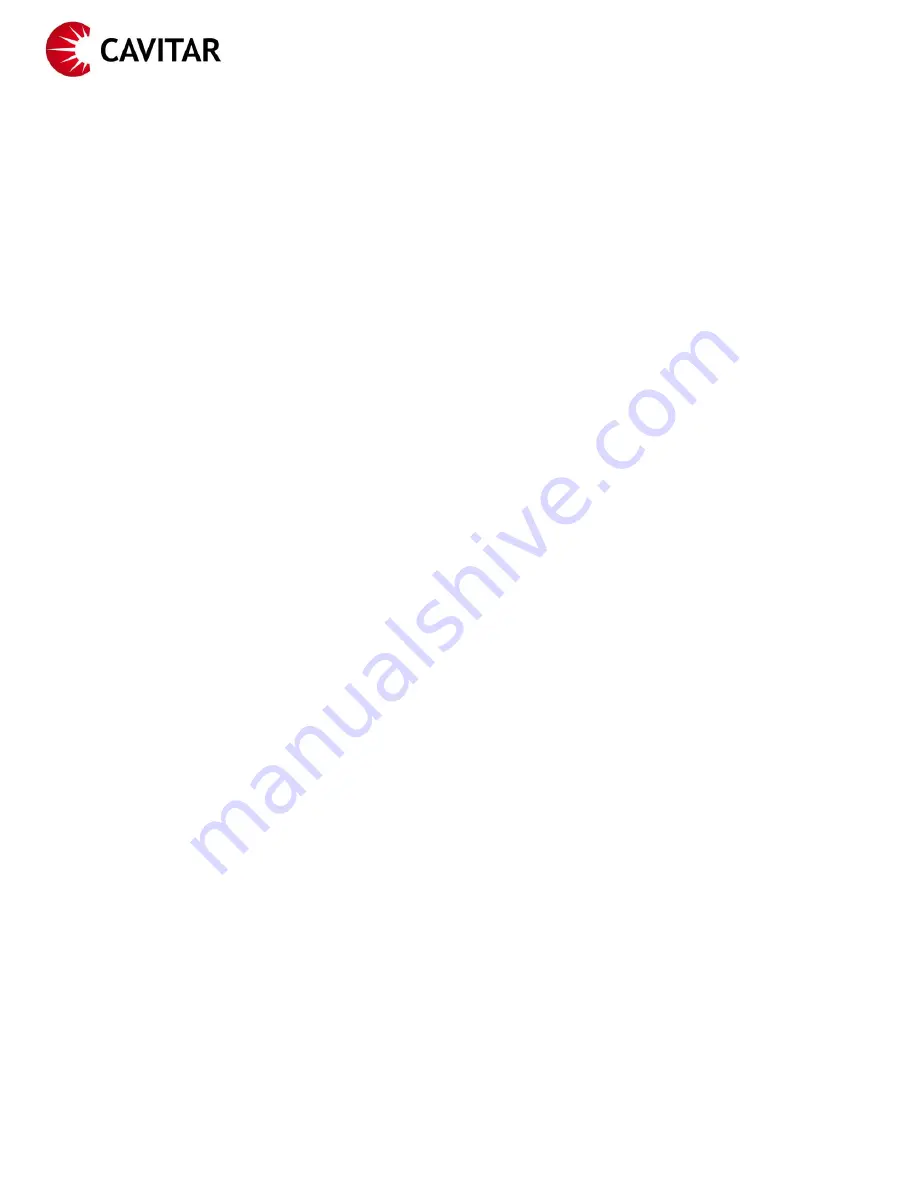
Page
2
of
22
1.
Introduction
This guide provides information about the cooling of Cavitar Welding Cameras (C300 and C400 series;
standard models with GigE interface) and is intended to be used together with the applicable operation
manual. The general principles of this guide also apply to the high-speed versions of Cavitar Welding
Cameras (USB3 interface). However, since the high-speed versions typically generate more heat than the
standard versions, the applicability of passive cooling is more limited with the high-speed version as
compared to the standard version. All tests have been made with Cavitar Welding Camera C300, but the
results and conclusions apply also to Cavitar Welding Camera C400 series. All results are indicative.
There are numerous different welding processes and welding environments. Therefore also the cooling
requirements can vary substantially from case to case. Typically the following sources of heat must be
dealt with:
•
Internal heat load generated by the camera itself
•
External heat load generated by elevated ambient temperature
•
External heat load generated by the welding process
Due to the internal heat generated by the camera electronics, heat must be transferred from the camera
to an external heat sink even in normal ambient temperature (25 °C). In such a situation it is usually
sufficient to mount the camera from the sides with an articulated arm having a metallic clamp.
Cavitar Welding Cameras have built-in safety measures for warning about increasing camera temperature.
With C300 series the camera temperature is shown in Cavitar Capture software and warnings will be
displayed on the screen (see the C300 operation manual for more details). With C400 series warnings are
generated by a separate temperature warning unit (see the C400 operation manual for more details).
Appropriate cooling will increase the lifetime of the camera. However, at the same time it is important to
keep the camera temperature above dew point to avoid condensation. Depending on the total heat load
either passive cooling (Chapter 2) or active cooling (Chapter 3) is needed.
2.
Passive cooling
Passive cooling is the simplest solution in situations where the external heat load is relatively small. As an
example we can consider a welding process with relatively short duration and small heat output under
ambient temperatures up to ~35 °C.
With passive cooling the aim is always to move the heat conductively from the camera to a separate heat
sink(s). In order to achieve efficient passive cooling the thermal conductivity from the camera to the heat
sink(s) must be maximized. The camera has been designed in such a way that the heat generated inside
the camera can reach the outer surface of the camera housing (especially both sides) as efficiently as
possible. This heat, as well as any additional external heat load, is then transferred to a heat sink(s).
Some important topics related to passive cooling are discussed in Sections 2.1
–
2.3 in more detail.