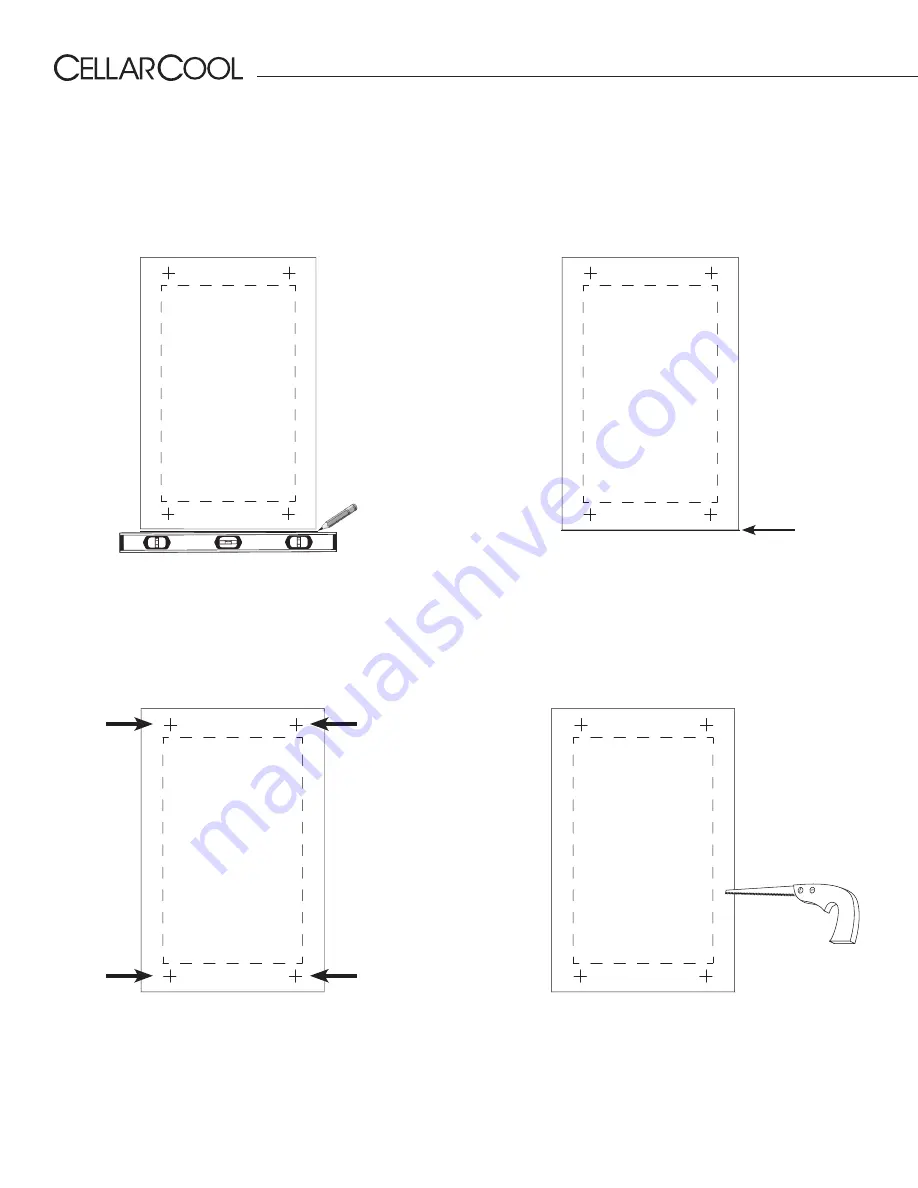
Page 26 | 1-800-343-9463
CCM9000
101017
1 . Square the flush mount template on the wall
using a level . Then draw a 3” line along the
bottom edge of the template .
FLUSH MOUNT BRACKET INSTALLATION
TOP
TOP
2 . Peel the backing off the template and stick it to the wall,
aligning the bottom edge with the line drawn in Step 1 .
Pencil line
TOP
TOP
3 . Use a 5/16” drill bit to drill a hole in the center of
each cross (+) .
4 . Cut along the perforated lines . When finished, remove
template from wall .
INSTALLING THE EVAPORATOR
1.
Locate the desired installation location.
2.
Place the external drip tray on a level surface. Place a vibration isolator on each end of three of the drip tray risers.
The vibration isolator needs to be pushed up against the outer lip on the top of the risers. Each vibration isolator
should be spaced about 17.5” apart. Center the evaporator unit on the vibration isolators.
Minimum Tools Needed:
Saw
T-square
Drill
¼” nut driver bit
Level
5⁄16” nut driver bit
CPVC tube cutter
3.
galvanized hanging straps. (NOTE: Plumber’s tape/hanger strap not provided.) Cut four pieces of galvanized
hanging straps long enough to extend from the ceiling joists to the screws located at the top corners of the
evaporator unit.
4.
If using a drill, set drill to 8 lbs. of torque to prevent stripping out the screw holes.
5.
Using a 5⁄16” hex head nut driver, remove (1) screw from the top corner of the evaporator unit and route the
screw through the appropriate hole on the hanger strap. Re-install the removed screw. Secure the free end of the
hanger strap to the ceiling joist to prevent the evaporator unit from moving out of place. Repeat this step for the
remaining three corners.
Vibration isolator
Drip tray
Hanger strap
31”
51”
17.5”
Ceiling joist
Plywood
Vibration isolator
Use a stud finder to locate the ceiling joists. The ceiling joists will be the mounting surface for one end of the