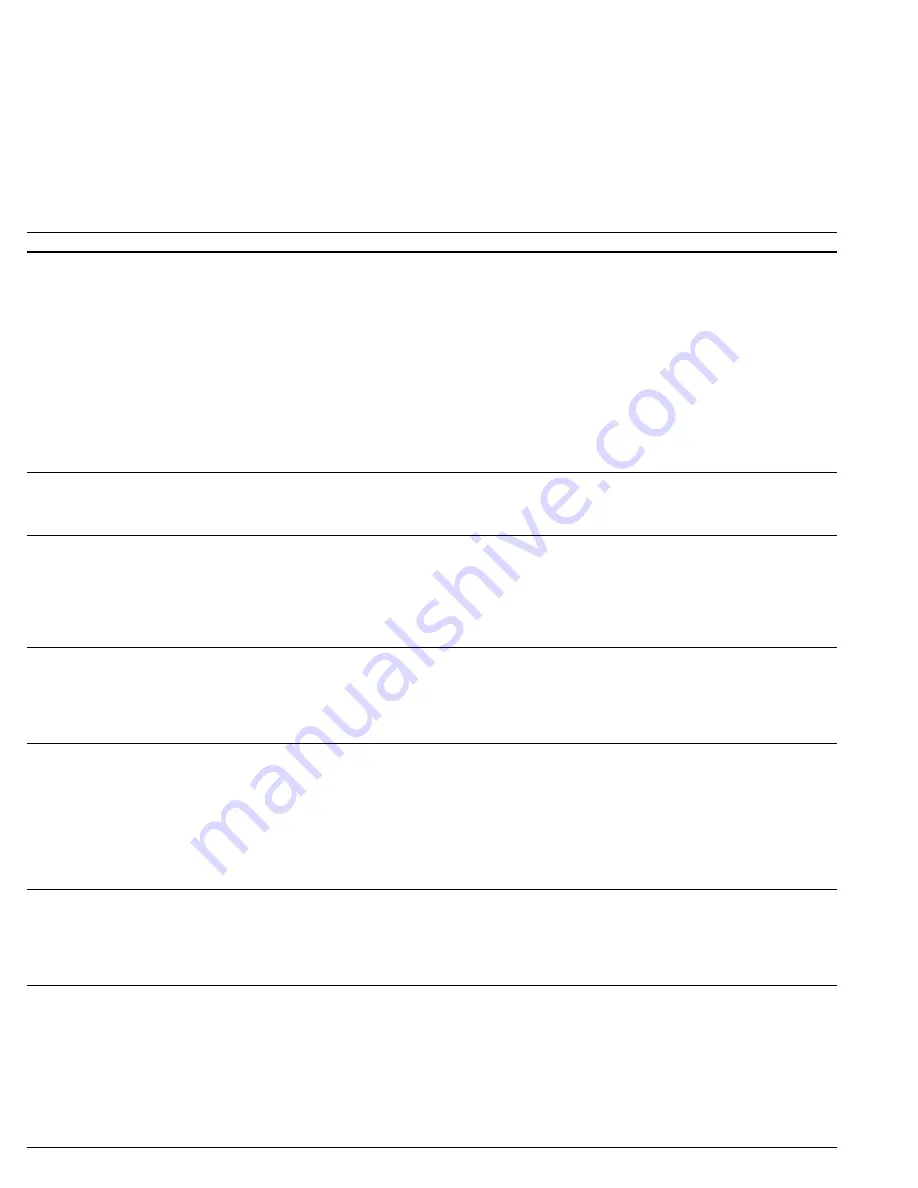
DIAGNOSIS AND MAINTENANCE
One of the most important steps in a high pressure system is to establish a regular maintenance program. This will vary slightly with each
system and is determined by various elements such as the duty cycle, the liquid being pumped, the actual specifications vs rated specifications
of the pump, the ambient conditions, the inlet conditions and the accessories in the system. A careful review of the necessary inlet conditions
and protection devices required before the system is installed will eliminate many potential problems.
