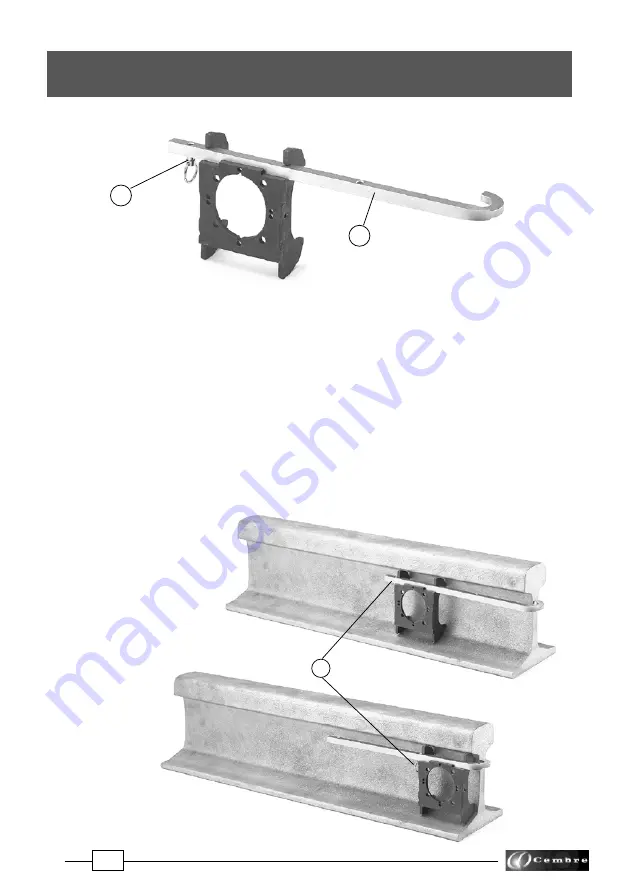
23
02
11.1.1)
Fit the
MPAF...
positioning template corresponding to the rail to be drilled (see § 7.3).
11.1.2)
Insert the
SPA...
positioning plate (03) relating to the rail to be drilled in the appropriate
housing (see Fig. 21).
11.1.3)
Insert the locking pin (02) in one of the two holes of the connection plate.
11.1.4)
With the spindle fully withdrawn position the drill close to the rail head without clamp-
ing it.
11.1.5)
Slide the drill so that:
– the curved end of the SPA... plate is flush against the rail head.
– the MPAF... positioning template is flush against the locking bolt (02).
11.1.6)
Clamp the drill in this position by tightening the handwheel fully, and commence drilling
(see § 8.1).
11.1.7)
To drill the second hole in the rail, repeat operations 11.1.5 - 6 with the locking pin (02)
inserted in the second hole of the
SPA...
plate.
11.1) Instruction for drilling close to rail heads
FIG. 21
02
03
For clarity the drilling
machine is not shown.
FIG. 22 – POSITIONING
11. SPA... POSITIONING PLATE