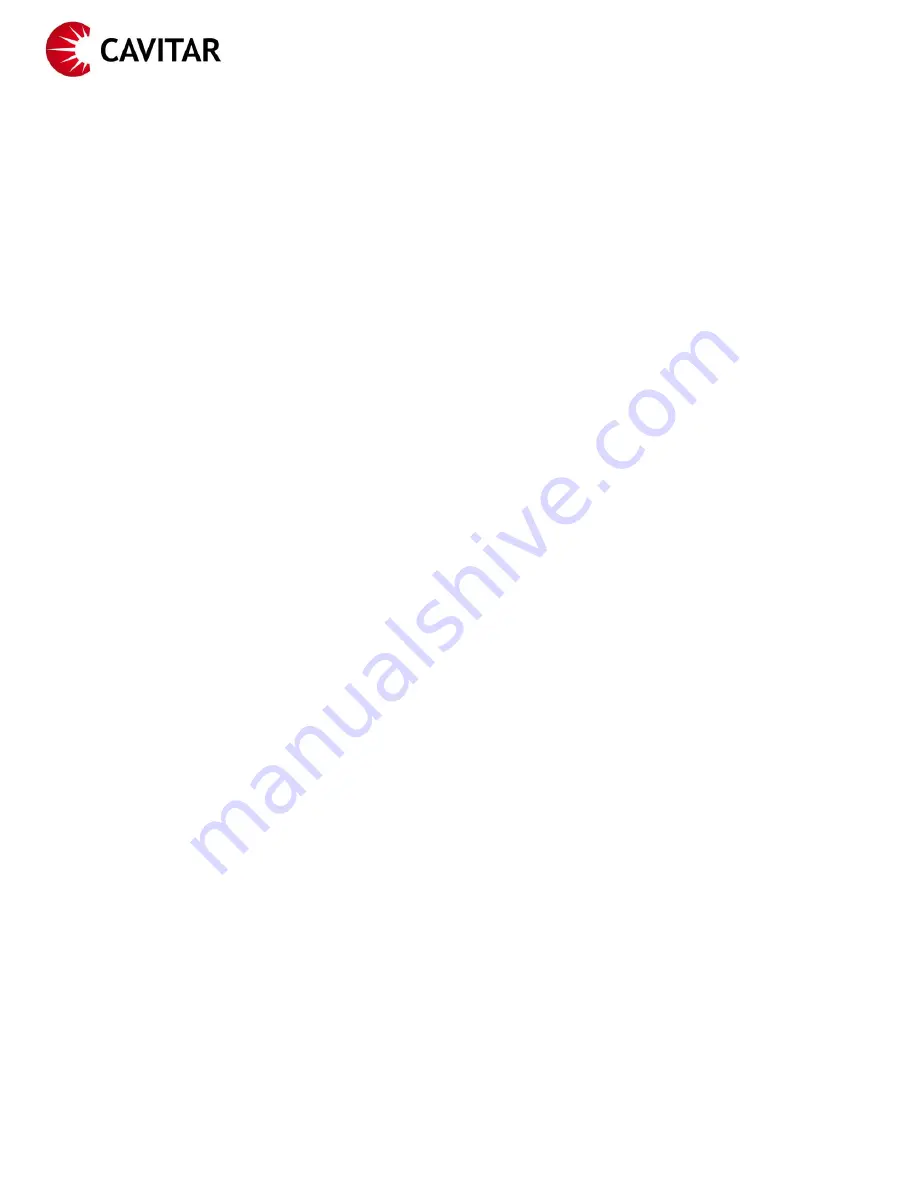
Page
8
of
22
2.2
Mounting to machinery
The simplest and most compact passive cooling solution is to mount the camera to the welding machinery
with a thermally conductive mount. For optimal results the following guidelines should be followed:
•
The mount should be made of high thermal conductivity material such as aluminium or copper
•
The mount should cover the entire side of the camera (for maximal heat transfer the camera can
be mounted from both sides)
•
Thermally conductive sheet should be applied between the camera side(s) and the mount(s) as
well as between the mount(s) and welding machinery
•
The connection point of the mount to the welding machinery should be in such a location where
the temperature of the welding machinery is as low as possible (however, the temperature of the
heat sink mustn’t be so low that condensation could take place inside the camera)
. Possible
mounting locations could be e.g. the metallic body of the welding machinery (roughly at the
ambient temperature) or some cooled component/location of the machinery, if available
•
The contact area between the mount and welding machinery should be sufficiently large
(preferably at least similar contact area as between the mount and the camera)
•
It is possible to reduce the effect of external heat loads by adding thermal insulation around the
camera and the mount (e.g. thermally insulating sleeve)
2.3
Heat sinks
Cavitar offers dedicated heat sinks (see Section 2.2 for mounting details) that can be applied if passive
cooling is sufficient but there is no suitable mounting location in the welding machinery.
In principle proper mounting to machinery can be more efficient than using separate heat sinks since the
temperature of the welding machinery is typically not affected by the heat generated by the camera while
the separate heat sinks get warm. Gradually thermal equilibrium will be obtained when the heat sinks
receive the same heating power from the camera as what they release to the surrounding air.
Since the cooling is based on heat transfer from the heat sinks to the surrounding air, thermal insulation
around the heat sinks can’t be
applied (unlike in Section 2.2). The efficiency of the heat sinks is improved
if air can flow properly at the surfaces of the heat sinks. This is shown in Fig. 2.10.
The mechanical dimensions of the heat sinks for Cavitar Welding Camera C300 are shown in Fig. 2.11.
Similar heat sinks are available for C400 series.