CAT PUMPS are very easy pumps to service and require far less frequent service than most pumps. Typically, only common tools are required,
making in-field service convenient, however, there are a few custom tools, special to certain models, that do simplify the process. This service
manual is designed to assist you with the disassembly and reassembly of your pump. The following guide will assist in determining the cause
and remedy to various operating conditions. You can also review our FAQ or SERVICE sections on our WEB SITE for more facts or contact
CAT PUMPS directly.
PROBLEM
PROBABLE CAUSE
SOLUTION
Low pressure
•Worn nozzle.
•Replace with properly sized nozzle.
•Belt slippage.
•Tighten belt(s) or install new belt(s).
•Air leak in inlet plumbing.
•Tighten fittings and hoses. Use PTFE liquid or tape.
•Pressure gauge inoperative or not registering accurately.
•Check with new gauge. Replace worn or damaged gauge.
•Relief valve stuck, partially plugged or improperly adjusted.
•Clean/adjust relief valve. Replace worn seats/valves and o-rings.
•Inlet suction strainer (filter) clogged or improperly sized.
•Clean filter. Use adequate size filter. Check more frequently.
•Abrasives in pumped liquid.
•Install proper filter.
•Leaky discharge hose.
•Replace discharge hose with proper rating for system.
•Inadequate liquid supply.
•Pressurize inlet and install C.A.T.
•Severe cavitation.
•Check inlet conditions.
•Worn seals.
•Install new seal kit. Increase frequency of service.
•Worn or dirty inlet/discharge valves.
•Clean inlet/discharge valves or install new valve kit.
Pulsation
•Faulty Pulsation Dampener.
•Check precharge. If low, recharge, or install a new dampener.
•Foreign material trapped in inlet/discharge valves.
•Clean inlet/discharge valves or install new valve kit.
Water leak
•Under the manifold
•Worn V-Packings or Lo-Pressure Seals.
•Install new seal kit. Increase frequency of service.
•Worn adapter o-rings.
•Install new o-rings.
•Into the crankcase
•Humid air condensing into water inside the crankcase.
•Install oil cap protector. Change oil every 3 months or 500 hours.
•Excessive wear to seals and V-Packings.
•Install new seal kit. Increase frequency of service.
Knocking noise
•Inlet supply
•Inadequate inlet liquid supply.
•Check liquid supply. Increase line size, pressurize or install C.A.T.
•Bearing
•Broken or worn bearing.
•Replace bearing.
•Pulley
•Loose pulley on crankshaft
•Check key and tighten set screw.
Oil leak
•Crankcase oil seals.
•Worn crankcase oil seals.
•Replace crankcase oil seals.
•Crankshaft oil seals and o-rings.
•Worn crankshaft oil seals or o-rings on bearing cover.
•Remove bearing cover and replace o-rings and/or oil seals.
•Drain plug
•Loose drain plug or worn drain plug o-ring.
•Tighten drain plug or replace o-ring.
•Bubble gauge
•Loose bubble gauge or worn bubble gauge gasket.
•Tighten bubble gauge or replace gasket.
•Rear cover
•Loose rear cover or worn rear cover o-ring.
•Tighten rear cover or replace o-ring.
•Filler cap
•Loose filler cap or excessive oil in crankcase.
•Tighten filler cap. Fill crankcase to specified capacity.
Pump runs extremely rough
•Inlet conditions
•Restricted inlet or air entering the inlet plumbing
•Correct inlet size plumbing. Check for air tight seal.
•Pump valves
•Stuck inlet/discharge valves.
•Clean out foreign material or install new valve kit.
•Pump seals
•Leaking V-Packings or Lo-Pressure seals.
•Install new seal kit. Increase frequency of service.
Premature seal failure
•Scored plungers.
•Replace plungers.
•Over pressure to inlet manifold.
•Reduce inlet pressure per specifications.
•Abrasive material in the liquid being pumped.
•Install proper filtration at pump inlet and clean regularly.
•Excessive pressure and/or temperature of pumped liquid.
•Check pressure and inlet liquid temperature.
•Running pump dry.
•DO NOT RUN PUMP WITHOUT LIQUID.
•Starving pump of adequate liquid.
•Increase hose one size larger than inlet port size. Pressurize and
install C.A.T.
•Eroded manifold.
•Replace manifold. Check liquid compatibility.