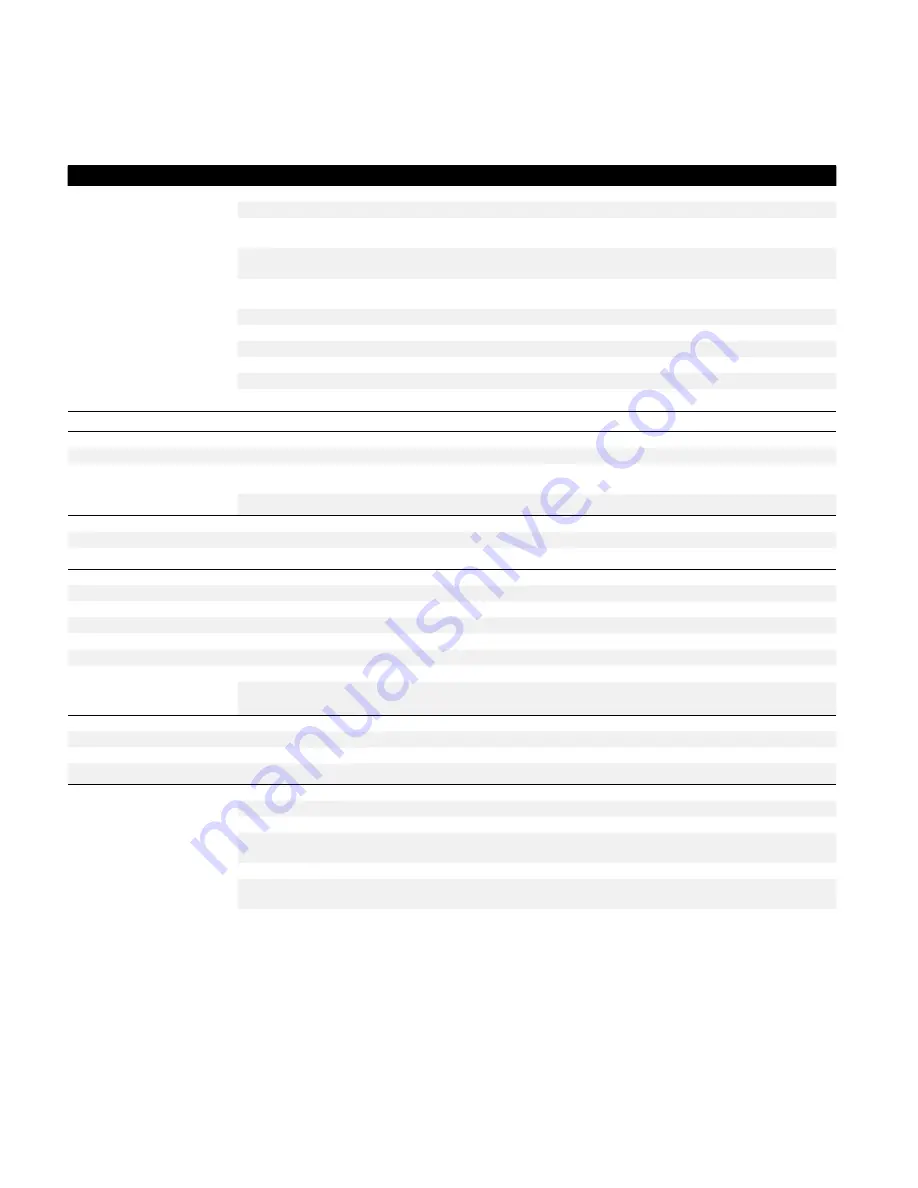
PN 99MAN006 Rev A 4/21
PROBLEM
PROBABLE CAUSE
SOLUTION
Low pressure
• Worn nozzle.
• Replace with proper size nozzle.
• Air leak in inlet plumbing.
• Tighten fittings and hoses. Use PTFE liquid or tape.
• Pressure gauge inoperative or not registering
accurately.
• Check with new gauge. Replace worn or
damaged gauge.
