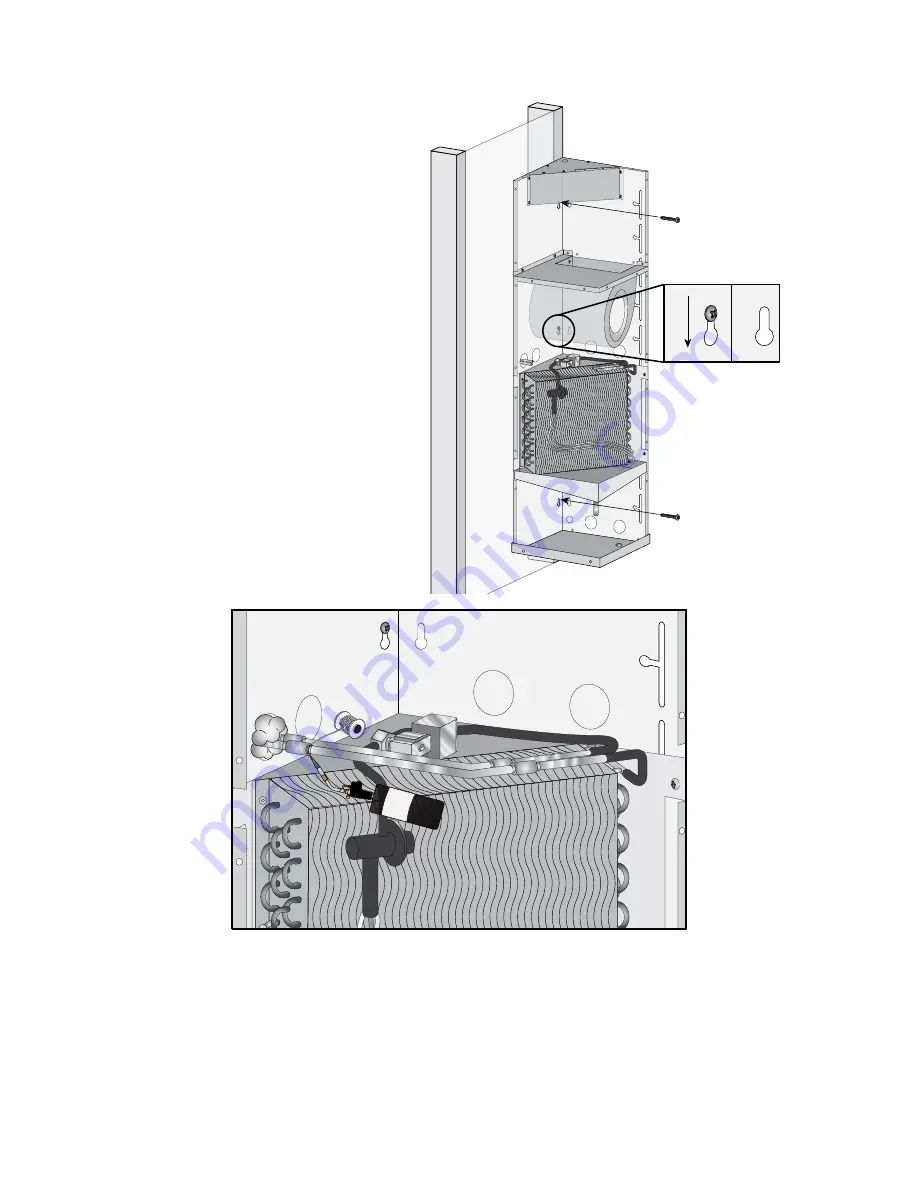
www.cellarcool.com | Page 17
Secure the evaporator unit by installing a screw
in both the upper and lower key holes that
align with the pilot holes. Tighten all mounting
screws once the evaporator unit has been set
in place.
VERTICAL MOUNT INSTALLATION
Using proper practices and procedures for brazing refrigeration tubing: Purge nitrogen in to the system,
braze the large tube of the line set to the suction line outlet and small tube to the liquid line inlet at the
evaporator. Pressurize the system to 200 PSIG for 30 minutes to verify the system is sealed. Once complete,
insulate the exposed suction line in the evaporator unit using Armaflex Insulation.
Note: If the liquid line is going to sit in an area with direct sunlight or high ambient temperatures,
insulation on the liquid line is recommended. DO NOT INSULATE the suction line and liquid line
with direct copper to copper contact. Each line needs to be insulated individually. Seal entry hole
using expanding foam insulation.
Refer to page 26 for proper wiring of the twin
system evaporator units.