE IN THE HYDRAULIC PUMP AND MUST
NOT BE USED IN THE ENGINE.
Is the fuel stopcock open?
Is there fuel in the tank?
Is fuel reaching the carburettor?
– To check, loosen the carburettor drainage screw with fuel stopcock open and refer to the
"HONDA owner’s manual".
Is the spark plug producing a spark?
– Remove the plug cap, clean around the plug and remove it using the spanner provided.
– Fit the plug back in the cap.
– Move button (17) to
"ON"
.
– Earth the side electrode then pull the starting cable and check to see if the plug produces a spark.
If the engine still fails to start, contact
Cembre
(see
§ 9
).
8.
MAINTENANCE
All electrical and mechanical maintenance shall only be carried out by authorised persons in accordance
with a safe system of work and
Cembre
instructions.
Before servicing or removing any parts of the machine, stop the engine and allow it to cool. Always
remove the spark plug cap from the spark plug when servicing the engine to prevent accidental starting.
8.1) Routine maintenance of the machine
At the end of each day, wipe the machine carefully using a clean cloth, being careful to eliminate all dirt, espe-
cially near the moving parts such as the clamp teeth, piston rods and wheels. Do not rest the machine or units
directly on dusty or muddy ground.
Regularly perform the following operations or inspections:
Tighten all bolts.
Check the integrity of the rubber dampers under the engine and pump, and on top of the clamp unit which
reduce vibration caused by those components.
Replace the insertion teeth (40) and contrast feet (41) as these become worn or damaged by long or improper
use.
8.1.1) Maintenance of braking system
The braking system is of robust construction and will require very little maintenance, however the following
routine checks should be performed.
Dust, sand and dirt are a danger for any mechanical device. Avoid putting the machine on muddy ground.
After every use, the machine must be wiped with a clean cloth, taking care to remove any residue, especially
around moving parts.