• Relief valve stuck, partially plugged or improperly
adjusted.
• Clean/adjust relief valve. Replace worn seats/valves
and O-rings.
• Inlet suction strainer (filter) clogged or
improperly sized.
• Clean filter. Use adequate size filter. Check more
frequently.
• Abrasives in pumped liquid.
• Install proper filter.
• Leaky discharge hose.
• Replace discharge hose with proper rating for system.
• Inadequate liquid supply.
• Pressurize inlet.
• Severe cavitation.
• Check inlet conditions.
• Worn seals.
• Install new seal kit. Increase frequency of service.
• Worn or dirty inlet/discharge valves.
• Clean inlet/discharge valves or install new valve kit.
Pulsation
• Foreign material trapped in inlet/discharge valves.
• Clean inlet/discharge valves or install new valve kit.
Water leak
• Under the manifold
• Worn high-pressure or low-pressure seals.
• Install new seal kit. Increase frequency of service.
• Into the crankcase
• Humid air condensing into water inside the crankcase.
• Install new oil cap protector. Change oil every 3 months
or 500 hours.
• Excessive wear to high-pressure or low-pressure seals.
• Install new seal kit. Increase frequency of service.
Knocking noise
• Inlet supply
• Inadequate inlet liquid supply.
• Check liquid supply. Increase line size or pressurize.
• Bearing
• Broken or worn bearing.
• Replace bearing.
Oil leak
• Crankcase oil seal
• Worn crankcase oil seal.
• Replace crankcase oil seal.
• Crankshaft oil seal and O-ring
• Worn crankshaft oil seal or O-ring on bearing cover.
• Remove bearing cover and replace O-ring and/or oil seal.
• Drain plug
• Loose drain plug or worn drain plug O-ring.
• Tighten drain plug or replace O-ring.
• Bubble gauge
• Loose bubble gauge or worn bubble gauge gasket.
• Tighten bubble gauge or replace gasket.
• Bearing cover
• Loose bearing cover or worn bearing cover O-ring.
• Tighten bearing cover or replace O-ring.
• Filler cap
• Loose filler cap or excessive oil in crankcase.
• Tighten filler cap. Fill crankcase to specified capacity.
• Excessive pump RPM.
• Consult pump data sheet for maximum pump RPM.
Change pulley sizes or motor/engine RPM.
Pump runs extremely rough
• Inlet conditions
• Restricted inlet or air entering the inlet plumbing.
• Correct inlet size plumbing. Check for air tight seal.
• Pump valves
• Stuck inlet/discharge valves.
• Clean out foreign material or install new valve kit.
• Pump seals
• Leaking high-pressure or low-pressure seals.
• Install new seal kit. Increase frequency of service.
Premature seal failure
• Scored plunger.
• Replace plunger.
• Over pressure to inlet manifold.
• Reduce inlet pressure per specifications.
• Abrasive material in the liquid being pumped.
• Install proper filtration at pump inlet and clean regularly.
• Excessive pressure and/or temperature of
pumped liquid.
• Check pressure and inlet liquid temperature.
• Running pump dry.
• DO NOT RUN PUMP WITHOUT LIQUID. Fill pump with oil.
• Starving pump of adequate liquid.
• Increase hose one size larger than inlet port size
or pressurize.
• Eroded manifold.
• Replace manifold. Check liquid compatibility.
Diagnosis and Maintenance
This service manual is designed to assist you with the disassembly and reassembly of your pump. The following guide will assist in determining
the cause and remedy to various operating conditions. You can also review our FAQ or SERVICE & TRAINING sections on our WEB SITE for more
facts or contact Cat Pumps directly.
CAT PUMPS
1681 94th Lane N.E., Minneapolis, MN 55449-4324 P: (763) 780-5440 F: (763) 780-2958 E: [email protected] www.catpumps.com
©2021 Cat Pumps Inc. All rights reserved. All data contained in this document are based on the latest product information available at the time of publication. Cat Pumps reserves the right to make changes at any time without notice.