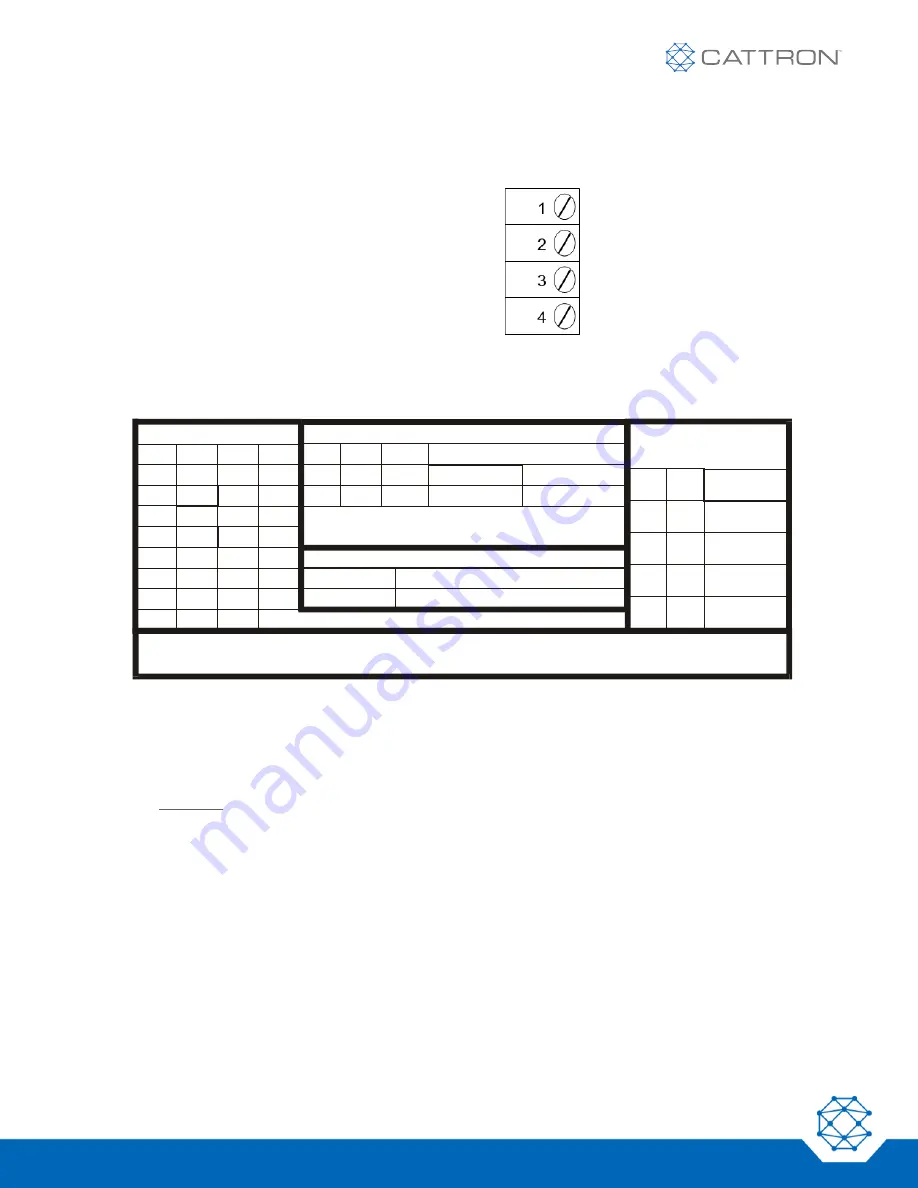
DynaGen
TM
ES52 - EN
User Manual
13
9M02-9253-A001-EN
Revision A
Potentiometers are shown in
as they appear on the rear of the ES52 series units.
label on the rear of these units.
1 – Crank Disconnect
2 – Over-Speed
3 – Crack / Rest
4 – Timer
Figure 3: Potentiometers
Figure 4: Label on Rear of ES52 Series Units
“
Oil
Bypass
” period refers to the delay period (fixed at 15 seconds for 1-3 crank tries and 20 seconds for more
than 3 crank tries) immediately after the Engine Running LED illuminates (engine starts). During this period the
oil input is bypassed (ignored).
3.5.1 Factory Settings
The ES52 is set up with the following settings from the factory:
•
20 Hz / 300 Hz Crank Disconnect in low- or high-speed mode respectively
•
10 s Crank / Crank Rest
•
10 s Timer output; Timer set to preheat functionality
•
DIP switches 1 and 2 ON; all others OFF
CRANK TRIES
S1 S2 S3
off
on
off off
on
on
on
on
on-Enabled
on on
#
1
2
3
4
5
6
setup
off
on
on
on
TIMER
SPEED SETTING
off off
S4 S5
Slow
Choke
- single crank attempt - 4 to 256 sec
Range
on on
off off lo
hi
CRDC
OVSP
12 - 140
44 - 300
60 - 4156 300 - 8492
S6
off
on
Enabled
CRDC - Crank Disconnect (Hz)
OVSP - Overspeed (Hz)
(52 Model Only)
on
off on
off
on
off
on
off
off
off
off
CRANK TRIES
LOSS OF SPEED
WHILE CRANKING
S1 S2 S3
off
on
off off
on
on
on
#
1
2
3
4
5
6
off
on
on
on
TIMER
SPEED SETTING
off off
OIL VERIFICATION
S4 S5
Glow Plug
on on
off off lo
hi
CRDC
OVSP
12 - 140
44 - 300
60 - 4156 300 - 8492
off
on
Disabled
S7 S8
S9
(52 Model Only)
Airgate
off
off off
Setting
on
off
off-Disabled
on
off
on
off
off
off
off
on
Summary of Contents for DYNAGEN ES52
Page 1: ...ES52 User Manual ...