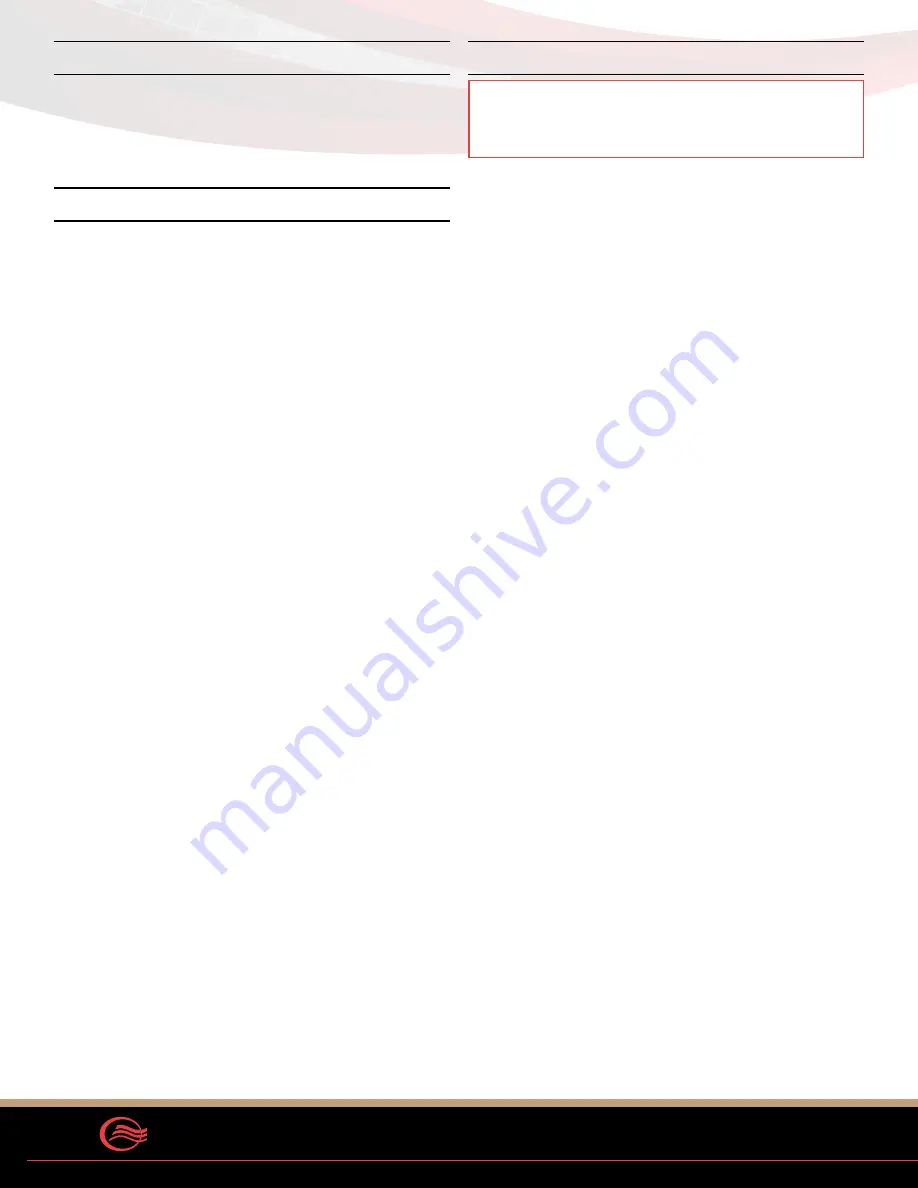
Fastrax
TM
1.855.244.3128
Fax: 1.303.979.7350
www.fastraxind.com
60
I.12 MOVABLE POINT FROG HEATING
Contact Fastrax or review the bill of material for proper mov-
able point frog heater selection.
J. PROCEDURES
J.1 GENERAL OPERATION
GENERAL OPERATION
1.
Fastrax
®
Switchblade
®
style track switch, crib
heaters, spring frog rail heaters and movable point
frog heaters are engineered for state of the art
heat transference and are ruggedly designed and
constructed for endurance.
2.
When properly installed, operated and maintained,
they will provide long life and dependable, trouble-
free service. The flattened stainless steel heater
style is extremely efficient and durable.
3.
When energized at the rated voltage, each heater
will operate at the nameplate wattage and transfer
heat to the rail or crib area it is attached to.
4.
Flat heaters are attached to the rail or crib platform
with XTC spring style clamp assemblies that will
expand and contract while maintaining excellent
contact with the metal and readily transfer heat
bringing the rail or platform above freezing
temperatures.
5.
Once above freezing, the heat from the rail or platform
will radiate warmth to melt existing or accumulating
snow and ice in the track switch, spring frog wing,
movable point frog rail, or crib area.
6.
When controlled with a Fastrax
®
control panel
system the switch heaters will operate in an energy
saving mode but only after snow has stopped falling.
7.
The energy saving mode will continue to operate
the spring frog, movable point frog and crib heaters
at full nameplate rated wattage while the switch
heaters will function at 25% of their rated wattage
for an adjustable time period.
8.
If snow begins to fall again all heaters automatically
return to full output.
J.2 INSTALLATION PROCEDURE
Note:
Do not operate heaters at voltages in excess
of that stamped on the heater. Excess voltage will
shorten heater life.
1.0
SWITCHBLADE
®
AND CRIB HEATERS
1.
Switch Heaters:
•
After equipment selection is made and
installation side of rail is determined, reference
the System Layout and Rail Heater sections
(page 9) of this manual. When installing heaters,
they should be located on the rail web extending
from a point approximately 2 ft ahead of the
switch toward the heel block.
2.
SwitchBlade
®
Heater Clamp Positioning:
•
Layout the proper clamp locations for the
heaters. Be certain that clamp locations are
placed approximately 24” on center following
the Rail Heater section of this manual
•
Avoid locating clamps where braces, signal
wires, or other apparatus is blocking access to
the rail web.
•
If existing braces are not of the notched style as
shown in drawings
•
Replace braces with the notched style or contact
engineering or Fastrax Industries for optional
installation methods.
3.
SwitchBlade
®
Heater Clamping:
•
Type FRB600 spring base style rail clamps
should be used to allow the heater to maintain
close contact with the rail while permitting normal
expansion and contraction. Install clamps by
hand and assemble on heater as described in
the Rail Heater section of this manual.
4.
Crib Heaters:
•
Clear ballast from between the ties below the
switch rods. Allow for a minimum of 4” from the
base of the rail to the top of the FCH Crib Heater
platform. Always mount top of Crib Heater
platform to allow proper clearance for free
operation of switch rods. Place heater platform
in the desired position to maintain a snow and
ice-free area below the operating switch rods.
Install as outlined in the Crib Heater section of
this manual. Replace ballast in area around crib
heater.
5.
SwitchBlade
®
Heaters for Frog:
•
Install all frog heaters as covered in this manual.